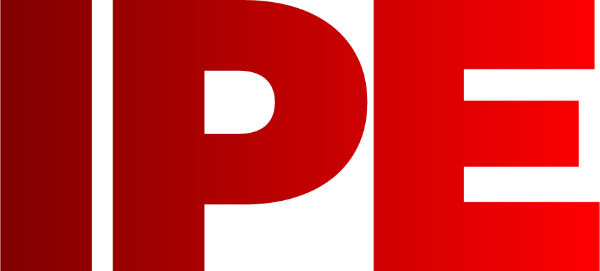
![]() |
Edward Lowton
Editor |
![]() ![]() |
Home> | Efficient Maintenance | >Lubricants | >Industrial lubricant management |
Industrial lubricant management
09 June 2020
Good lubricant management can contribute towards lower maintenance costs, reduced downtime, higher productivity and increased savings over the longer-term, asserts David Wright, Director-General of the United Kingdom Lubricants Association
Many manufacturing companies undertaking metalworking using rolling, forming or cutting methods, will require one of two types of lubricants called metalworking fluids.
Neat oils are hydrocarbon based and used to reduce friction at the cutting head surface where metal- to-metal contact occurs during machining. They create a thin lubrication film that separates the two surfaces to improve energy efficiency and the cutting process; they reduce the build-up and have become the dominant of heat caused by friction, reduce wear at the cutting edge, and remove chips and other metal fragments caused by these operations. Due to the higher cost of the initially filling up a sump, neat oils are typically used in more severe cutting operations or specific grinding operations where high quality surface finishing is required.
Other types of metalworking fluids called water-mix are used where cooling is the primary concern. These have a lower total cost compared to neat oils as they are mixed with water to form emulsions typically between 5-10% oil in water providing many of the same benefits of neat oils. Water-mix fluids were developed to improve machining operations, increase production rates, have become the dominant product type which also possess some cooling characteristics.
There are three main types of water-mix fluids:
- Conventional milky emulsions containing between 60% to 80% oil. They are usually the lowest cost water mix metalworking fluid, and require biocides to manage the growth of bacteria in the fluid. Their opaque appearance is due to the large size of oil droplets in the water which absorbs some the light passing through the fluid.
- Semi-synthetic translucent emulsions which contain between 5% to 60% oil; at the lower end of this concentration range the emulsions have a translucent appearance due to the smaller oil droplet size compared to the more opaque appearance of the higher concentration emulsions. These products may have a relatively long sump life because of the presence of additives which enhance the performance of the fluid, whilst also limiting bacteria growth. Should bacterial growth occur which cannot be prevented by standard measure, biocides may be added to maintain the quality of the fluid.
- Fully synthetic solutions are usually fully transparent in appearance and are completely water miscible. This product is typically free of oil and usually used for grinding operations. The addition of performance-enhancing additives means that the products can be used for a wide variety of operations. Should bacterial growth occur which cannot be prevented by standard adjustments to fluid quality, biocides may be added to maintain the quality of the fluid.
A wide variety of factors influence the choice of fluid, including the type of material, the extent of metalworking operations and the environmental conditions within which metalworking takes place.
Fluid monitoring
Many lubricant companies today will provide a fluid monitoring and supply service to their customers. The role of fluid monitoring is to maintain the fluid within its operating parameters, preventing over concentration, dilution, and contamination.
When the water content of a fluid exceeds the manufacturers recommended operating range, this can lead to metal corrosion and promote bacteria growth which in turn can result in poorer metalworking performance, increased maintenance costs and even machine shutdown.
If the fluid concentration exceeds the manufacturers recommended operating range this could lead to the fluid foaming, formation of sticky residues and deposits in the machine. This may also irritate the operator’s skin if personal protective equipment is not used.
In the wrong conditions, bacterial growth in a water-mix MWF can become a problem if left unchecked reducing machining performance and risking the machine operators’ health.
On-site services
Fluid providers often provide on-site services which include regular checks on the condition of the fluid. Other suppliers use computers and smart sensors to continuously monitor the quality of the fluid with the customer electronically recording bacteria levels. Software can be used to trigger alarms when parameters drift outside of their acceptable range, and some systems may include automated systems to adjust the fluid within the acceptable operating parameters.
To assist end users in managing the quality of their metal working fluids the UKLA working with other partners including HSE has published a Good Practice Guide. Some of the following advice is based on the content of this guide (http://www.ukla.org.uk/wp-content/uploads/UKLA-HSE-Good-Practice-Guide-for-Safe-Handling-and-Disposal-of-Metalworking-Fluids.pdf). This guide explains the risks to the health of machine operators and the responsibilities of employers to undertake health surveillance.
The Control of Substances Hazardous to Health regulations 2002 (COSHH) require that records of inspections or checks on the fluid are kept for a period of 5 years. Undertaking regular checks on the condition of the fluid can help to reduce the risks to the operators’ health which include skin (dermatitis) and lung disease. Operators need to be protected by minimising their contact and inhalation of metal working fluid mists as well from accidents and injuries. The use and maintenance of protective measures such as machine guards, machine door interlocks, Local Exhaust Ventilation (LEVs), and personal protective equipment is essential.
The use of weekly checks with pH test strips can ensure the fluid is maintained within the manufacturers’ recommended pH range which can be found on the product Technical Data Sheet (TDS). If in doubt, ask your supplier for a copy of the TDS. The pH of typical fresh emulsion should lie somewhere between 8.5 and 9.5.
The use of dip slides on a regular basis can help to identify when bacteria growth is occurring and alert users to take preventive actions to manage the quality of the fluid. The dip slide is used to count viable bacteria that form colonies on the slide which can be observed with the eye. Maintaining bacteria levels at or below 104 or 10,000 Colony-Forming Units (CFU)/ml is required but when counts exceed 104 CFU/ml this may indicate that bacteria are growing more rapidly. Immediate actions are required if the MWF is heavily contaminated with bacteria at or above 1,000,000 CFU/ml (106 CFU/ml) and appropriate actions may be the disposal of the MWF and a complete system clean.
The disposal of metalworking fluids should be undertaken only by an appropriately licensed and authorised waste contractor. Until such time, fluids should be stored safely pending collection and disposal. The fluids can be disposed of by splitting where possible to separate the aqueous component, which is then subject to treatment to separate out the oil which can be recycled.
The quantity of waste fluid along with associated disposal costs can be minimised by the use of a long-life, high quality, fluid and by maintaining good fluid management throughout the life of the product.
- Distribution
- Lubricants: Sampling, analysis and testing
- Gear lubricant based on water and synthetic base oil
- Oil consumption cut by 6000 to 7000 litres per year.
- Monitor for power transformers
- Lubricant support from online chat robot
- Lubricants, coolants and oil analysis
- Remote monitor for automatic lubrication systems
- Oil consumption cut
- Perils of improper lubrication