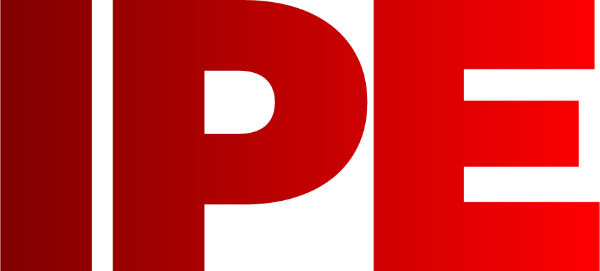
![]() |
Edward Lowton
Editor |
![]() ![]() |
Home> | Production Engineering | >Lubrication | >Taking care of metalworking fluids |
Taking care of metalworking fluids
18 October 2024
METALWORKING FLUIDS have been used for many years in machining operations in industry and is the name given to a variety of lubricants used in the rolling, forming, cutting and grinding of metal, usually carried out on CNC machines or lathes.

These metalworking fluids, or mwfs, come in two types; neat cutting oils and water-mix coolants. Both of which have very different purposes.
Neat Cutting Oils are largely made up of mineral-oil. They are designed to be used directly at the cutting head of the tool and help lubricate between the tool and the materials being cut by creating a film or barrier between the cutting head and the material being machined. This stops the cutting head coming into direct contact with the material being machined and reduces friction and wear.
These Neat Cutting Oils also help to clear away swarf or metal fines from the tool head to keep it clear of debris so providing a cleaner cut and are applied directly to the cutting tool or head.
Water-Mix fluids are complex mixtures of oils, detergents, surfactants, biocides and anti-corrosion agents. They are widely used as coolants, lubricants, and swarf or metal chip removers during machining operations. They also help to prevent surface corrosion of the machined parts and prolong the life of machine cutting tools. These types of fluids are designed to be mixed with water in an emulsion of 2%-10% emulsion by water. The appearance of these fluids can be opaque, milky or even transparent.
Ensuring health and safety
Although these fluids are safe to use in operation, a series of precautions are needed to be taken to avoid skin contact or inhaling metalworking fluid mist and care needs to be taken in handling, storage and disposal as you would expect with any chemical product.
Metalworking fluids are classified as chemicals and come under UK and EU chemical regulations. In Great Britain, chemicals have to be registered with the Health & Safety Executive, as the regulator, under the UK Registration, Evaluation, Authorisation and Restriction of Chemicals, or REACH, before being placed on the market.
In Europe, chemicals are registered with the European Chemicals Agency or ECHA, before being placed on the market. Northern Ireland continues to follow EU chemical regulations, but also participates in UK REACH through a light touch notification to the HSE of chemicals being placed on the market of Great Britain.
Regulatory compliance
Along with REACH, there are a number of chemical regulations which also cover metalworking fluids. Like all chemicals, mwfs are included in COSHH or the Control of Substances Hazardous to Health. The law requires that workers are protected from exposure to hazardous substances in the workplace. A COSHH assessment is required to be carried out by the employer in every workplace dealing with hazardous substances. Such an assessment includes identification of the hazard and an assessment of the risks they present, as well as steps taken to mitigate, reduce and control these risks in the workplace.
The Classification of Labelling and Packaging requires hazardous substances including chemicals to be correctly and accurately labelled throughout the supply chain to demonstrate to end users the risks associated with the products. Hazard statements and pictograms should be included on product labelling and associated Safety Data Sheets alert downstream users to the risks associated with the product.
The Biocide Product Regulation or BPR requires the use of any biocide to be pre-approved before being placed on the market. Biocides can be used in association with metalworking fluids as a way of managing bacteria in the fluid.
The Health and Safety Executive will often undertake a series of inspections of industrial premises including factories and workshops that use metalworking fluids to ensure that risks are being managed and workplaces remain safe environments. Last year, the HSE carried out a series of inspections and identified that common failings amongst inspected premises included not having local exhaust ventilation, not completing regular fluid quality checks, and failing to provide regular health checks for skin and lung conditions.
The importance of LEV
Local Exhaust Ventilation or LEV is designed to extract mist generated from the use of metalworking fluids in machining operations, typically in a CNC machine, from the area of working and expel this through a filtered system. Metalworking fluid mist can cause lung conditions when inhaled by machine operators and LEV should be fitted to CNC machines where operators are exposed to mist. Alongside LEV fitted to machines, the use of machine enclosures including guards and a timed door release mechanism on CNC machine enclosure will allow time for the working area to be cleared of metalworking fluid mist before the door is opened.
If you don’t have LEV fitted to your CNC machines then ask your fluid supplier for assistance. It is important that every machining workshop has regular contact with their fluid supplier who can advise on the right metalworking fluid to use matched to the material to be worked taking into account the environmental conditions, provide assistance on the right type of biocide and the correct treatment rates, along with associated matters like the use of LEV and Personal Protective Equipment or PPE.
LEV and Personal Protective Equipment are two ways that organisations can reduce the risk of ill health arising from the use of metalworking fluids amongst operators. By the use of machine enclosures with time-release delays and extracting metalworking fluid mist using LEV, the risk of inhalation can also be reduced or even removed from the workplace.
Using Personal Protective Equipment such as gloves, goggles and overalls, places a physical barrier between the metalworking fluid and the operator. Dermatitis can arise in the operator if their skin is directly exposed to metalworking fluids over time. The use of single-use nitrile gloves help prevent skin coming into contract with mwfs but care should be taken to avoid entanglement with machines. Using pre and post work cream on the hands can also minimise the risk of direct contact. Always follow HSE guidance when putting on and especially removing single use nitrile gloves to avoid skin contact with mwfs.
Reducing the risk of lung disease
Lung disease can be a risk for those working with metalworking fluids if precautions aren’t taken. Prolonged exposure to mwf mist can cause asthma and breathing difficulties. The use of mist filtration units and LEV can reduce or even eliminate this risk from the workplace. Similarly, care should be taken when using compressed airlines to clean down machines at the end of use.
Along with precautions when machining with metalworking fluids, just as important is to maintain the quality of metalworking fluid in use. Weekly dip slides checks for bacteria and CFUs or colony forming units, regular PH and tramp oil checks should be supplemented with daily visual checks to ensure any issue can be identified and managed at an early stage. This is not a comprehensive list of checks that need to be carried out and a more complete list can be found in the UKLA/HSE Good Practice guidance for The Safe Handling and Disposal of Metalworking Fluids which can be found here: tinyurl.com/5n8kmw56
United Kingdom Lubricants Association
Tel: 01442 875922
Email: [email protected]
Web: www.ukla.org.uk