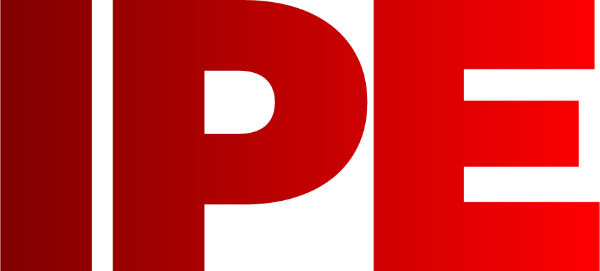
![]() |
Edward Lowton
Editor |
![]() ![]() |
Home> | Health, Safety & Welfare | >PPE | >3D-printed PPE |
3D-printed PPE
01 July 2020
The success of the UK's National 3D Printing Society’s initiative allows RS to refocus its efforts on the international need for 3D-printed face visors during COVID-19 pandemic
RS Components is broadening its focus to help frontline healthcare workers around the world access 3D-printed personal protection equipment (PPE). The company’s DesignSpark engineering community has been very active in supporting the National 3D Printing Society’s (N3DPS) UK campaign, which has now officially drawn to a close.
3D printing has played a key role in the UK, helping to keep medical staff and key workers safe since the start of the COVID-19 crisis. Enlisting 3D printers to manufacture PPE provided the vital fillip needed until more conventional manufacturers were able to ramp up production.
Mike Bray, Group Vice President of Innovation and DesignSpark at RS, said: “We are proud to be continuing to assist in the 3D printing effort. The UK was hit hard by the first wave of COVID-19, with global supply chains for PPE stretched to breaking point. Every volunteer who has given their time and effort across all of these initiatives should be very proud to have played their part."
In April, RS set up a 3D printing farm in Corby, Northamptonshire, to support the collective effort and has since printed hundreds of visor frames. Fellow Northamptonshire company igus was responsible for assembling the face visors, with staff volunteering their time to add the plastic sheets to the community printed frames for distribution. Part of the company’s Northampton facility was quickly repurposed as an emergency production line, which at the peak was turning out 1000 pieces of PPE per day.
Matthew Aldridge, Managing Director of igus UK commented: “When we became aware of this project, we volunteered to help with the assembly of the face visors. Within hours the production line was set up, within days PPE was being delivered to frontline workers, all using igus people, usually working in their own time to make it happen."
Thousands of other volunteers, schools and businesses across the UK have also supported not only this initiative but many others, including 3D Crowd UK and Makers 4 the NHS. Collectively these groups have helped to ensure that over 250,000 visors have been produced in just two months.
This period of support through 3D printing relieved the sudden pressure on injection moulding companies around the UK, including igus, allowing them time to build production to thousands of visors each day, using a much more efficient and sustainable method of manufacturing. Injection moulding not only produces the visors in larger quantities, but also increases the product consistency and quality.
Stock levels of traditional PPE are also returning around the UK. RS now has over 140,000 PPE Class I certified face shields in stock and available for free next working day delivery, along with a host of other equipment including disposable face masks.
As a result, there has been a significant reduction in the demand for auxiliary PPE prints. This, coupled with a recent UK Government guidance document which required some significant changes to be made to current processes being used by voluntary organisations, has led to many initiatives pausing or ending production completely.
With thousands of assembled visors remaining within the National 3D Printing Society’s network which have not cleared the new guidelines set by government, these will instead be diverted to countries outside of the EU that are able to use them, working with the Red Cross. RS and igus are also working to explore support for other initiatives in Africa and Moldova respectively.
Any remaining funds from the £14,472 crowdfunded for the N3DPS campaign, are being donated to MedSupplyDrive UK, an organisation run by volunteer NHS doctors and medical students to purchase PPE for frontline workers. MedSupplyDrive UK has been a key partner in the initiative, alongside igus, RS Components, ByBox, the Gap Partnership, SHIELD and the Nottinghamshire Community Foundation.
Bray said: “Whilst not all of the visors will be heading to the UK frontline workers as originally intended, they will still be helping to save lives across the world and that is no small achievement.
“The increased number of injection moulding companies now producing large quantities is helping to ensure that the demand within the UK will be supported. We are continuing to work with the Office for Product Safety and Standards to clarify guidance, specifically around the inclusion of heat testing in the CE Marking process and the liability for volunteer groups. This will enable 3D printing solutions to step up again in the UK as and when needed.
“As our focus moves towards supporting health-care workers from across the globe, we would like to thank everybody who has been involved in the initiative to-date, including members of our own DesignSpark engineering platform. The community spirit and resolve to help has been a huge positive during this time, and we continue to urge people to produce emergency equipment for frontline healthcare workers wherever it’s needed. We are one community, supporting each other in facing the same challenges from COVID-19.”
Aldridge added: “The mantra at igus is ‘everyone is a manager’. Our people have total autonomy coupled with total responsibility, this gives a very flat company structure, and it means that work gets done, very quickly. We are proud to have been part of this community effort and believe that it is very important that we are able to help people around the globe who are fighting COVID-19 using the remaining visors.”
- PPE selection guide
- Scalable, entry-level access control bundles
- 3D printing technology
- HVAC smart probes sync wirelessly with smartphones
- Digitisation of the end-to-end maintenance supply chain
- Effective energy management holds infinite benefits for industrial operators
- Visitor experience celebrates digital world
- Tackling mounting challenges to keep water and wastewater flowing
- Affordable 3D solution for design bottlenecks
- Lockout equipment