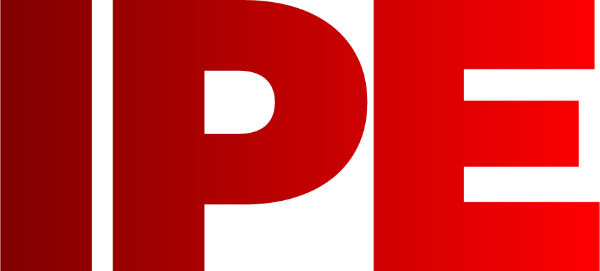
![]() |
Edward Lowton
Editor |
![]() ![]() |
Home> | Energy Management | >Compressors & ancillary equipment | >Latest blowers deliver savings |
ARTICLE
Latest blowers deliver savings
25 January 2013
Tests have shown that a new range of oil-free positive displacement screw blowers is on average 30% more energy efficient than conventional lobe solutions.Peter Lattaway, product support manager,Atlas Copco Compressors exp
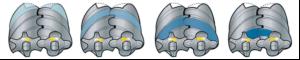
Tests have shown that a new range of oil-free positive
displacement screw blowers is on average 30% more energy
efficient than conventional lobe solutions.Peter Lattaway,
product support manager,Atlas Copco Compressors explains
The technical evolution in blower design for small volume flows (300 to 5000m3/h), has not advanced for 50 years.While 'Roots' type lobe blowers have been developed from 2-lobe to 3-lobe blowers, mainly to reduce the pulsation level, lobe blowers have not achieved significant improvements in terms of energy efficiency.
Atlas Copco Compressors determined that, in order to achieve this energy efficiency goal, a major advance in the design principle was needed. That innovation was the introduction of blowers using internal compression instead of external compression.
The external compression design of lobe blowers proved to be less efficient than the internal compression principle of screw elements. By designing blower screw elements dedicated for low pressure (0.5 bar(g)), dramatic energy savings are achieved resulting from improved energy efficiency and lower air outlet temperatures. Screw technology offers further advantages relative to noise, vibrations and reliability.
Atlas Copco Compressors' latest ZS range of oil-free, energy-saving positive displacement screw blowers, designed to meet today's low carbon economy needs, is proven to be on average 30% more energy efficient than conventional lobe solutions, as official tests confirm.
The performance of the new ZS screw blower was tested against a tri-lobe blower by the independent Technische Überwachungs- Verein (German Technical Monitoring Association), according to the international standard ISO 1217, edition4. In tests it was proven that the ZS is 23.8% more energyefficient than a tri-lobe blower at 0.5bar (e)/7 psig, and 39.7% at 0.9bar (e)/13 psig.
'Roots' type blowers are positive displacement machines consisting of a pair of two lobed or three lobed rotors, rotating inside an oval shaped casing. One rotor is driven by external power while the other rotor is driven by synchronisation gears. As the rotors turn, air is drawn into inlet side and forced out the outlet side against the system pressure. There is no change in the volume of air within the machine but it only displaces the air from the suction end to the discharge end against the discharge system resistance.
At the lobe blower delivery side, air at a higher pressure is present. When the rotor lobes uncover the exit port, air from the delivery side flows back into the flute space between rotor and casing. This back flow of air equalises pressure and compresses the entrapped air externally at constant volume.
Further the air is forced to the discharge line against the full system pressure Due to dynamic losses at inlet and discharge side, leakages and friction, the real compression work is increased. Subsequently the adiabatic efficiency of the blower will be reduced. The extra compression work for a lobe blower, compared to a screw blower, results in extra heat dissipation and consequently a higher outlet temperature.
Lobe machines' strong pulsations can lead to high operational noise levels and vibrations within the blower. Screw blowers deliver a stable flow and thanks to a better matching of internal pressure to external pressure, pulsation levels are reduced.
The oil free screw blower is a positive displacement machine, consisting of male and female rotor elements, which move towards each other while the volume between them and the housing decreases.
The rotors do not make contact and are synchronised by timing gears. Each screw blower has a fixed, integrated internal pressure ratio. To attain optimum efficiency, the internal pressure ratio must be adapted to the required working pressure.
At the beginning of the compression cycle, air at suction pressure fills the flute spaces as the rotors unmesh under the suction flange.
Air continues to fill the flute spaces, until the trailing lobe of the screw crosses the inlet port and the air is trapped inside the flute space. As the lobe meshes, the flute volume is reduced, causing the pressure to increase. Air is discharged from the flute space when the leading lobe crosses the discharge port.
Further rotation and meshing of the rotors forces this air to the discharge line.
Most compressed air applications do not always need the exact amount of air that is produced when a blower is running at its maximum flow and require the ability to change the delivered air flow. A screw blower with integrated variable speed drive allows the delivered air flow to be matched to the demand and results in significant energy savings. The combination of screw technology and a variable speed drive maintains a more stable efficiency across a wider operating range compared to a lobe blower.
Low pressure air is the backbone of many production processes, particularly in the aeration operations of wastewater treatment plants. A continuous, energy-efficient and 100% oil-free, low pressure air supply is equally essential for pneumatic conveying, flue gas desulphurisation and many other applications across the power generation and manufacturing sectors.
The technical evolution in blower design for small volume flows (300 to 5000m3/h), has not advanced for 50 years.While 'Roots' type lobe blowers have been developed from 2-lobe to 3-lobe blowers, mainly to reduce the pulsation level, lobe blowers have not achieved significant improvements in terms of energy efficiency.
Atlas Copco Compressors determined that, in order to achieve this energy efficiency goal, a major advance in the design principle was needed. That innovation was the introduction of blowers using internal compression instead of external compression.
The external compression design of lobe blowers proved to be less efficient than the internal compression principle of screw elements. By designing blower screw elements dedicated for low pressure (0.5 bar(g)), dramatic energy savings are achieved resulting from improved energy efficiency and lower air outlet temperatures. Screw technology offers further advantages relative to noise, vibrations and reliability.
Atlas Copco Compressors' latest ZS range of oil-free, energy-saving positive displacement screw blowers, designed to meet today's low carbon economy needs, is proven to be on average 30% more energy efficient than conventional lobe solutions, as official tests confirm.
The performance of the new ZS screw blower was tested against a tri-lobe blower by the independent Technische Überwachungs- Verein (German Technical Monitoring Association), according to the international standard ISO 1217, edition4. In tests it was proven that the ZS is 23.8% more energyefficient than a tri-lobe blower at 0.5bar (e)/7 psig, and 39.7% at 0.9bar (e)/13 psig.
'Roots' type blowers are positive displacement machines consisting of a pair of two lobed or three lobed rotors, rotating inside an oval shaped casing. One rotor is driven by external power while the other rotor is driven by synchronisation gears. As the rotors turn, air is drawn into inlet side and forced out the outlet side against the system pressure. There is no change in the volume of air within the machine but it only displaces the air from the suction end to the discharge end against the discharge system resistance.
At the lobe blower delivery side, air at a higher pressure is present. When the rotor lobes uncover the exit port, air from the delivery side flows back into the flute space between rotor and casing. This back flow of air equalises pressure and compresses the entrapped air externally at constant volume.
Further the air is forced to the discharge line against the full system pressure Due to dynamic losses at inlet and discharge side, leakages and friction, the real compression work is increased. Subsequently the adiabatic efficiency of the blower will be reduced. The extra compression work for a lobe blower, compared to a screw blower, results in extra heat dissipation and consequently a higher outlet temperature.
Lobe machines' strong pulsations can lead to high operational noise levels and vibrations within the blower. Screw blowers deliver a stable flow and thanks to a better matching of internal pressure to external pressure, pulsation levels are reduced.
The oil free screw blower is a positive displacement machine, consisting of male and female rotor elements, which move towards each other while the volume between them and the housing decreases.
The rotors do not make contact and are synchronised by timing gears. Each screw blower has a fixed, integrated internal pressure ratio. To attain optimum efficiency, the internal pressure ratio must be adapted to the required working pressure.
At the beginning of the compression cycle, air at suction pressure fills the flute spaces as the rotors unmesh under the suction flange.
Air continues to fill the flute spaces, until the trailing lobe of the screw crosses the inlet port and the air is trapped inside the flute space. As the lobe meshes, the flute volume is reduced, causing the pressure to increase. Air is discharged from the flute space when the leading lobe crosses the discharge port.
Further rotation and meshing of the rotors forces this air to the discharge line.
Most compressed air applications do not always need the exact amount of air that is produced when a blower is running at its maximum flow and require the ability to change the delivered air flow. A screw blower with integrated variable speed drive allows the delivered air flow to be matched to the demand and results in significant energy savings. The combination of screw technology and a variable speed drive maintains a more stable efficiency across a wider operating range compared to a lobe blower.
Low pressure air is the backbone of many production processes, particularly in the aeration operations of wastewater treatment plants. A continuous, energy-efficient and 100% oil-free, low pressure air supply is equally essential for pneumatic conveying, flue gas desulphurisation and many other applications across the power generation and manufacturing sectors.
MORE FROM THIS COMPANY
- Atlas Copco Unveils Enhanced TCX Chiller Range
- All in a typical week's work
- Additions to oil-free centrifugal compressor range
- Atlas Copco launches free guide to industrial cooling technologies
- New compressors boost energy savings
- Saving energy, running time and space
- Air compressors: New generation unveiled
- Re-design for energy recovery units
- Latest vacuum pumps: Potential for energy savings
- VSD rotary screw pumps: Cutting energy costs
OTHER ARTICLES IN THIS SECTION