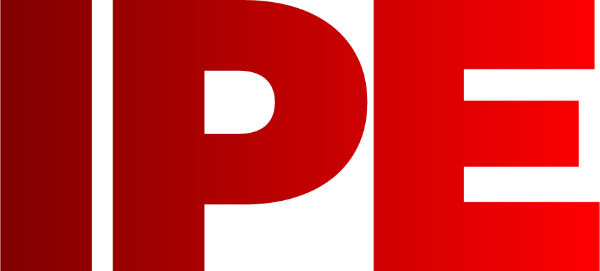
![]() |
Edward Lowton
Editor |
![]() ![]() |
Water technology that's making waves
05 December 2017
Not only is water a scarce resource, maintaining water quality standards is an essential process for water supply companies and those who rely on it for commercial process applications. Charlotte Stonestreet takes a look at some of the latest developments
Anyone watching the BBC’s current flagship natural history series, Blue Planet II, will be aware of the vast quantities of water that cover around 70% of the Earth’s surface. Of this, however, around 97.5% is salt water leaving just 2.5% as fresh water; of this more than two-thirds is frozen, with another large proportion stored below ground as ground water. What all this means is that only 0.3% of all freshwater on the plant is really available as surface water. Add to this that this relatively tiny proportion of what at first might seem like an abundant resource is often the ‘wrong’ place in terms of demand/consumption, resulting in round 40% of the world’s population living in water stressed areas - a figure which, according to the United Nations Environment Programme, is projected to increase to between 50 and 65% by 2025 - and it is clear that water is not something thatch be taken for granted.
Like any scarce resource, for businesses water presents not just a challenge, but also an opportunity. While an inadequate water strategy can lead to businesses pouring profit down the drain, get it right and there are bottomline improvements to be made, and this is a message that Velioa is emphasising in its recent “Rethink Water’ white paper.
When it comes to water, there is a perception that sewer discharge costs nothing and there is little you can do with wastewater once it has been treated and cleaned in line with industry regulations. Unfortunately, nothing could be further from the truth, and businesses need to change how they see water, asserts Veolia. Delivery of mains water costs £1 per cubic metre, and it typically costs twice as much to discharge the equivalent volume, meaning that reusing and recycling wastewater can save up to £3 per cubic metre, not to mention the potential for converting waste to energy to be used elsewhere in a facility. Companies looking to increase profit while generating positive publicity can start by analysing the total cost and environmental impact of their water usage, and implement solutions to reduce consumption.
There are currently no restrictions for most customers on the amount of water that can be drawn from the network or returned to the drain; you simply pay for the amount you use or discharge. However, we are now beginning to see the emergence of limits for industrial water use to try and manage demand. Although there are currently only financial penalties for excess use, if demand continues to exceed supply, we may see a situation in the future where water supplies are simply cut off once water limits are reached. This would have a far more significant impact, leading to temporary shutdown of manufacturing processes and significantly harming profitability.
Reuse & recycle
If you’re in an industry that cannot operate without water, Veolia advises that now is the time to consider how you can improve water reuse and recycling to reduce consumption and disposal costs before they start to impact your bottom line.
Reducing water consumption is the most direct way to save money, and an internal audit of processes can often reveal examples of inefficient or wasteful water use, such as leaving taps or hoses running unnecessarily during washing processes. Regular water monitoring can help highlight leaks or unexplained water usage in your facility. If trade activities primarily occur during the day time for example, you should expect to see your water consumption almost zero overnight.
Reusing and recycling wastewater can offer even more significant savings, due to the high cost of discharging wastewater. There is reticence within some industries to reusing and recycling water, due to the fear factor around using treated wastewater, for example, to clean a tank involved in food production. But greater understanding of how efficient and effective wastewater treatment can be should alleviate any industry concerns and overcome such objections. After all, it is too easy to forget that every drop of mains water has at some stage been reused and recycled.
Wastewater can be a very valuable resource, particularly in the food and beverage industry. For example, wastewater from dairies and distilleries could be passed through an anaerobic bioreactor to produce biogas, which could be returned to the grid or back to the facility to supply energy – up to 80% of the electrical needs of some distilleries. A second by-product, biomass, could also be repurposed as fuel, or used as land fertiliser on farms.
Water analysis
Maintaining water quality standards is an essential process, not only for water supply companies, but also for those who rely on it for their commercial process applications. Analysing and recording various water quality parameters using the compact and modular solution from Bürkert Fluid Control Systems now has increased functionality thanks to new 'cubes' that add more test options.
Since introducing the Type 8905 Online Analysis System for water treatment processes, Burkert has continued to work on new functions and testing capabilities that increase its functionality. The latest developments include new test cubes for Chlorine dioxide and iron as well as a hand-held cleaning and calibration module.
Furthermore, the ability to adapt the basic principle of the analysis system into a bespoke sampling station that can accommodate any number of sample streams will be of particular interest to larger water treatment facilities.
The original premise was to create a multi-channel, multi-function unit that could communicate using the majority of existing protocols and provide a precise record of water quality, based on the needs of the application. As such, the Type 8905 is already capable of measuring pH, reduction potential (ORP), conductivity, free chlorine and turbidity.
Chlorine dioxide is an important characteristic to measure in the disinfection process as it is widely used as an effective microbicide, disinfectant and sanitiser. The effective control of this popular chemical is very important and Bürkert has now added a sensor cube that can be used in both new and existing analysis stations.
Just as important is the removal of iron deposits from water used for processes that demand a minimum of contaminants. The iron analysis cube can be set up to measure and record iron levels as well as initiate warnings when pre-set levels are reached.
The Type 8905 can communicate with existing control protocols and with personnel both on and off site, ensuring that any deviation from the water quality criteria is notified immediately.
Blockage detection
Blockages of submersible pumps caused by grease and solids are a major problem in pumping wastewater. In the worst-case scenario, this can result in flooded wells, unwanted spillages and eventually, premature motor failures. Unscheduled work to manually clear the blockages is then required, which entails pump lifting, involving considerable time and expense, not to mention the health and safety aspects.
Anglian Water has extensively trialled the Simocode motor management system from Siemens, at over 200 of its sites. Early results have shown an impressive 70% reduction in blockages, and in many instances engineers no longer have to visit troublesome sites.
Initially, Anglian Water ran a trial at a site in Corby, which had been experiencing regular pump blockage issues. Upon first use with Simocode the operator was able to identify that the pump was running at a higher than anticipated current, and instigated a reversal operation. The current then reduced significantly, suggesting evidence of freeing a previous blockage. The system was configured to look for set points indicating higher than normal currents, whereby Simocode would automatically instigate a pump reversal.
Simocode is simple to deploy, which means no new software tools have to be learned and no extra time is wasted in learning new software skills. In addition to managing the process, if required Simocode will provide all the data associated with the pump over a secure internet connection so decisions can be taken remotely.
Mobile filtration
The UK has been slow to pick up on the advantages of mobile containerised water filtration plants but it is now becoming a rapidly increasing trend. As industry wakes up to the fact that water is a limited resource, more and more options regarding source are being considered. Not only does this mean a variation in the water quality but access to the source can test even the most experienced engineer and it may only be a temporary operation. According to Amiad, flexibility, manoeuvrability and non-permanent nature of a containerised water filtration plant is very appealing.
Units can vary from complete small scale treatment plants to multiple container systems each incorporating a stage in the treatment process. However, it is not just the provision of mobility that has made these popular with some of the most far reaching utility and industrial plants. The ability to pre-commission and ‘prove’ the system before dispatching effectively reduces installation and maintenance issues as they will only require services connection and process interconnection on arrival at site.
Good containerisation requires careful thought. Often space is at a premium and access is limited. Early discussion with the client regarding maintenance requirements and access ability, typical deployments periods, along with their own policies on these matters requires careful consideration. How much heat will be generated by system pumps and the extremes of ambient temperature also have to be examined.
Amiad produces containerised systems with specialised sections in the roof to enable media to be changed and access ports in walls for critical part removal. Units can be purchased outright or procured as a contracted package so costs can be spread out over a period of time.
Zero liquid discharge
Zero liquid discharge (ZLD) is a liquid waste stream treatment. It involves transforming liquid waste streams from industrial plants into clean water, which can be reused in the process, and the minimum amount of solid residues, which often include valuable by-products that can be sold or reused.
ZLD is suitable for a wide range of industries, including power production, chemical and fuel refining, mining, distillation, food production, and waste treatment, and a variety of equipment is available to treat different waste streams and processes. However, this diversity means every system must be designed on its own merits, considering factors such as the contamination or chemicals present in the water, flow rate, how pure the returned water needs to be, etc. This makes it impossible to design a ‘general purpose’ ZLD system, and makes the necessary custom-made solutions more expensive.
The effective design of any ZLD system is dependent on the correct analysis of the water/waste stream. It is essential to have accurate estimates of composition, flow rates, chemistry, etc. Without this, any designed solution will fail to deliver the required results, if it works at all. For example, calcium, ammonium and some heavy metal salts are difficult to crystallise by evaporation, and so other treatment techniques will need to be incorporated into the overall system design.
According to HRS Heat Exchangers , although every ZLD system will be different, many will comprise a pre-treatment phase, an evaporation phase to remove most of the water, and a further concentration or crystallisation phase to produce the final solid residue. Pre-treatment often focuses on removing organic elements and any chemicals which could damage evaporation or other equipment later in the process. As ZLD has become more widely used, more and more techniques have been employed, with varying levels of success. Most common water treatments, such as pH adjustment, flocculation, membrane processing, degasification, oxidation, separation and even aerobic and anaerobic digestion, have all been used as pre-treatments for ZLD systems.
Traditionally, vapour compression evaporation has been the main method employed for ZLD processing, with evaporation typically recovering around 95 per cent of wastewater as distillate. Any remaining concentrate is then further treated physically or chemically to produce solid residues (such as crystals) and water. Evaporators used in ZLD systems are often run at lower pressures in order to reduce the boiling point of the liquid being treated.
Working with a reduced boiling point means that multi effect evaporation can be made possible. In multi-effect evaporation, steam from a previous evaporation stage is used as thermal energy in the next stage which works at a lower boiling point. This way, multiple evaporation stages are combined and as a result energy savings are obtained. For many components, crystal precipitation is favoured at lower temperatures, therefore lowering evaporation temperatures helps to increase the solids yield.
Whatever kind of evaporator is employed, heat exchangers play a crucial role in reducing the running costs of a ZLD system by utilising heat from process water and other existing sources, and also recapturing heat at the end of the process and reusing it to boost the energy efficiency of the overall ZLD system.
- CVE obtains funding for zero-carbon projects
- E3 Academy scheme aims to double pipeline of electrical engineering talent
- Thriving in a competitive market
- End of the line for manual packaging?
- Warehouse automation gets smart
- UK Manufacturing most cyber-attacked industry
- Reliability, safety & cost reduction
- On track for digitisation
- No related articles listed