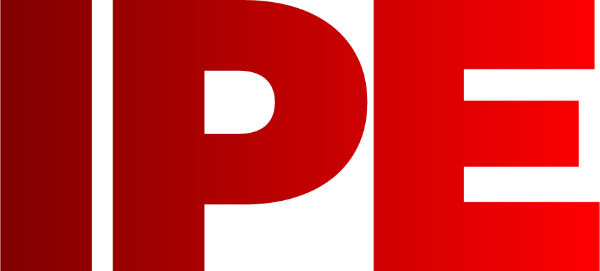
![]() |
Edward Lowton
Editor |
![]() ![]() |
Home> | Energy Management | >Motors and drives | >How is your electric motor feeling? |
How is your electric motor feeling?
01 November 2024
With electric motors forming the backbone of manufacturing, production, and assembly industries, thermography has an important role to play in reviewing their health
IF THE title of this article seems like a strange question, and you’re unsure why it might be relevant, then keep reading! If you’ve reached this second sentence, then presumably your business has some kind of reliance on electric motors somewhere. Maybe static motors powering conveyors or machinery, motors powering cranes or dollies that move around a production plant, motors fitted to materials handling vehicles or construction equipment, or some other installation of electric motors that keeps your production process operating as it must.
Electric motors are the backbone of manufacturing, production, and assembly industries. Whether you work in the automotive industry, pharmaceutical industry, food and beverage industry, or any other industry, there will be countless electrical motors powering your operation.
Electric motor health
How are those motors feeling? Are they well? A little unwell? Or barely hanging onto life, at the point of failure? If some of those electric motors are close to failure, then the next questions become: what impact will a breakdown have on your business? How long will repairs take? Do you have the skills, tools, and spare parts on-hand? Responding quickly to a breakdown is stressful, and will impact production quantity, delivery speed, customer trust and brand reputation. Therefore, responding quickly to equipment failures is vitally important.
While electric motors are the champion of this article, they are not the only unsung hero of typical production processes. They are often powered by switches, fuses and contactor plates found within electrical cabinets, which may even change voltages, balance electrical phases, or change between 3-phase and single-phase depending on the equipment in focus. How does each component in your electrical cabinet feel? Are they all happy, tired or at the point of failure too?
When we add together potential failures from electrical equipment, motors, bearings, and other equipment irrespective of whether it is electrical or mechanical, there are many potential points of failure in most manufacturing settings. Being able to react to failure quickly, with the right knowledge, tools, spares, and availability is an impossible task, so in stead of preparing for failure, why not discover the health of your critical assets using condition monitoring techniques?
One way to review the health of motors and other critical assets is to check their temperature. All equipment has a healthy operating temperature when working under normal conditions. Understanding what that temperature is for each piece of equipment that needs monitoring provides a healthy baseline to compare against in the future.
The role of temperature readings
Temperature readings of motors and assets can be taken with a thermal camera and a little guidance or training (online courses are easily accessible through the Infrared Training Centre (ITC)). However, there are a few pitfalls to avoid, for example,
- You wouldn’t want to take the temperature of something that is not running under normal conditions or has only just been turned on and is still heating up.
- If you are taking temperature readings at different angles, of different materials, qat different distances then this will cause the measurements to vary.
- Outdoor measurements need to be carefully taken to account for sun-loading, wind cooling and other atmospheric conditions.
- Factories are typically able to change their production speed depending on their demand, this needs to be considered to avoid drawing conclusions from different temperature readings based solely on production speed variations.
Taking several temperature readings for a particular motor at different times, under different electrical loadings, etc., will provide a range of measurements which indicates the healthy operating range for that motor.
These baseline temperature settings provide a reference to compare all future temperature measurements against, to indicate whether the motor is healthy, or beginning to indicate that something may need attention or repair.
Building a trend
Armed with the knowledge of what temperatures healthy equipment operates at, it is then possible to note future temperature readings to build a trend. This can be done at its most basic level in software like Microsoft Excel. However there are multiple specialist programs and applications to support trending to monitor equipment health; such as FLIR Ignite.
When a temperature reading of a particular piece of equipment begins to rise abnormally, you know it is time to investigate further. In dusty environments it could be something as simple as air cooling channels becoming blocked, and the ‘fix’ could be as simple as disconnecting a motor and cleaning it. However, increasing temperatures could be indicative or worn bearings, windings failing, or one of many other potential failure modes. At least this approach provides an early warning and gives the ability to investigate the problem before a surprise failure occurs.
The cost of taking temperature readings for predictive maintenance doesn’t need to be severe, with basic thermal cameras from FLIR such as the FLIR C5 or E5 Pro costing far less then a typical smart phone. These cameras can take temperature readings however their ‘thermal resolution’ is only suitable for basic inspections of simple equipment, where access is easy, and the equipment being assessed is in close range.
Tackling access challenges
For sites that are a little more complex and complicated, possibly with equipment installed at different heights or with access challenges then cameras like the FLIR E8 Pro or E76 would be more suitable. These cameras have a higher thermal resolution allowing more detailed temperature measurements to be recorded, and the E76 has interchangeable lenses allowing things like wide-angle lenses compatible with Infrared Windows in electrical cabinets, etc.
If thermography is something that you are interested in pursuing, then contact FLIR or one of their channel partners who sell the full range of thermal cameras and ask for advice and an in-person demo. The best experience is always to test a few cameras in your facility to identify which is the most appropriate match between your requirements and camera performance.
Predictive maintenance is a large topic and thermography is only one piece of the jigsaw. FLIR offers a range of acoustic cameras, vibration monitoring and test and measurement equipment, and software services to support complete condition monitoring regimes. When FLIR products are used together, there are built-in synergies to improve processes and make predictive maintenance easier.
For more information:
Tel: +44 (0) 1494 430240
- Smarter and more affordable
- Spot thermal imaging camera - see heat and measure it
- In the picture before you buy
- Tips on achieving meaningful images
- Advanced features at entry level
- Seeing infrared
- Camera passes electrician's test
- Thermal imaging camera
- Education discount package
- Flexible coil clamp meters aid inspection and navigation