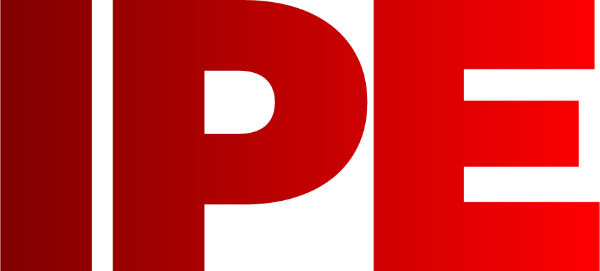
![]() |
Edward Lowton
Editor |
![]() ![]() |
Home> | Plant, Process & Control | >Valves and actuators | >XD4 pump ideal for wide variety of transfer applications |
XD4 pump ideal for wide variety of transfer applications
17 January 2023
AVAILABLE FROM ESE BV, the XD4 pump delivers up to 4 gpm (15 l/m) of oil flow. It is a self-priming and quiet-running vane pump for use in a wide variety of transfer applications with non-corrosive fluids such as oils and coolants. It can produce over 60 psi (4.1 bar) pressure at nominal voltages of 12 thru 24vdc.

Plumbing considerations
Excessive pressure drop caused by small pipes can be detrimental to system performance. Relative to ‘hydraulic pumps’ this is a high flow, low pressure pump. It is optimised for efficiency in transfer applications. Small suction pipes will starve the pump and reduce output flow by causing cavitation. Small pressure pipes will create excessive backpressure that will reduce output flow and system efficiency by loading and slowing down the pump motor. Therefore, elbows and long runs of pipe should be avoided. Each elbow and each inch of pipe has a cumulative effect. Pluming loses with cold or high viscosity fluid can easily add up to a large percent of available pressure when the plumbing is too restrictive.
The pump itself produces flow not pressure. Like a turnstile, every rotation of the pump delivers a metered volume to the other side. Whatever system is connected to the pump has flow resistance, which is the source of the backpressure as the pump works to maintain flow.
It is recommended that hose or pipe no smaller than 3⁄4” (19mm) at 24v or 1⁄2” at 12v be used and that the suction hose in particular is kept as short as possible and no longer than 36”.
Duty cycle and circuit protection
The XD4 pumps permanent magnet motor is capable of doing an extraordinary amount of work for its size but it is also the limiting factor for duty cycle. When it is loaded beyond about 7 amps. at room temperature it will begin to make heat at a rate that is higher than it can dissipate heat.
There are a number of factors that come into play in determining a safe duty cycle such as ambient temperature and airflow. In complex applications, the simplest way to determine the duty cycle may be thru direct experimentation. See chart 2 for basic duty cycle guidelines. Adding active cooling to the motor can substantially improved duty cycle.
The motor current varies with the viscosity and the pressure required to pump the fluid through the system. Many oil-based fluids have a substantial viscosity response to cold temperatures causing high motor current draws. We recommend the Bussmann CB251-15 breaker be used on the power supply line to protect the motor from thermal overload under adverse conditions. These particular breakers have an amp/time curve that closely matches the motor/pump combination to properly protect the pump within its operating envelope for up to 3 minutes of cumulative motor on time.
Product information
- DC POWERED POSITIVE DISPLACEMENT LIQUID PUMPS 12/24 VDC
- FULL-FEATURED
- FLOWS FROM L/HOUR TO 60 L/MIN
- TEMPERATURES TO 200 C
- CLEAR FLUIDS OILS AND WATER
- QUIET OPERATION
- UNIQUE DESIGNS WITH HIGH EFFICIENT PERFORMANCE
- DESIGN PRODUCES FLOW AND NOT PRESSURE. WHATEVER SYSTEM CONNECTED TO THE PUMP HAS FLOW RESISTANCE WHICH IS THE SOURCE OF BACK PREESURE AS THE PUMP THEN WORKS TO MAINTAIN FLOW
- APPLICATION ENGINEERING AVAILABLE FOR OPTIMUM PUMP SELECTION FOR SYSTEM REQUIREMENTS
For more information:
Email: [email protected]