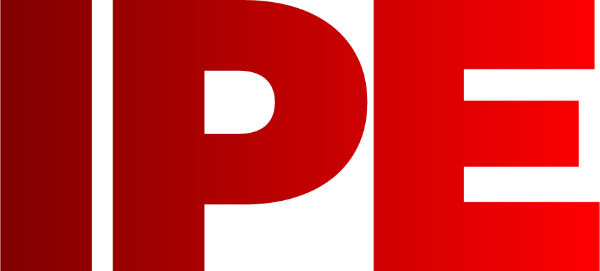
![]() |
Edward Lowton
Editor |
![]() ![]() |
Data drives down equipment failure
28 July 2021
IN THE age of intense global competition the pressure on manufacturers to achieve greater levels of efficiency and quality output is relentless. But when machines and equipment underperform or fail, this can result in service delays, unhappy customers, and productivity and income losses, asserts Iwona Kandpal, industrial digital technology specialist at Made Smarter.
Never before has the need to know exactly how every machine across the factory floor is performing to tackle the challenge of unplanned downtime.
Digitalisation and the advances in industrial technology mean access to that valuable data - which is at the core of effective monitoring, control and analytics - is now at the fingertips of the workforce.
Industry 4.0 technologies, such as Industrial IoT (Internet of Things) sensors, which collect the data automatically, are laying the foundation for the introduction of analytics and Artificial Intelligence (AI), which can warn of potential failures long before they may happen.
While an increasing number of manufacturers are pursuing this path, the reality for many small and medium-sized enterprises is that they are not yet ready to capture this valuable information from their equipment, and risk wasting time and money investing in the wrong technology, in the wrong way, trying to catch up with the pack.
Reliant on reactive
For the last two and a half years the Made Smarter’s Adoption programme in the North West has engaged with hundreds of SME manufacturers, assessing their digital capabilities and readiness. We have found that many are still reliant on reactive and preventative maintenance, and manually monitor equipment.
The justification is that not spending time, money and labour on a machine that isn’t broken can be advantageous in the short term. But a fail and fix strategy is not sustainable in the long term. It puts a business at risk of the worst case scenario, where a machine stops working and there is a delay on getting parts for the repair, halting production, increasing lead times and reducing profits.
A planned maintenance strategy, with schedules for part changes, introduces an element of proactivity and is cheaper than the long term costs associated with reactive maintenance, but it relies on human intervention from the shop floor, is manually recorded and managed, and doesn’t overcome the risk of a serious failure developing before the next inspection.
The solution to these traditional approaches is predictive maintenance, where digital removes the human element in the collection, storage and analysis of data. But the journey to predictive maintenance usually starts at having a maintenance schedule, basic data collection, and analytics already in place. Once a company can identify that this solution is not sufficient anymore then it is time to reach out for specialist advice to scope the predictive element of their maintenance practice and avoid ballooning project costs.
In all our conversations with manufacturers, we advocate a holistic approach to digital transformation where every decision is qualified and quantified. This can be broken down into four key steps.
The first, and most important step, is to get impartial expert advice.
Since 2019, Made Smarter has worked with more than 1200 businesses supporting them to introduce digital tools and technologies to help boost productivity and growth, and navigate the impact of Covid-19.
Identifying the challenges
We aim to identify technology with a purpose, so at the heart of these conversations is understanding what challenge a business is trying to solve.
For instance, the ambition could be to reduce machine downtime, improve product quality, reduce maintenance costs or lead times. Maybe the driver is to gain insight into legacy equipment or understand what is behind micro-stoppages, which are often missed by human monitoring and go unrecorded, but can add up to be a significant issue.
Understanding the purpose of why the data is being collected means technology can be adopted sustainably. It will also help you choose the scale of the project. Is it to monitor one machine, a whole line or the entire factory?
Step two is deciding which technology you will use to collect the data.
IIoT sensors, which record things like temperature, vibration, the trajectory of moving parts in machinery, flow rate, pressure and fluid levels, is one of a number of methods of collecting that data.
Process control systems can host and analyse data from different sources such as IoT sensors, machines, robots and other manufacturing equipment.
Process control systems have developed over the years and have integrated their reporting solutions with AI technology effectively becoming the driving force towards achieving predictive maintenance. Of course, the data can also be shared with the ERP systems and analysed.
Step three focuses on how and where that data is stored.
When introducing data collection devices or systems we need to be aware of the format in which this data is collected. This is because some machines are not compatible with modern ‘computer language’ and if connected directly, could render the data unreadable. To avoid this, it is best to turn to system integrators who are able to design and deploy fully-integrated industrial IT architecture.
Typically, an average factory will have a mixture of legacy control systems which require integration and modern data collection devices which will be able to communicate with computers directly. In other words, when thinking about a data collection system, turn to professionals for advice as not all the systems are as quick and easy to set up as their leaflet would suggest.
Data storage
In addition to the above, it is important to be aware that there are different methods of industrial data storage which play a crucial role as an enabling solution to successful analytics reports.
Reporting tools, whether AI-driven or not, depend on data storage. How well this data is organised will impact how quickly it can be accessed and ‘clunky’ storage will be a deal-breaker to achieving live or near-to-live reports.
Then comes the fourth and final step, the analytics, and the gateway to using AI and machine learning to spot trends in production and labour, correct maintenance and quality issues, minimise safety, business risk and operational downtime throughout their production.
Data and analytics are central to the 4th Industrial Revolution, which is why so many SME manufacturers are putting data at the heart of their own digitalisation journeys. Capturing the data from across their processes and bringing it all together in one place is a vital first step for many manufacturers looking to solve problems and recognise opportunities. But upgrading to new technologies can seem like a complex and daunting task and SMEs can miss out on significant improvements to their operations.
This is why Made Smarter developed a Digital Transformation Workshop, an innovative, streamlined process which uses a diagnostic of a manufacturer's products, services, processes and people to find practical solutions to overcome business challenges.
The bespoke process cuts through the jargon to demonstrate the steps required in order to achieve digitalisation. It has been designed in a way that requires minimal time investment for manufacturers to turn the actions into results, while still allowing participants to focus on the day-to-day operations of the business.
Decision-makers' guide
The result is an easy-to-use guide for decision-makers with recommended first steps, a technology roadmap with potential suppliers, and information about how to get further support from the Made Smarter Adoption programme.
This includes support with a technology project to pilot ideas, a leadership programme designed to equip SME managers and directors with the strategic view and the skills needed to pursue smarter manufacturing, and funded digital technology internships where undergraduates, masters and PhD students, and graduates work on live projects which may involve implementing technology projects, upskilling staff or helping develop the business's digital roadmap to support its digital transformation.
Made Smarter is also supporting manufacturers with organisation and workforce development (OWD), which focuses on getting a business ready for industrial digital technologies by analysing the business structure, identifying if departments could work better together, and any gaps in knowledge where upskilling could help. It can then support practical planning, developing people, engaging with employees, and producing materials that can be used to develop a highly skilled, flexible and productive workforces needed to capitalise on digital transformation.
Network of sensors
A great example of a Made Smarter-supported business driving forward its digital transformation is Crystal Doors, a manufacturer of bespoke vinyl wrapped furniture components, based in Rochdale.
Its data and systems integration project will establish a network of sensors connecting their machines through the cloud onto a dashboard. Supported by a digital technology intern, Crystal Doors are aiming to gain insights into how its machines are performing and identify potential efficiencies.
We are also working with Spiroflow, a process equipment manufacturer based in Clitheroe which has developed a remote monitoring system using IIoT to capture real-time information on the performance of its complete machinery range.
For its customer it means an operator no longer needs to constantly monitor equipment or processes, and can be alerted of potential safety hazards before they arise. Constant insight into equipment performance and being made aware of maintenance schedules will eliminate costly and unnecessary downtime.
For Spiroflow, remote access to its customers’ equipment means engineers will be able to carry out diagnostics without the need to travel, which will significantly reduce travel time, cost, and emissions, and make its maintenance and repair service more efficient and productive.
Access to the data will also give Spiroflow insight into the predictive maintenance of its equipment., meaning it can stock the right spare parts and become more efficient. The data will also help Spiroflow understand its product range better and provide feedback into its research and design process.
It is not a secret that SME manufacturers have been slow to adopt digital technologies and are lagging behind. Before the pandemic many struggled with the dual barriers of time and money to buy their ticket for the Industry 4.0 express, focussing on short-term goals to maintain economic viability.
But the message is clear that survival, recovery, and future prosperity depend on digitalisation, which can help make things faster and better. To get to that target destination, you need to understand the resources you have now and make a plan on how to get there.
- BEP Surface Technologies slashes energy use by 20% with data-driven project
- Made Smarter-backed engineering firm hails 'phenomenal' impact after smart factory success
- Digital spare parts: innovation to solve supply chain woes
- New fund to develop digital innovation
- How SME manufacturers are upskilling workers to create the teams of tomorrow
- Technology and digital skills support help SME manufacturers achieve efficiency and innovation
- Helping tackle fractured supply chains
- Robotics and automation create manufacturing jobs
- Cardboard cutout manufacturer invests in AI and automation
- Helping SME manufacturers realise the smart factory dream
- No related articles listed