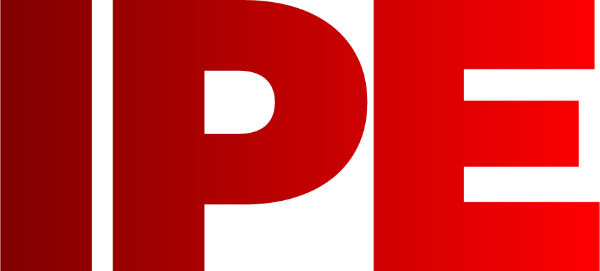
![]() |
Edward Lowton
Editor |
![]() ![]() |
Home> | Plant, Process & Control | >Valves and actuators | >Withstanding the pressure of industrial tasks |
Withstanding the pressure of industrial tasks
02 December 2016
Pressure reducing valves are essential to any manufacturing system where a tight control over fluid flow and pressure is required. Steve Busby, business development director at Oxford University spin-out Oxford Flow, discusses why a return to first-principles could mean the use of valves in the industry is transformed
Process control is perhaps the single most important element of manufacturing. And when it comes to the control of gas, steam, water and other fluids, the modern factory could not function without the humble pressure reducing valve (PRV), which enables the distribution of gas and liquids at a pre-determined pressure.
Usually, this pressure reduction is enabled by a diaphragm which will constantly modulate with the changing pressure, and therefore needs to be flexible in order to provide accurate control. However, it is this very flexibility, normally enabled by a limited range of elastomers, which leads to the fatigue, erosion or embrittlement which frequently causes the – often untimely – end to the lifespan of the conventional PRV.
Not so with the new patented system of pressure reduction recently introduced to the market by Oxford Flow. Engineered in Oxford University’s Osney Thermo-Fluids laboratory, the Oxford Flow PRV replaces the diaphragm with a direct sensing piston actuator. This not only greatly simplifies the design of the regulator but also removes the main cause of failure.
How it works
One side of the piston is exposed to downstream pipeline pressure while the other side is balanced against a pressure cavity controlled by a pilot regulator. The sleeved piston actuator operates over an optimised feed-hole configuration to provide precise, stable control across the entire operating range. During operation, the piston moves inward, reducing the size of the cavity when the downstream pipeline pressure exceeds that within the pressure cavity set by the pilot regulator.
The movement of the piston actuator progressively covers the feed holes; reducing the flow rate to maintain a stable downstream pressure. When demand increases the downstream pressure falls below that set by the pilot and the reverse operation occurs; the cavity expands, as the pilot feeds it, uncovering the feed holes, which increases flow and maintains a stable downstream pressure.
Performance benefits
Extensive testing against current market-leading regulators proved that the device could match and more often out-perform the other models being used in industry, with its various performance benefits including reduced hunting, minimal droop, minimised flow turbulence and reduced minimum pressure head-drop. With noise pollution a significant health and safety issue in so many process engineering settings, the fact that it is also significantly less noisy than comparable devices is also a benefit.
When the device is deployed in the manufacturing setting, it weighs less than competitors - A 4in IHF Series weighs 10kg, whereas 2in valves from leading competitors can weigh as much as 60kg. This means that fewer technicians are necessary when the device is being installed. This low weight results in health and safety benefits too – the lower the weight the smaller the risk of injury when installing or performing maintenance.
And indeed, that maintenance needs to happen much, much less often. Because of the piston-led design and the fact that the Oxford Flow model has only one moving part, it can generally stay in service for longer than conventional diaphragm operated PRVs on the market.
In addition, the simplicity of the design means that it can also be manufactured in specialist hardened materials where it is being used to handle particularly corrosive materials (e.g. in chemicals manufacturing).
Efficient, durable valves are one of the most important weapons in the modern manufacturer’s armoury. In going back to first principles and developing an entirely new method of pressure regulation, Oxford Flow may yet have produced a game-changer.
- No related articles listed