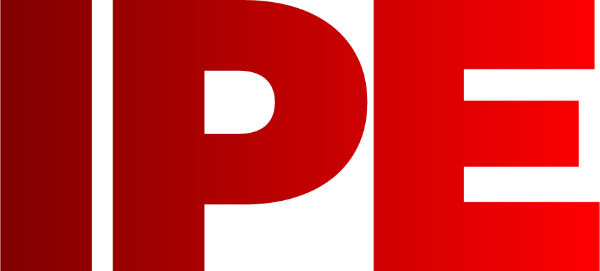
![]() |
Edward Lowton
Editor |
![]() ![]() |
Home> | Plant, Process & Control | >Pumps | >industrial vacuum pumps: Which type is right for my application? |
industrial vacuum pumps: Which type is right for my application?
18 July 2017
To assist end users in selecting the best type of equipment for their application, Richard Oxley, vacuum product manager for Atlas Copco UK, offers a brief overview of the operating principles and current developments in the four main categories of industrial vacuum pump
In the past industrial vacuum pumps were synonymous with high oil carryover, excessive noise and prohibitive energy costs. In parallel with developments in other air movement technologies, vacuum pumps have recently undergone substantial advances in terms of reliability, performance, quiet operation and energy economy.
Rotary vane
Operating on the simple principle of centrifugal force acting on an eccentrically mounted rotor with radially movable blades, this tried and tested technology has been subject to a host of design innovations to improve performance and reduce total operational costs. Compared with earlier generations, power demand at the same volume flow is now about 15% lower. In general, the latest units are more compact, with vibration levels that are 3 to 5dB(A) quieter than their predecessors. They can also now operate at lower temperatures, which protects oil consistency and extends service life as well as maintenance intervals. Capable of an ultimate pressure between 0.1 and 0.5mbar, these pumps are suitable for packaging, woodworking, plastics, paper and printing, material handling and other demanding applications.
Liquid ring vacuum
Liquid ring vacuum is regarded as the optimum technology for handling extreme vapour loads and pumping wet or dry gases with a high tolerance for liquid carryover, especially on condensable processes such as distillation, drying and evaporator duties. Single stage pumps have very good efficiency above 200mbar and are ideal for general process applications such as filtration and dewatering, pump down or evacuation duties.
Liquid ring pumps have a fixed blade impeller located eccentrically within a cylindrical casing. As the impeller rotates, liquid (usually water) is thrown out by centrifugal force to form a liquid ring around the circumference of the casing, sealing the tips of the impeller and creating separate enclosed gas chambers between each blade. In general, capacities range from 170 to 37,500m³/h.
Dry claw vacuum pumps
These offer the advantage that there is no lubrication in the main pumping chamber, thus eliminating the possibility of any contamination of the application process.
Claw vacuum pumps employ two claw-shaped rotors running in opposite directions that don’t touch each other or the pump chamber. This makes them virtually free from wear. They are among the quietest vacuum technologies; which contributes to an agreeable working atmosphere in a wide variety of dry pumping applications ranging from packaging lines, pneumatic conveyors, and clamping systems for CNC machines, to moulding machines, drying processes and central vacuum supply systems.
Volume flows for these pumps varies between 65 and 1230m3/h and units typically have an ultimate vacuum of 140mbar(a). Some of the latest pumps on the market can reach 50mbar(a)
Rotary Screw
Rotary screw pumps are based on proven compressor screw technology and provide significantly higher performance levels and reduced maintenance, noise and heat emissions compared to conventional oil-sealed and dry vane vacuum pumps. With the application of variable speed drive it’s possible to tailor vacuum production to precisely meet process demand. When installed as part of a central vacuum system, energy consumption can be reduced by up to 50%. With a maximum flow rate in the region of 5004m3/h, they are particularly suited for large industrial vacuum users in the glass, plastics, canning and food packaging industries.
- Oil-free rotary screw blower
- Energy recovery and a free CD
- Compressors and heat recovery system
- Oil-injected screw compressors
- Acquisition announced
- Centrifugal turbo compressors
- Atlas Copco Ireland appoints business line manager for its compressor technique service Division
- Tips on specifying a stationary air compressor
- Quiet compressors – the key to reducing factory noise emissions
- Latest vacuum pumps: Potential for energy savings