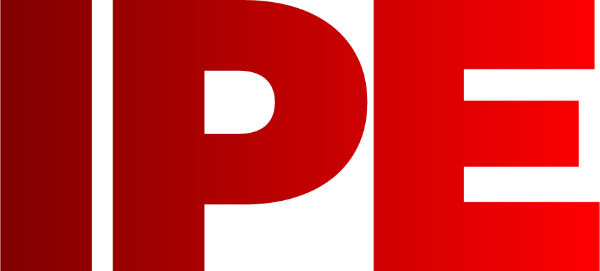
![]() |
Edward Lowton
Editor |
![]() ![]() |
Home> | Plant, Process & Control | >Industry 4.0 | >Technology and digital skills support help SME manufacturers achieve efficiency and innovation |
Technology and digital skills support help SME manufacturers achieve efficiency and innovation
24 September 2024
THE MADE Smarter Adoption programme in the North West has supported hundreds of businesses like Forth Engineering and BEP Surface Technologies, to embrace digital transformation as a route to sustainable growth

It has been five years since Made Smarter launched the first Made Smarter Adoption programme. The bold and ambitious plan was to equip North West SME manufacturers with the know-how and confidence to fully embrace the next industrial revolution, offering them access to a package of support which could boost growth, productivity, efficiency, decarbonise and create high value, well paid jobs of the future.
Despite weathering a cross wind of challenges, including the pandemic, Brexit, Ukraine and the subsequent supply chain disruption and labour shortages, rising energy prices and a cost of living crisis, the appetite for adopting technology and digital skills grew, and is continuing to do so.
More than 2,500 manufacturers have engaged with specialised support. Hundreds have reaped the rewards of intensive support including expert, impartial technology advice and digital transformation workshops to help them take their first steps to identify practical solutions to overcome business challenges.
Over 150 have embedded new digital skills into their operations through leadership programmes, internships and other training opportunities.
Made Smarter has match-funded 334 technology projects with companies who are starting to see the economic benefits. The North West forecast to see an increase of £242m in GVA in the coming years. What is more, is that these investments are creating 1,300 new jobs and upskilling 2,500 existing roles.
The achievement can be put down to a well designed model which puts people at the centre of the adoption of technology, and a flexible approach to delivering what SMEs need as new challenges and opportunities emerge.
This blueprint of success has so far been replicated in the North East, Yorkshire and the Humber, the West Midlands, East Midlands, and West of England. It is now poised to be rolled out to the whole of the UK from 2025.
There is a real local, regional and national approach to Made Smarter which enables organisations, large and small, at each stage of the supply chain network, to work together.
The National Commission continues to make the case to invest more in Made Smarter, not just in terms of productivity and growth, but also the positive impact on decarbonisation and net zero. Made Smarter is joining up different agendas for the government. And then there is our North West steering board, which now includes SMEs who have benefited from the programme, ensuring the programme remains relevant and forward-thinking.
The business impact of Made Smarter is well illustrated by two recent case studies: Forth Engineering is using extended reality and mixed reality to allow its clients to interact with 3D models of their assets, while BEP Surface Technologies has invested in a digital intern and control and automation technologies to help fine-tune its production process.
Case study 1: Engineering firm uses immersive technologies to drive innovation
They work closely with industry leaders in a wide range of sectors to help them deliver cutting-edge and ground-breaking solutions to complex problems.
With the support of Made Smarter - the government-backed movement to support SME manufacturers to adopt technology for growth - Forth is investing in a hardware and software solution which will allow a client to step into a virtual room and interrogate a 3D model of their asset.
Combining extended and mixed reality
They are adapting office space to create a mixed reality studio to enable customer demonstrations. 3D data of assets will be converted into a model using 3D visualisation software. This will allow the asset to be viewed within virtual/mixed reality environments in a true to life scale.
Forth will use a leading extended reality (XR) headset to project a clear and precise visual representation of the asset into a room at their facility. Meanwhile, mixed reality smart glasses are sent to the customer to access a virtual face to face meeting or inspection scenario from the safety and comfort of their own office. What is more, the smart glasses will create a hologram of the customer in the studio where they can interact and interrogate the asset, which can be animated and exploded into parts.
"We are creating a platform where two fantastic technologies meet. By taking the best of the headset’s ability to project a high intensity AR image and the smart glasses’ ability to import a hologram of a person, we can show clients their assets in staggering precision," MD Mark Telford explained.
"We hope that more customers will come to us with dreams of realising their prototype dreams through the use of mixed and virtual reality.
“We also hope to be able to open up the scope of work to clients from around the world and include them on engineering decisions from wherever they are whilst feeling like they are interacting with us and the project in person.”
The use of digitalisation, immersion, and presentation technologies will mean that Forth’s customers will now be able to interrogate a digital model of their assets from anywhere in the world; opening up new markets and increasing services offered to customers.
The project will be at the forefront of immersive technology and will also help to upskill staff, reduce cost and travel, and create a safe inspection environment.
Delivering innovative solutions
This groundbreaking technology will allow Forth to deliver innovative and novel solutions to complex problems globally. Moreover, the team of thirty-eight full time employees believe the value-added service will give it a competitive advantage as it is forecast to increase GVA by at least £500,000 over the next three years and in the process create five new, highly skilled jobs.
Forth believes this service will raise its profile in the global, harsh environment market and support its growth strategy to double turnover by £2m each year and help to upskill the team, secure jobs and increase job satisfaction.
"Our engineering solutions are giving customers new and accurate insights into the state of their assets, without risking their workforce, and ultimately saving them a considerable amount of money," Telford stated.
"The application of immersive technology will be a value-added service, offering our customers something no one else is. We hope that we can create a place of technological brilliance for the whole community around us, not just our customers."
"Made Smarter has enabled fuller and faster adoption of the new technologies and training, accelerating implementation by years.
Case study 2: Surface engineering specialist accelerates digital transformation with skills support
BEP Surface Technologies is a leading electroplating and surface finishing specialist based in Greater Manchester. The company provides an extensive range of chrome, nickel and copper plating services and surface finishing, dealing with turbines and large rotors for the energy sector through to small shafts and all types of rotating equipment.
With the support of Made Smarter, BEP embarked on a project to accelerate its digital transformation and decarbonisation journey, using a funded digital intern and investing in control and automation technologies.
Reducing energy usage
The bespoke solution has transformed the Radcliffe-based manufacturer’s chrome plating process by enabling real-time visibility of critical operational parameters, enabling enhanced monitoring and data analysis. The two-year project has cut energy use by 20%, material use by 10%, and labour use by 15%.
The scalable solution is now being rolled out to copper and nickel-plating operations. It integrates with BEP’s grinding machinery to introduce predictive maintenance strategies and monitor hazardous materials to enhance safety.
The digitalisation programme has also facilitated a cultural shift within the 54-year-old company. Reducing manual operation and monitoring is empowering engineers to drive continuous improvement initiatives.
"The successful implementation of our control and automation system has revolutionised our chrome plating process, fast-tracked our digital transformation and accelerated our net zero journey," said Andrew McClusky, MD of BEP Surface Technologies.
Utilising data to improve processes
"Like many heritage industries, electroplating and surface engineering has previously relied on operator skills and experience. Capturing that vital data from our processes enables ground-breaking control and automation, allowing our engineers to monitor and analyse comprehensive data sets and providing invaluable insights into process optimisation and energy efficiency.
"This project epitomises BEP’s commitment to innovation and excellence in manufacturing practices that have underpinned our work over the last half-century."
The chrome plating project was launched in 2022 as part of BEP's digital strategy. Made Smarter funded a six-month digital intern - Hassan Bin Mazhar, then an MSc student in Aerospace Engineering at the University of Salford - who was tasked with addressing the challenge of excessive chrome deposition during the plating process.
The project's first phase applied sensors to the plating tanks to enable real-time acquisition of operational data such as temperature, volts, amps, solution levels, solution composition, timings, and extraction efficiencies at each boiler. This was collated by a PLC and displayed in real-time via Human-Machine Interfaces (HMIs) to engineers who can precisely monitor and control parameters. A SCADA (Supervisory Control and Data Acquisition) software system was then deployed to centralise those readings and analyse them to offer new insights and enable engineers to optimise the process.
The next generation of engineering talent
Such was the project's success; BEP took on Hassan as an automation engineer, spending the last 18 months developing and scaling the solution.
"This project has been a dream start to my career. I gained hands-on experience in control and automation and was able to make a real-life impact on a challenge that had been niggling BEP for a long time," Hassan stated. "For BEP, it demonstrated what could be achieved through a small investment in technology and bringing in some new digital skills. It has also proved that kick-starting the digital transformation journey need not be elaborate or expensive."
This transformative shift has enabled BEP to transition towards a model that prioritises technical expertise over manual operation, upskilling the roles within the business and paving the way for growing the engineering workforce.
Made Smarter
Web: madesmarter.uk
- Helping SME manufacturers make the most of cobots
- New fund to develop digital innovation
- Why North East manufacturers should consider the Made Smarter programme
- Helping SME manufacturers realise the smart factory dream
- Emerging technologies used to navigate COVID-19
- How SME manufacturers are upskilling workers to create the teams of tomorrow
- Digital spare parts: innovation to solve supply chain woes
- £25m drive to confront turbulent manufacturing supply chains
- Improving maintenance processes through MSIN partnerships
- Made Smarter-backed engineering firm hails 'phenomenal' impact after smart factory success
- Introducing Industry 4.0 to SMEs
- Enhance maintenance practices
- Digital transformation: Customer insight matters
- IoT digital experiments as a service
- Smarter maintenance: Paper available
- Condition monitoring & Industry 4.0
- Smart data collection
- Mechanised welding, cutting and Industry 4.0
- Tomorrow’s tech is here today
- The business value of Industry 4.0