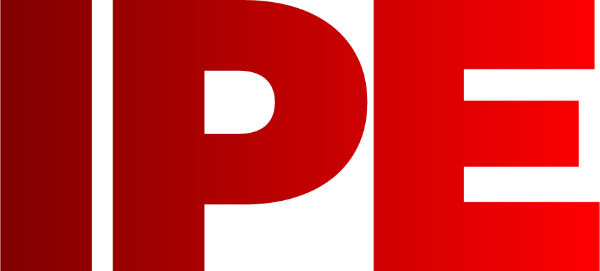
![]() |
Edward Lowton
Editor |
![]() ![]() |
Home> | Energy Management | >Building energy management systems | >Tackling energy blind spots |
Tackling energy blind spots
30 September 2022
The pressure on UK manufacturing firms for greater energy efficiency is intensifying as fuel costs rocket and government carbon emission targets loom. But are some manufacturers really doing all they can to achieve optimum energy efficiency, asks Paul Walsh

THE CURRENT geopolitical situation is causing significant supply chain disruption in UK energy markets. Russia's invasion of Ukraine is impacting gas and electricity wholesale prices, which are rising by up to 60% more than in European markets, and are continuing to further soar. The implication for high energy-use manufacturing firms is clear – to keep spiralling energy bills under control, action must be taken to prioritise energy efficiency.
Alongside this, the Government has pledged net-zero carbon emissions by 2050, with a 75% reduction by 2035, as set out in the Climate Change Committee’s Sixth Carbon Budget advisory report. With this ambitious target only 13 years away, energy-intensive manufacturing firms need to find financially viable ways to decarbonise their operations as a matter of urgency. The reality is achieving these goals will require commitment and strong leadership within these organisations.
A lack of support
Yet, as it stands, it can be argued that many manufacturing firms are not fully supporting facilities managers (FM) responsible for implementing energy efficiencies. This is the conclusion of a recent CIM whitepaper, The Energy Blind Spots. It revealed that of the 100 FMs interviewed for the report from tier 1 energy-intensive manufacturers, only 35% believed that energy costs, and more specifically, those relating to heating, ventilation and air conditioning (HVAC) are a high priority for the C-suite.
Considering that HVAC can account for up to 45% of a manufacturing site's energy consumption, a question can be posed – could senior management do more to enable FMs to effectively implement energy efficiency and sustainability measures? Doing so is clearly an ever-pressing priority, and if net-zero targets are to be achieved in manufacturing while ensuring firms remain competitive, leadership needs to better prioritise where efficiencies can be made. Considering their energy-intensive nature, HVAC equipment would be an ideal place to start.
However, CIM's research has shown how few manufacturing firms have a comprehensive plan for net-zero, with only 29% of FMs surveyed saying that they continually monitor carbon emissions. More eye-opening is that 63% of survey respondents' sites are ISO 50001 certified for energy management. This suggests a disconnect, and that unsupported facility management teams at UK manufacturers are struggling to implement practices that would save money and lower emissions.
Efficiency issues
In turn, this raises another challenge for manufacturing firms – managing and analysing the sheer volume of data generated by their building management system, which can be overwhelming for already under-pressure FMs. Such a situation can hinder efforts to reduce costs and emissions as FM teams face ‘alarm fatigue’ responding to a constant barrage of inefficiency alerts, which are either not prioritised correctly or are not addressed at all.
This issue is brought forward in the CIM whitepaper which found that 27% of respondents said BMS alarms go unactioned because too many notifications are received for teams to manage effectively. Tackling the concern shown from these statistics should therefore be a higher priority on manufacturers’ agendas, especially with the pressing need to reduce general operating expenses and meet carbon emissions targets.
Towards greater energy efficiency
Focusing on HVAC, improving energy efficiency can be approached in two ways. Either organisations can invest in new equipment at significant cost, which for some organisations may be prohibitively expensive. Indeed, 80% of survey respondents from The Energy Blind Spots stated that capital expenditure constraints are a major barrier to improving energy performance.
The alternative is to use more sophisticated and innovative building analytics platforms within existing building infrastructure and HVAC systems to drive OPEX savings. Such systems, which monitor all plant equipment and utilities, ingest existing building data and with a combination of fault detection and diagnostics alongside machine learning, can identify immediate operational concerns and provide clear, actionable insights to FM teams.
Operational and efficiency issues can then be addressed on site before they become critical, resulting in both environmental and economic savings. Underpinned by insights from mechatronic and electrical engineers, maintenance teams can pre-empt efficiency issues and identify areas where efficiency can be made.
Such hi-tech building analytics platforms empower FM teams to be proactive in their ongoing HVAC maintenance strategy, eliminating a culture of firefighting and alarm fatigue that may occur with manufacturing firms relying on BMS solutions. At organisations with inadequately commissioned BMS systems – as many as one in three firms, according to CIM’s report – the effect of implementing a platform that will help rather than hinder understanding and control of HVAC systems can be even greater still.
Advanced data analytics platforms ensure that HVAC efficiency improvements made do not degrade over time with continuous and ongoing monitoring, enabling on-site FM teams and remote HVAC engineers to better oversee equipment performance. As such, the 'fix and forget' mindset that can put FM teams in a loop of running repairs can be avoided. Instead, proactive steps may be taken to manage workloads, provide actions that more effectively reduce energy consumption and emissions, and deliver improved operational efficiency across both onsite and contractor teams.
The future
In conclusion, looking at CIM’s report, it can be argued that the interdependency between energy efficiency, sustainability and competitiveness may not have been fully recognised by senior stakeholders at UK manufacturing firms. Adopting a data-driven approach to energy optimisation and operational efficiency could help manufacturers maintain a competitive advantage in their sector.
Indeed, for some UK manufacturing C-Suite and senior leadership teams, energy efficiency remains a low priority. Consequently, FM teams are more likely to become trapped in a cycle of firefighting and alarm fatigue while profitability and competitiveness declines. As the country edges nearer to the Government's commitments to markedly reduced emissions by 2035 and net-zero by 2050, this issue of HVAC energy efficiency is becoming the proverbial elephant in the room.
Implementing an integrated building analytics platform with both machine learning algorithms and human engineering support could therefore transform manufacturing firm’s broader operational culture. Alongside this, it could drive a 'virtuous circle' of ongoing efficiencies and sustainability improvements, helping the sector brace for an uncertain energy future.
Paul Walsh is general manager – EMEA at CIM
For more information:
Tel: 020 8133 9490
- Esh-Stantec and Hauff-Technik collaborate to improve sealing solutions in UK water sector
- SME manufacturers help cut 3,850 tonnes of CO2
- Robust industrial tablet
- Why OSHA Training Still Matters in Modern Industrial Workspaces
- Industry 4.0 consulting, down-under style
- All round measurement solution
- Holding system to streamline small part machining
- Midlands manufacturers complain of being locked out of NHS PPE contracts
- Hard wearing, rapid drying floor screed
- Helping to triple turnover for Flying Fish