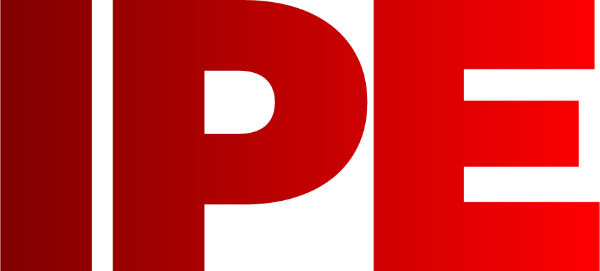
![]() |
Edward Lowton
Editor |
![]() ![]() |
Home> | Plant, Process & Control | >Valves and actuators | >Valves: To repair or to replace? |
Valves: To repair or to replace?
24 June 2013
When it comes to process, pilot and actuation valves, the question of whether it is advisable to repair or replace a worn or intermittent unit is worth considering, regardless of the type or the size. Tom Carnell, systems applications manager at Bürkert UK, comments
Starting with the smallest of solenoid-controlled valves, which are a relatively low cost item, it would usually be beneficial to replace the valve with a new component which carries the manufacturer's warranty. Bürkert solenoid valves, for example, are comprehensively tested and designed to cope with millions of operations, so rarely require replacement, even in tough operating conditions. Outside influences, beyond the design parameters of a system however occur more often than we would like to think. With some processes costing thousands of pounds per hour of downtime, a straight replacement can often be a default choice in this situation.
In contrast, large-scale butterfly and ball valves would often see repairs carried out with many serviceable parts available. These tend to be used in applications dealing with dirty or aggressive media and the bodies can be worn down by the passage of abrasive particles. The larger the valve, often the more economic a repair can be.
Usually, valve seats, seals and stem seals are available as a service kit which provides a known maintenance cost for budgeting purposes. Aggressive materials can often perish soft seals and seat materials. Valves should be specified carefully based on the medium they carry, but in many cases simple age can result in seals and seats requiring replacement in an otherwise perfectly healthy valve.
Potential downtime can affect the decision, as can issues of cleanliness and meeting ‘as new’ material specifications; especially in food, aerospace or medical applications. Often valves used in hygienic applications have recommended service intervals which are dependent on their position within the manufacturing process. This planned maintenance schedule often prevents unwanted valve failures which can cause substantial production losses.
When it comes to process valves, the medium tends to be less aggressive or at least more consistent. In this instance each component is replaceable, so valve seats and seals would be available as well as components for the pilot valves. In this case you would expect the valve body to remain serviceable, unless it has received physical damage, and then a replacement is usually the only option.
Upgrades are a crucial aspect of the decision to repair or replace; it may be that a different type of valve can replace a series of older valves; Burkert’s Robolux series is an example. This multi-way valve can potentially do away with more than one valve and several pipe sections and bends. Modern design techniques allow this valve to be customised to incorporate mixer and diverter valves, or to integrate sensors into the valve block. Crucially, the number of potential leak paths is greatly reduced and with the valve delivered pre-assembled, installation time is reduced.
Control is also a key decision, as the development of automation marches on, the repair or replacement of a valve might present an opportunity to increase the control and visibility of an application. There are products, such as Burkert's control head, which can be applied to create an intelligent field device from an existing valve, providing information on status and allowing external actuation in an application that previously relied on pressure or manual actuation.
When assessing control valves, there can be strong benefits in upgrading equipment due to the new technology which is evolving in this area. Older systems can be upgraded to provide faster response times with the use of 4-20mA converters and to provide diagnostic information on valve performance – useful when trying to pinpoint areas for concern and resolving performance issues.
The after-sales department at Burkert inspects any returned valves to help in understanding failure modes and so improve installation and reliability. However, many of these valves perform as required when tested; further investigation with the customer can help in determining any reduction in plant performance.
In many cases it transpires that the valve was incorrectly specified by the process design engineer - an issue which can be easily resolved by asking for help from the valve manufacturer. A typical example is using the Kv value for a valve as the flow rating – a common mistake which does not take into account the differing pressures through the valve or the viscosity of the material under control. By making use of expert advice, production control systems can be designed to use the most efficient and appropriate equipment to ensure reliable performance.
There are cases where we have received a 25 year old valve returned for its first service, but the parts may no longer be available. In such cases, we would look at the application and the process as a whole and make suggestions as to the most efficient way forward. This could include integrating new technologies and reducing the total number of valves in the process.
The bottom line is that prevention is better than cure. Good maintenance practice and ensuring that the control devices are providing reliable efficient service is crucial. Replacement of valves may entail higher initial costs, however, additional benefits such as increased diagnostic and communication ability as well as product warranty, all lead to improved productivity in the long term. Where possible, consult with engineers whose experience can be used to benefit the design and operation of the control system.
- Sense and sensitivity
- Transmitter role
- Bürkert boosts support for Ireland with new account manager
- Monitoring enhances accuracy and predictive maintenance
- Solenoid valves: An enduring design
- Flow measurement for WFI loops: Preventing biofilm development
- Technical training
- Simplifying industrial process automation with IO-Link
- Countering contaminants
- Stainless steel PTFE bellows valve