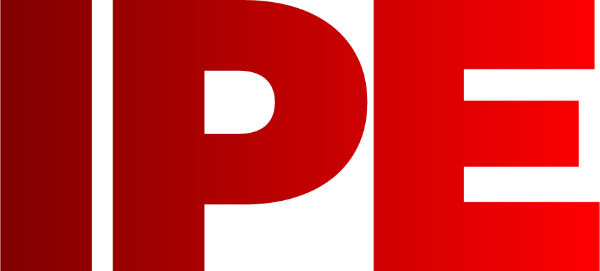
![]() |
Edward Lowton
Editor |
![]() ![]() |
Home> | Plant, Process & Control | >Industry 4.0 | >BEP Surface Technologies slashes energy use by 20% with data-driven project |
BEP Surface Technologies slashes energy use by 20% with data-driven project
19 March 2024
Ground-breaking control and automation system backed by Made Smarter enables real-time visibility and analytics. Two-year investment boosts operational efficiency and accelerates digital transformation and net zero journey

BEP SURFACE Technologies, a leading electroplating and surface finishing specialist, has cut energy use by 20% after investing in control and automation technologies.
The bespoke solution has transformed the Radcliffe-based manufacturer’s chrome plating process by enabling real-time visibility of critical operational parameters, enabling enhanced monitoring and data analysis.
The two-year project, backed by skills support from Made Smarter, has cut energy use by 20%, material use by 10%, and labour use by 15%.
The scalable solution integrates with BEP’s grinding machinery to introduce predictive maintenance strategies and monitor hazardous materials to enhance safety. It is now being rolled out to copper and nickel-plating operations.
The digitalisation programme has also facilitated a cultural shift within the 54-year-old company. Reducing manual operation and monitoring is empowering engineers to drive continuous improvement initiatives.
"The successful implementation of our control and automation system has revolutionised our chrome plating process, fast-tracked our digital transformation and accelerated our net zero journey," said Andrew McClusky, MD of BEP Surface Technologies.
"Like many heritage industries, electroplating and surface engineering has previously relied on operator skills and experience. Capturing that vital data from our processes enables ground-breaking control and automation, allowing our engineers to monitor and analyse comprehensive data sets and providing invaluable insights into process optimisation and energy efficiency.
"This project epitomises BEP’s commitment to innovation and excellence in manufacturing practices that have underpinned our work over the last half-century."
Supporting a digital internship
The chrome plating project was launched in 2022 as part of BEP's digital strategy. It was supported by Made Smarter, a government-backed programme helping SMEs adopt technology and skills, which funded a six-month digital internship to work with BEP.
Hassan Bin Mazhar, then an MSc student in Aerospace Engineering at the University of Salford, was tasked with addressing the challenge of excessive chrome deposition during the plating process.
The project's first phase applied sensors to the plating tanks to enable real-time acquisition of operational data such as temperature, volts, amps, solution levels, solution composition, timings, and extraction efficiencies at each boiler. This was collated by a PLC and displayed in real-time via Human-Machine Interfaces (HMIs) to engineers who can precisely monitor and control parameters. A SCADA (Supervisory Control and Data Acquisition) software system was then deployed to centralise those readings and analyse them to offer new insights and enable engineers to optimise the process.
A career launchpad
Such was the project's success; BEP took on Hassan as an automation engineer, spending the last 18 months developing and scaling the solution.
"This project has been a dream start to my career. I gained hands-on experience in control and automation and was able to make a real-life impact on a challenge that had been niggling BEP for a long time," he stated.
"For BEP, it demonstrated what could be achieved through a small investment in technology and bringing in some new digital skills. It has also proved that kick-starting the digital transformation journey need not be elaborate or expensive."
This transformative shift has enabled BEP to transition towards a model that prioritises technical expertise over manual operation, upskilling the roles within the business and paving the way for growing the engineering workforce.
BEP provides an extensive range of chrome, nickel and copper plating services and surface finishing, dealing with turbines and large rotors for the energy sector through to small shafts and all types of rotating equipment.
The business holds Fit for Nuclear (F4N) and ISO 9001, 14001 and 45001 accreditations.
For more information:
- Cardboard cutout manufacturer invests in AI and automation
- Digital spare parts: innovation to solve supply chain woes
- 750 new jobs from £12.6M technology investment
- Digital transformation confusion risks paralysing SME manufacturers
- Why North East manufacturers should consider the Made Smarter programme
- Cake-making engineer inspires a new generation of women in industry
- Relish the rise of the machines
- £25m drive to confront turbulent manufacturing supply chains
- Made Smarter powers SME manufacturers to invest £25m in technology
- Helping SME manufacturers make the most of cobots
- Introducing Industry 4.0 to SMEs
- Enhance maintenance practices
- Digital transformation: Customer insight matters
- IoT digital experiments as a service
- Smarter maintenance: Paper available
- Condition monitoring & Industry 4.0
- Smart data collection
- Mechanised welding, cutting and Industry 4.0
- Tomorrow’s tech is here today
- The business value of Industry 4.0