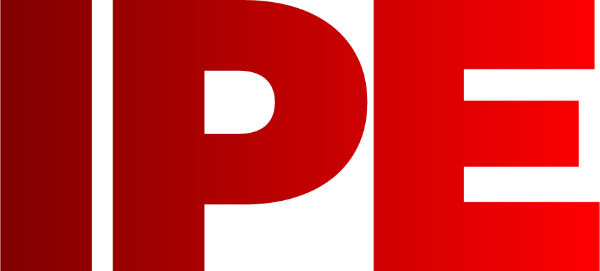
![]() |
Edward Lowton
Editor |
![]() ![]() |
Home> | Handbooks | >Maintenance Management Guide | >Effective and safe industrial lubricant management |
Effective and safe industrial lubricant management
03 July 2019
The importance of effective lubrication management cannot be underestimated, says the UK Lubricants Association.
Known as condition monitoring this system will ensure your lubricant remains in an effective state by reporting on the state of the fluid during operation to maintain its quality and performance characteristics.
Condition monitoring comprises of a series of steps to assess the lubricant quality in use. The condition of the lubricant can its effectiveness supporting industrial operations such as enabling the cutting, rolling and forming of metalworking processes as well as cooling and quenching.
In industrial processes lubricants perform a series of functions that enable machinery to operate effectively. The lubricant acts as a detergent keeping moving parts clean, a dispersant to hold sedimentary deposits in suspension and away from moving parts, a coolant to keep prevent machine temperatures and operations from overheating, it helps keep moving parts away from each other by way of a thin film that reduces wear, lubricants also help reduce friction and improve machinery performance.
Left unchecked the condition of the lubricant could break down in operation meaning that it cannot perform its core functions. Machinery operations would then become less effective and prone to overheating caused by a build-up of friction. Over time accelerated wear to bearings, gears and cutting tools could become prevalent leading to wear metals becoming deposited in the lubricant and, if left unchecked, eventual application or system failure might occur.
Effective condition monitoring prolongs the lubricant’s life, reduces downtime costs due to unplanned breakdowns and improve the effectiveness of metalworking processes.
Some lubricant suppliers, as part of their supply arrangements, will take over condition monitoring of the lubricant. The supplying company could make regular visits to the site or sites of the company, and assess the quality of the lubricant. Sometimes the organisation could take samples of the lubricant form the sump, in metalworking processes, and send this off to an external laboratory under the supervision of the lubricant company, for evaluation.
More recently condition monitoring has become more advanced with some lubricant companies using remote handheld devices held by the client at their premises, which will collect data and send it electronically back to the supplying company for remote monitoring.
No one way of condition monitoring is more effective than another but the important point is that it should be undertaken on a regular basis at the company’s premises. Not only does this ensure that the fluid is maintained in an optimum state for the benefit of metalworking processes, but it also helps prevent machine operators from being subject to health issues arising from poor fluid management.
Recently the Health & Safety Executive launched its strategy to ‘Help Great Britain Work Well.’ Over previous decades great improvements in the safety of industrial premises had been achieved so that the regulator turned their attention to the health of workplaces.
Metalworking fluid, as lubricants that are used in machining operations are called, are hazardous in nature. They often comprise of a base fluid, or carrier, supplemented by a number of different additives designed to help the fluid perform its functions. Managed correctly, metalworking fluids are safe to use. However some important steps are needed to ensure machine operators who come into close contact with these types of fluids, especially water-mix lubricants, are adequately protected.
Incidence of dermatitis can be reduced by the use of personal protective equipment. This may seem an obvious statement but it is important that the operator’s skin does not come into contact with the fluid. If the metalworking fluid is allowed to deteriorate or break down then it could become contaminated with tramp oil, wear metal particles or even bacteria and yeast.
Tramp oil is the name given to other types of oil-based substances that contaminate metalworking fluid. These occur due to their presence in other parts of the machine or arise due to other machinery operations. Examples of tramp oil include gear oil, sliding oil, hydraulic oil and even waxes. Like other foreign contaminants, the presence of tramp oil could interfere with the effectiveness of the metalworking fluid tramp oil and lead to an increased presence of micro-organisms.
The use of biocides in the metalworking fluid can help to manage contamination by micro-organisms such as bacteria and yeast. But even these additives can cause itching or redness if they come into direct contact with the skin such as hand or fingers.
The Control of Substances Hazardous to Health regulations or COSHH (2002) place a responsibility on the employer to carry out a risk assessment to ensure exposure is prevented and controlled, or minimised. In addition to the use of gloves, steps should also be taken to minimise or avoid altogether the risk of inhalation of metalworking fluid mist.
Metalworking fluid mist can cause lung disease in machine operators and a few simple steps can be taken to ensure that this risk is avoided. In close contact machine enclosures and mist control systems or LEVs (Local Exhaust Ventilation) should always be used. LEVs are designed to extract the fluid mist and expel it through a filtration system. If this cannot be done then the use of personal protective equipment should always be used supported by suitable health & safety training of machine operators, to identify and minimise any risk.
More recently some lubricant companies have begun to offer mist suppression fluids to the marketplace so it might be worth asking your supplier of the steps they would recommend you take to minimise any risk arising from fluid use.
The importance of good records management can also not be understated. COSHH sets down a responsibility for the company to keep adequate records for metalworking fluid inspections and checks for five years either electronically or paper. Employee health records and records of personal exposure should be retained for 40 years.
Taking a few simple steps can avoid health risks to your machine operators and other employees. For more guidance on the safe handling and disposal of metalworking fluids visit www.ukla.org.uk/metalworking-fluid-product-stewardship-group/.
- Healthy trucks, healthy site
- The Sound of Silence: Communicating with machines
- Inspection, test & monitoring: A choice of career development pathways
- Compressor efficiency: Specification matters
- Raising issues of concern
- Mattei explains why compressor maintenance is essential
- Maintec 2013: Innovation galore
- Co-Locations for Maintec 2014
- Maintaining strategies for success
- Considerations for machine tool maintenance