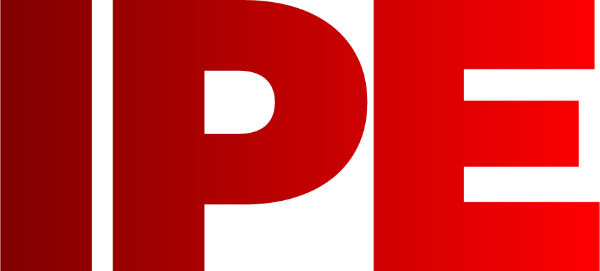
![]() |
Edward Lowton
Editor |
![]() ![]() |
Home> | Industry update | >Company news | >Bakers Basco 'on a roll' with efforts to bring bakery equipment attrition rates down |
Bakers Basco 'on a roll' with efforts to bring bakery equipment attrition rates down
19 March 2024
Attrition rates on bread baskets and dolly equipment used in the baking industry have fallen 4.34% and 6.63% respectively over the last year to reach their lowest levels in four years, new figures from Bakers Basco show.

DESPITE FLUCTUATING circumstances over the past 10 years due to exceptional events that have played a part in impacting equipment losses – the Covid-19 pandemic and driver shortages, for example - the combined attrition rates now reported for all equipment (bread baskets and dollies) have improved by 7.01% versus the same period in 2020-21.
Bread basket conversion, through theft and misplaced equipment, is an issue that has plagued bakers for many years. In the past, typical losses could be in excess of 60%. Since it was established in 2006, Bakers Basco, which was set up by Allied Bakeries, Fine Lady Bakeries, Frank Roberts & Sons, Hovis and Warburtons as a membership scheme to manage an industry-wide bakery equipment solution, has played a significant role in driving efficiencies of basket management across the industry.
The latest attrition rate figures - which for the period 2023-24 stand at -8.77% and -6.51% for baskets and dollies, respectively - Bakers Basco’s general manager Paul Empson says, come as a result of substantial improvement of efficiencies and streamlining operations. "Increasing stock counts across the supply chain at the end of each period gives the team a much better handle on the rates on a more regular basis," he explains.
With a current equipment pool of approximately 4.5 million Omega baskets and 450,000 dollies, Bakers Basco’s operations and investigations teams work daily to manage and recover the equipment on behalf of UK bakers.
Thanks to an increased focus on data and regular reporting, the team has been able to see much more clearly any store backlogs and blockages within the existing supply chain and conduct additional site stock counts. That, along with increased recovery of equipment from third-party abusers outside of the supply chain who don’t own the equipment, since stepping up its efforts in recent years through the strategic placement of GPS trackers and the national awareness poster campaign has helped to highlight the issues and delays in return of equipment.
"The whole collection process we operate today is more connected than ever before," explains Empson. "By taking a more measured approach to how we run the day-to-day business operations and with a particular focus on data and technology to support our efforts through stronger auditing and operational controls, it’s having a positive impact on bakery equipment attrition rates, while driving a more efficient and sustainable supply chain."
- UK Bakers Drives Sustainable Supply Chain with Lowest Equipment Losses in Five Years
- Counterplas signs three-year contract with Bakers Basco
- Bakers Basco boosts GPS trackers usage across equipment pool by 50%
- UK Bakers Call for Action as EFRA Launches Circular Economy Inquiry: Reuse Must Be Protected, Not Just Promoted
- GPS tracking tech leads to successful court action
- Northern Ireland bakers on high alert as Bakers Basco's investigations team report 34% boost in recoveries of misused bakery equipment
- GPS tracking tech leads to court action against Barkers Bakery over repeated misuse of bakery equipment
- Bakers Basco signs new agreements with Allied and Hovis