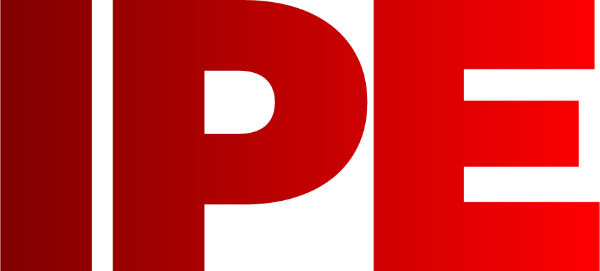
![]() |
Edward Lowton
Editor |
![]() ![]() |
Home> | Plant, Process & Control | >Valves and actuators | >Tips for optimum valve positioner performance |
Tips for optimum valve positioner performance
12 January 2024
There are some top tips to bear in mind for ensuring optimum valve positioner performance, while digital smart positioners are increasingly providing an attractive solution for valve control applications, says Jo Kirkbride

VALVES ARE a fundamental component in many facilities and are widely in water treatment plants, refineries and food and beverage factories. A vital part of the valve is the actuator used for opening and closing it - while some only allow two states, open or closed, many actuators can adopt a range of intermediate positions.
This is where valve positioners come in - they can alter the valve actuator's position based on a control signal to achieve the desired flow of process medium through the valve. They are usually used where rapid and accurate control is required without any error or hysteresis.
For sliding stem control valves, positioners are mounted on the yoke or top casing of the actuator or for rotary control valves, at the end of the shaft. Common to both is a mechanical feedback linkage to provide feedback to the positioner control unit. This allows the valve’s position to be compared with the position requested by the controller.
When a control signal is received that differs from the valve actuator’s position, the valve positioner sends a control signal to move the actuator. The feedback linkage confirms that the change has taken place and reports on the magnitude of the change.
Valve positioners offer several advantages for valve operation, the main ones being precise and accurate positioning of the valve actuator. They allow fine control with better resolution by using the full signal, which compensates for the inherent variability in the accuracy of the actuator system. A further advantage is their ability to cope with large variations in forces,
When to use a valve positioner
The key benefits of a valve positioner are speed of response and accuracy, and as such there are certain circumstances when valve positioners would prove beneficial. A secondary benefit is their ability to maintain a consistent valve position with varying process pressures.
Accuracy is important in production processes where the correct volume or flow of materials is required. This is particularly true of food & beverage applications where the volume delivered must adhere to a recipe to maintain consistency. The correct volume could be measured by a flowmeter, or through level measurement in the vessel with feedback data delivered to the process controller. In this application valve-positioners offer fast and accurate response to deliver product quality.
When there is a need to speed up valve response times as process conditions change valve positioners are invaluable. For example, if a change in flowrate is detected in a piping system the measurement would trigger an adjustment to the valve position, the continuous feedback loop delivers the correct valve position for the desired flowrate. The increased speed can be achieved because the positioner uses a higher pressure and air flow to adjust the valve.
A valve positioner can act as a ‘pressure amplifier’, increasing the pressure that an actuator can close against. This allows a consistent valve position to be maintained despite where a process medium experiences differential pressures, a situation that could cause the position of the plug in a plug valve to change.
Valve positioners are also useful when controlling valves with a wide throttling range or where the controlled process medium incorporates suspended solids or sludges.
Choose your positioner
There are four different types of valve positioners, all of which use either compressed air or electricity to move the valve actuator.
Powered by compressed air, pneumatic positioners receive pneumatic signals, and then supply the valve actuator with the correct air pressure to move the valve to the required position. Electric valve positioners perform the same function as pneumatic positioners, but instead of air pressure, they use electricity as an input signal.
Electro-Pneumatic valve positioners are a combination of the two, converting current control signals to the equivalent pneumatic signals.
A more modern alternative and one that is increasingly popular is the digital or 'smart' positioner. These devices use microprocessors to position the actuator while also monitoring and recording data. Digital positioners are very accurate and also use less air than traditional non-digital versions. They also offer the possibility of online diagnostic features.
Why it can pay to go digital
Digital positioners offer numerous benefits at the commissioning stage. Conventional positioners must be mechanically configured, which can take up to three or four hours for each valve. By contrast, digital positioners use an auto stroke routine to set themselves to the valve in just a few minutes. They also have a major maintenance advantage over mechanical positioners because they have fewer moving parts, reducing the disruption, time and cost associated with unplanned downtime, especially on sites with hundreds of valves installed.
The ability of digital positioners to communicate remotely using protocols such as 4-20mA, HART Foundation Fieldbus or Profibus also means that they can be sited in hazardous or difficult to reach areas.
Digital positioners are also less vulnerable to drift and can stick to their programmed tasks over a longer time than traditional positioners. Components are also generally smaller, making them less likely to be disturbed by events such as vibrations from plant or machinery. In fact, many users find that they never have to reset units following the initial commissioning – if attention is needed, digital positioners can easily be recalibrated using the same simple commissioning techniques, further limiting downtime.
Keeping an eye on diagnostics
The microprocessors typically used in digital valve positioners are much more capable than required for their control function. In fact, very little of their time or processing abilities is needed for operating the valve. Much of the functionality can therefore be dedicated to diagnostic tasks which can include friction analysis or troubleshooting. Friction analysis is particularly useful because excessive friction could indicate increased wear, leading to a valve that is more difficult to control.
Saving with digital positioners
One of the major attractions of using digital positioners is the chance to cut down on the use of air. With around 90% of the energy consumed by a compressor ending up as waste heat, compressed air is effectively ten times more expensive than electricity.
As an example of the savings that can made, consider the case of an application where positioners spend 50% of their operational time in a steady state position. If compressed air costs 1p per scfm (standard cubic feet per minute), the cost of this wasted energy could be as much as £2,106.78 per year.
Replacing these positioners with a digital positioner such as an ABB TZIDC could save between £500 and £1,200 per year per positioner.
Digital positioners can also make considerable contributions to maintenance savings. For example, in applications with constant or predictable loads, the amount of wear on control valves will most likely be very limited. The picture is very different for processes that experience more frequent or less predictable changes or where accurate control is critical. In these applications, it is vital to use equipment that can deliver a consistently fast response for as long as possible and digital positioners can offer this extended service.
In addition, the remote communications possible with digital positioners mean that engineers have no need to physically check every unit to determine which need attention, saving on time and resources.
Jo Kirkbride is product manager Actuators and Positioners and Force Measurement at ABB Measurement and Analytics UK and Ireland
For more information:
Tel: 01925 741111
- Double benefit
- Early warning
- ABB helps turn up the heat
- Guide to low voltage electric motors
- Steel maker set to save £68,000 on energy costs
- Power transmission catalogue
- New guide helps to simplify pressure transmitter selection
- ABB robots for processing and packaging feature in virtual exhibition
- Show debut for drives
- Driving down pumping costs