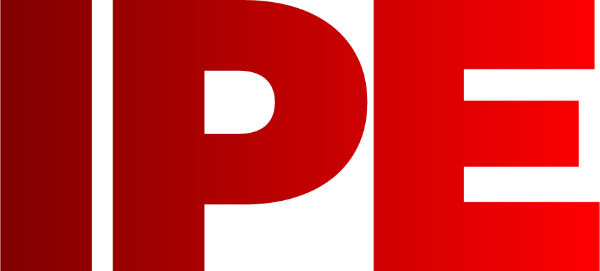
![]() |
Edward Lowton
Editor |
![]() ![]() |
Home> | Industry update | >Company news | >Building a robust compliance process |
Building a robust compliance process
17 April 2023
With an annual output of over £400 billion, the UK manufacturing sector is a major player in the global market. Yet it faces unique challenges when it comes to supply chain compliance, explain Dale Jones and Lisa Stevens

THE UK'S manufacturing sector is quite different in terms of its make-up when compared to other industries. Over 45% of organisations in the sector are classified as large, in terms of turnover and number of employees. In general terms, this means they tend to operate from multiple locations with higher head counts. In comparison, less than 1% of construction businesses would fit into this classification.
Manufacturing has many different sub-sectors, which includes food and drink, engineering, paper, plastics, textiles, and chemicals, just to name a few. Each of these has varying risk profiles. But what does that mean in terms of the supply chain?
Essentially, you’re going to have a number of direct suppliers providing services, goods, and products, which are necessary for you to manufacture the products you deliver. Additionally, there are also indirect suppliers who provide services and goods to keep your plant operational.
To reduce risk in your supply chain, it’s essential to gather compliance information from all your suppliers. However, the level and depth of information required will vary depending on the service or product being delivered. Given this, dealing with all suppliers in the same way using generic processes and questions is not always going to be suitable.
Working with contractors
As an industry, manufacturing tends to be particularly dependent on one type of supplier: contractors. These businesses provide specialist skills on projects, often during busy periods, whether that's maintenance turnarounds or shutdowns. The types of contractors can vary and may include a range of services, such as maintenance construction, installs, PPM, or inspection and testing.
Organisations generally utilise contractors to either provide a skill set that's not continuously required or to supplement limited internal resources, e.g. allowing for increases in headcount without the overhead cost of directly employed employees. However, the introduction of contractors into any workplace will bring an increase in risk to the operating environment.
This risk arises from the fact that you will have individuals or teams of people who will be unfamiliar with existing risks in facilities, along with different types of risk that their projects will bring and how they could impact on regular workflows.
Therefore, understanding contractors' safety capabilities is a key step in reducing risks, whether that be from working at height, isolating energy sources, working in confined spaces, and movement and storage of hazardous materials such as asbestos.
Developing a resilient supply chain
Safety is not the only factor, however, that organisations need to be concerned about. The global disruptions that businesses have experienced in recent years have seen manufacturers move to increase their UK supply base by up to 42%.
These increases have been made to help ensure resilience of supply, whether that is the need to lower costs or to minimise the impact of suppliers going into administration due to issues such as inflation and rising costs.
And all of this is being done within an ever-changing regulatory environment. Over the last couple of years, as organisations have needed to address post-Brexit requirements for bringing goods and materials into and out of the UK, there is an ever-growing need for information on various compliance-related topics.
A few of the common topics we’re seeing at the moment include understanding how suppliers are managing obligations for environmental and carbon management, and the journey towards Net Zero; bribery and anti-corruption; forced labour; and cybersecurity, among others.
An evolving regulatory environment
The specific requirements for each are evolving - especially for organisations operating in Europe - and there are a range of things to be aware of and monitor in terms of changes. One of these is the German Supply Chain Due Diligence act. This is a piece of legislation which mandates that companies with either locations or parent companies in Germany must conduct due diligence checks on their supply chains, both to protect human rights and meet environmental requirements.
Alongside this, the EU is looking to introduce new industry powers to protect European supply chains during times of crisis. Any new rules will be implemented via legislation, but this could potentially force member states to stockpile key products.
There are also proposed legislative changes to public procurement requirements in the UK, with the Government reportedly keen to overhaul the current regulatory framework.
Identifying supply chain priorities
Alcumus commissioned a study by 20/20 Research in April 2022 which surveyed 874 respondents from Australia, Canada, the UK, and the US and covered multiple sectors and business sizes.
The study identified strategic sourcing as a very high priority for 63% of companies. To put that in context, almost two-thirds of organisations are discussing supply risks at board level and are actively seeking to improve their supply chain management.
One survey respondent highlighted the sheer number of suppliers their organisation has to manage is “very time and labour-intensive”, adding “we need a larger team to address the problems we have, but we lack budgets”.
Another respondent noted supply chain services can be difficult to manage due to limited reporting ability, while they also questioned the accuracy of those reports they do have. That is a point which seems to resonate across a lot of the manufacturing industry.
Resolving underlying issues
Alcumus has found that organisations taking a stance on safety and sustainability are reaping commercial benefits. These include increased business growth, workforce satisfaction, and greater investor interest.
However, there are several underlying issues which need to be solved. One of these being the need to move from passive to active safety and sustainability management. Passively treating contractor and supplier management as a checkbox exercise cannot continue.
Utilising standardised questions for contractors and suppliers which may not adequately cover the work they undertake leads to reduced insight regarding their capabilities, their safety credentials and ESG requirements when working on behalf of a client. In turn, limited visibility in terms of compliance, contributes to increased risk exposure.
One of the key takeaways from our survey was that many organisations are facing a lack of trusted data. As the role of safety and ESG continues to grow in importance, so too does the need for trusted accurate data across supply chains.
Manual and ineffectual existing processes and procedures overextend personnel and create cumbersome admin that frustrates both internal and external stakeholders. The continued use of processes that rely heavily on internal resources can also cause delays, while a "just-in-time" environment, can result in mistakes and rework.
Another common issue is data and system silos. We often find businesses where pockets of key data are siloed. This data is not connected and cannot be reported on, meaning that organisations do not have that ‘one true view’ across their operations. These firms are working on dated methods like spreadsheets, which give rise to data inaccessibility, together with complexity challenges.
Charting supply chain challenges
Coming back to the survey, we asked operators in the manufacturing sector about the most challenges facing companies, their chief procurement officers and health and safety personnel. Alongside this, we also discussed their ability to address gaps in the supply chain.
51% of respondents identified a lack of supplier transparency as an issue, noting that suppliers are not always able or willing to share the necessary information. 35% of participants said they were unable to report on supplier compliance and 33% said they didn't have enough resources to manage compliance.
Our research also found that 80% of supply chain leaders recognised they need to make improvements within their prequalification processes within the next two years. Organisations typically have multiple personnel assigned to the prequalification practices. Mid-sized businesses - those with 250-1000 employees - had on average three people involved in supply prequalification, while this figure rose to five people for larger firms.
We found that on average, our clients spend five hours per month on maintaining their databases, five hours on sending out PQQs to new suppliers, five hours chasing those PQQs, and 10 hours managing documents (including re-audits). This equates to 40 working days prequalifying contractors and suppliers.
Building a robust compliance process
Those are some of the challenges being encountered by manufacturers. Given these, what are some of the necessary steps in order to operate a robust supply chain compliance process?
To start off, you need to go back to basics. It’s important to consider what you need to achieve with the processes and how to manage stakeholders’ expectations. You need to engage with groups such as the board of directors, investors, employees, consumers, trade bodies, and NGOs that work in the sector. They are all going to have expectations regarding what standards need to be applied within your organisation.
It’s also important to consider the legislative requirements and standards that each business needs to conform to. Here you need to think about topics such as health and safety, environmental management, quality management, modern slavery, bribery and corruption, equality and diversity, financial performance, cybersecurity, data protection, corporate governance, and insurance.
Learning from best practice
In terms of best practice, undertake a review of your existing approved supplier list. It’s common to see manufacturers with lists containing thousands of entries that have either been added over the years or, if an organisation has grown via acquisition, they may have various lists in different systems over multiple locations.
While all organisations know who their key suppliers are, many become less certain once they move beyond tier-one suppliers. We have commonly seen that the lists tend to be dated and may contain references to companies which are no longer operating, have never been used or not used for a number of years.
Such lists will often lack visibility regarding how often contractors and/or suppliers are being used and can contain out-of-date contact information. As a first step in addressing this issue, organisations need to review their supplier lists and remove those companies which are no longer used.
It’s also important to identify key services, goods or products. Based on this, an organisation can clarify whether they need to consider diversifying the businesses they are working with to ensure consistency and resilience of service. Always have a plan B and an awareness of who else could potentially provide a service or product.
Supplier requalification
We recommend placing suppliers through an initial prequalification process and then re-qualifying them on an annual basis as a minimum. This will provide a snapshot of how they're performing; what their capabilities are for managing risk; and most importantly, will provide an insight into how they are improving or aligning their capabilities and objectives with your own.
Organisations need to plan how they are going to engage with suppliers and prepare them for completing a qualification process. It’s not always going to be as easy as sending the suppliers an email and receiving an instantaneous response. But, the key is to develop a workflow that drives engagement with suppliers and ownership from the team that deals with and manages supply in the organisation.
Another important consideration are the systems that an organisation uses to send and capture information. How can you guarantee that everyone who needs access to the information can actually see the required information?
There are also a number of additional questions to consider: Once the contract element of supply chain has gone through the prequalification stage, how do you authorise both the business and its employees to come on site? How do you streamline the induction process in order to avoid unnecessary delays and at the same time ensure that everyone attending the location understands the key rules and procedures on-site?
Overall, the key to practical compliance management across the supply chain is to take a technology-led approach. The use of technology will not only save time and effort, but it will also simplify how organisations drive, track and review overall performance as well as manage risk.
If you'd like to hear Lisa and Dale discussing the issues surrounding supply chain compliance in more detail, together with what Alcumus can do to help, why not check out their webinar: How to Enhance Supply Chain Compliance in the Manufacturing Sector, available here: https://tinyurl.com/bdctbads
For more information:
https://www.alcumus.com
Tel: 0330 127 1723
- Will China’s zero COVID-19 policy mean renewed export disruptions?
- ISO standards: Free-to-attend workshops
- Achieving robust, reliable and transparent supply chains
- Getting ahead of supply chain risks in manufacturing
- Managing COSHH in the supply chain
- Are your key suppliers on the edge of being shut down?
- How to lock out poor quality, unethical components
- Compliance and risk management expert expands leadership team
- Risk management expertise
- In charge of digital risk management service