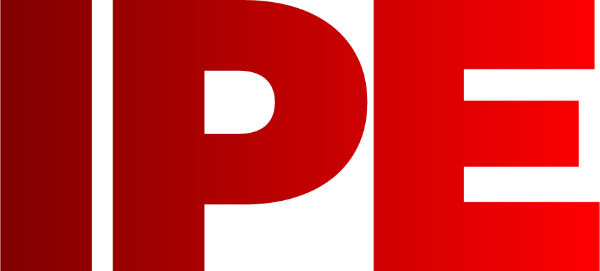
![]() |
Edward Lowton
Editor |
![]() ![]() |
Home> | Plant, Process & Control | >Sensors and instrumentation | >Precision sensors ensure wind turbine efficiency |
Precision sensors ensure wind turbine efficiency
22 November 2024
As wind turbines grow larger and are placed in more challenging environments, advanced automation systems and precision sensors are becoming essential for optimising performance, reducing wear, and enabling predictive maintenance, says Mark Weymouth

ALONG WITH the trend for wind turbines to increase in size and be positioned in hostile environments on hills or offshore, there is also a growing use of increasingly complex automation systems to optimise their performance.
The importance of optimising wind turbines
The high costs of wind turbines make their optimisation increasingly essential to maximise their economic value. The pitch of the turbine blades catching the wind is the primary means of adjusting the speed and generation output of the turbine. Blade pitch also enables the system to obtain a rotational speed best suited for conversion to the electricity frequency required for export to the electrical distribution grid.
The turbine may, for example, have its blades pitched to only catch some of the wind and so operate at a lower rotational speed. This approach reduces wear and tear on the wind turbine, especially when the wholesale electricity price is low, such as on a sunny afternoon when there is less demand.
Additionally, the use and complexity of preventative maintenance systems is increasing, for example, monitoring the vibration of rotating shafts and the wear of shaft couplings. These systems are vital for ensuring long-term operational efficiency and minimising downtime.
Advantages of analogue inductive sensors
Contrinex analogue inductive sensors are industry-leading in their precision, with long sensing ranges of up to 40mm, combined with precision measurement accurate to a few µm (microns). These sensors, located in the rotor, measure the distance to an eccentric lobe attached to the end of each blade to monitor the angle or pitch of the turbine blades.
Contrinex sensors provide a robust and precise system to replace more costly and fragile mechanical encoder solutions. The increasing placement of wind turbines in challenging environments with prolonged exposure to outdoor, often salt-laden air, further enhances the advantages of using these sensors over traditional encoder systems.
Maintenance applications
The fine resolution of the sensor’s measurement also enables it to be used for monitoring rotating shafts to detect vibration or track trends in movement as bearings wear. This technology replaces the traditional use of maintenance based on time or rotational count.
Another application measures the distance to a shaft coupling, providing a simple analogue voltage or current to the PLC. The precision of Contrinex’s analogue inductive sensor allows the measurement of movement as the seal wears over time, enabling predictive maintenance and scheduling the best time for coupling replacement.
Mark Weymouth is MD of PLUS Automation
For more information:
Tel: 07910 156 470
- Contrinex releases new Product Overview brochure
- Create double-sheets sensors using Contrinex SMART Sensors
- Weld-immune sensors ideal for resistance spot welding
- PISTOR provides precision control of valves and louvres
- 90 seconds to create custom nut detection smart sensor using the PocketCodr App
- Contrinex moves to new HQ building
- Eliminating hose-coupling bulk-handling errors
- Contrinex Inductive Ensures Automated Tool-Change on Hydraulic Press Goes Smoothly
- Satron Instruments debuts new website
- Contrinex's inductive sensors keep their cool on solder reflow oven