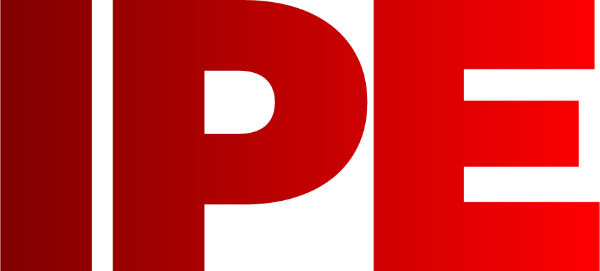
![]() |
Edward Lowton
Editor |
![]() ![]() |
Home> | Plant, Process & Control | >Industry 4.0 | >Helping SME manufacturers realise the smart factory dream |
Helping SME manufacturers realise the smart factory dream
28 July 2023
British SMEs are starting to get to grips with the opportunities afforded by Industry 4.0 technologies, according to Kevin Smith

IT HAS been 12 years since the term ‘Industry 4.0’ was first introduced to the world, laying out the picture of the factory of the future. The so-called smart factory aimed to be the pinnacle of technological and manufacturing development, a seamless blend of data and production, of IT and OT, operated by high-tech workers, spelling the end of challenges like defect and downtime, waste and waiting, and illuminating opportunities to design and make things better.
More than a decade on, while the ideal has been realised by some, wide-scale adoption of the technologies that enable such connectivity, especially among SME manufacturers, has been slow.
Helping SMEs catch up with the pack is the Made Smarter Adoption Programme, a government funded initiative providing businesses with specialist, impartial technology advice, grant funding for projects, digital transformation workshops, a leadership programme and broader skills development.
Since 2019 we have helped hundreds of businesses in the North West invest in a range of technologies to digitalise, decarbonise and drive growth. As a result these manufacturers are forecasting their investments will create almost 1,300 new jobs, upskill 2,400 existing roles, and deliver an additional £209M in gross value added (GVA) for the regional economy over the next three years.
The need for joined-up thinking
Our experience is that while SMEs are embracing automation in huge numbers, these machines operate in isolation and aren’t connected. And while some companies are early adopters to using basic software to support their processes, much of this technology is out-dated, not fit for purpose and creaking under bootstrapped workarounds to keep them operational and useful.
The barriers to adopting technologies to replace these legacy systems are resources, namely time and money, a loss aversion mindset and fear of failure, and the lack of skills to drive the necessary change.
To overcome these hurdles, Made Smarter has developed a process which lays the foundation to digital transformation and paves a potential path to a future smart factory.
A digital roadmap
We start with a digital transformation workshop where our impartial experts analyse a company’s products, services, processes and people to identify challenges and practical solutions.
The main outcome of this strategic work is a digital roadmap for manufacturers to select the right approach and the appropriate level of investment for their business at the right time in the right order to bring the greatest benefits.
At the heart of our approach is breaking down the big vision into small, manageable steps. It prevents digital transformation from becoming overwhelming, and looks for those easy wins which can demonstrate value to get buy-in across the business.
Skills
Skills mapping is a vital part of the workshop process. Whether that means bringing in a digital transformation expert or creating a digital champion from within the organisation, every plan needs a leader to drive the change.
Measuring success
Another other element of a digital roadmap is keeping it on track. By creating a baseline measure of the here and now, and capturing the changes over time, you can monitor progress and the impact, adjusting where needed to stay on course for the desired improvements. The measure of success will be aligned with your vision, whether that is smart factory status, or something more granular, such as improving production efficiency, reducing costs, improving customer experience or expanding into new markets,
The technologies
There is a purist view about Industry 4.0 and the steps that should be taken to achieve a truly smart factory that uses connected devices, machinery and production systems to continuously collect and share data across the organisation and its supply chain.
This starts with core technologies including sensors, used to collect real-time data from devices and machines at specific stages of the manufacturing process, and an Internet of Things software platform to collate and visualise that information.
Storing and processing this data then becomes important. This is where Cloud computing can replace traditional on-site storage, and enable feedback for decision-making in real time.
As more and more data is collected, Big Data analytics software can be deployed to achieve insights into how production processes are performing, spot error patterns, make better decisions and identify areas for improvement.
Once you have grasped managing the volume, velocity and variety, you can begin to deploy other technologies such as artificial intelligence and machine learning to achieve greater gains in predictive maintenance, process optimisation and quality control. It then becomes a virtuous circle: more data, more analysis, greater insight, more valuable outcomes.
The data enables the other part of the manufacturing equation by identifying the need or opportunity for other technologies such as automation or robotics to take over repetitive unskilled tasks, leading to increased efficiency and freeing up human resources for higher value work, or introducing additive manufacturing to achieve rapid prototyping.
Meanwhile, there is the potential for Virtual and Augmented Reality technologies to help operators to organise products, production tasks and the maintenance and repair of equipment, and digital twin technology to simulate a process or product to identify efficiency improvements and operations planning before it is made in the real world.
The proof is in the pudding
More than half of the 275 technology projects we’ve match-funded focussed on digital technologies which connect disparate systems and unify data residing in different sources - a major first step in the journey towards a smart factory
One example is Beverston Engineering, which makes precision components for aerospace, oil and gas and pharmaceutical industries, has worked with Made Smarter for the last four years to design a digital roadmap and invest in technology which provides real-time visibility of its manufacturing, and brought in new skills to accelerate data-led decision-making for future projects.
Projects in 2020 laid the foundations for connectivity, upgrading IT infrastructure with a dedicated machine data server to run the platform that collects data on state, current product, and maintenance status. Beverston also installed IIoT sensors to monitor the factory environment, giving another layer of data to contextualise analytics to the working conditions of machining assets. This infrastructure facilitates real-time asset monitoring, efficient handling and storage of big data.
Beverston has also created a 'productivity control room' - a bank of 18 big screens in the centre of the factory displaying real-time factory analytics, such as machine downtime events, availability, and performance metrics to the workforce. This can also be monitored remotely via a smartphone or tablet.
A second project in 2022 integrated all 20 machines and operators with its ERP and third-party systems and aims to reduce manual data input whilst delivering a platform that gives machine operators insight into machine OEE and productive efficiency in real-time.
What next?
The rapid pace of change means the conversation has already shifted to Industry 5.0, an emerging phase of industrialisation where humans work alongside advanced technology and A.I.-powered robots to enhance workplace processes.
It means we at Made Smarter need to redouble our efforts to reach more SME manufacturers and showcase the opportunities afforded by Industry 4.0 technologies and the smart factory vision. We need to demonstrate that growth can be green - that by increasing energy efficiency and reducing waste in production processes, the productivity gains can lead to significant reductions in greenhouse gas emissions.
Adoption programmes in the North East, Yorkshire and the Humber, and West Midlands are starting to have an impact, and with East Midlands and West of England programmes emerging, more UK manufacturers are now accessing the support they need to adopt technology and digital tools to increase growth, productivity, and efficiency.
Kevin Smith is lead technology adoption specialist for the Made Smarter Adoption Programme
For more information:
- Cake-making engineer inspires a new generation of women in industry
- Made Smarter-backed engineering firm hails 'phenomenal' impact after smart factory success
- Robotics and automation create manufacturing jobs
- Why North East manufacturers should consider the Made Smarter programme
- Spice Kitchen targets £2m sales and new jobs with tech investment
- Digital spare parts: innovation to solve supply chain woes
- £25m drive to confront turbulent manufacturing supply chains
- Data drives down equipment failure
- Improving maintenance processes through MSIN partnerships
- New fund to develop digital innovation
- Introducing Industry 4.0 to SMEs
- Enhance maintenance practices
- Digital transformation: Customer insight matters
- IoT digital experiments as a service
- Smarter maintenance: Paper available
- Condition monitoring & Industry 4.0
- Smart data collection
- Mechanised welding, cutting and Industry 4.0
- Tomorrow’s tech is here today
- The business value of Industry 4.0