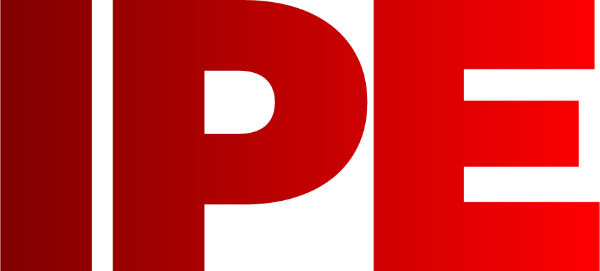
![]() |
Edward Lowton
Editor |
![]() ![]() |
Home> | Plant, Process & Control | >Sensors and instrumentation | >Reaping the benefits of the evolution of sensor technology |
Reaping the benefits of the evolution of sensor technology
04 July 2024
Keeping abreast of the evolving sensor technology landscape will help industrial operators get a better picture of asset health, says Milesh Patel

OPERATORS IN the industrial sphere, wherever they are in their preventative or predictive maintenance journey, rely on sensors within the plant to achieve and maintain access to a real-time picture of asset health.
Sensors are top of the list of required components. As cost has come down, technology has evolved and retrofitting becomes less complex, there’s really no excuse not to maximise their potential to identify issues and enhance plant efficiency. So are operators keeping updated on the latest sensor technologies that can help them reap rewards?
Harnessing the power of IO-Link technology
IO-Link gives access to status information that would have been previously inaccessible. It enhances sensor capabilities by providing additional data, like parameters and device status. With the capability to self-diagnose and send information to the control system, IO Link technology can help engineers to obtain data that can take their maintenance strategy from preventative to predictive.
IO-Link technology is arguably far from new - in fact, it’s been around for some 15 years - but it’s still not truly optimised and there are perceived barriers to adoption for some. This is severely hindering true maturity of this benefit-packed technology.
A potential barrier may be the perception of a complex installation; however, this technology utilises existing wiring. The transmission of information is conducted via the sensor or actuator’s three-wire connection. The result is an invisible solution, which does not affect any other components, operation or diagnostics, with the information transmitted over the same line as the process data. In short, implementing IO-Link couldn’t be easier.
Another barrier could be the limited choice of IO-Link enabled sensors, but the range of available products is vast and increasing all the time - and reducing in cost - negating yet another barrier to adoption.
The evolution of factory automation sensing
Like any technology, sensing will evolve and become even more valuable on the factory floor. We’re already seeing sensors reduce in cost and increase in functionality, which is a trend we will likely see continue, due to an uplift in sensors used across all applications. It’s probable that multi-function sensors will become standard as the cost of combining features, like pressure and temperature in a single device, continues to reduce. We should also see a reduction in sensor size: with MEMS technology (Micro Electromechanical System) driving change in consumer, medical, automotive and industrial sensing applications.
There’s no escaping digital transformation and so IIOT capability in-device will increase. With connected devices, particularly in the consumer market becoming commonplace, the idea that Ethernet or WIFI capability will be embedded within the sensor isn’t far off. There are already robust industrial application-suitable protocols available and the cost saving on installation and cabling costs is significant, especially on larger installations. Perhaps we’ll also see IO-Link V2.0. As IO-Link approaches a critical mass of manufacturer adoption, the functionality and capability of IO-Link will need to evolve as sensor manufacturers, OEMs and end users demand greater levels of information and control from their sensors and actuators.
Milesh Patel is a supplier manager, automation and control, for RS UK and Ireland
For more information:
Tel: 03457 201201
- RS Components launches 7-in-1 oscilloscope
- RS releases 2025 Indirect Procurement Report: Tackling the cost of business
- Preparing for change: The evolution of MRO procurement
- Tackling mounting challenges to keep water and wastewater flowing
- Online event calling for greater diversity in UK engineering roles
- Tools and accessories: Special promotion
- RS appoints new Regional Managing Director for UK and Ireland
- Unlocking dormant data improve maintenance decision-making
- RS Components supports innovation with sponsorship for Mantis walking machine
- Driving F&B exports with a proactive maintenance approach