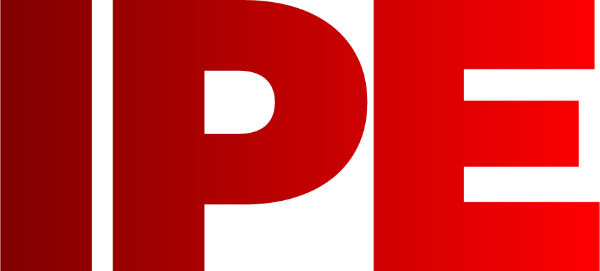
![]() |
Edward Lowton
Editor |
![]() ![]() |
Home> | Energy Management | >Compressors & ancillary equipment | >Simple solutions secure savings |
ARTICLE
Simple solutions secure savings
25 January 2013
Compressed air systems can account for up to 15% of all factory energy consumption, making them a prime target for potential savings.Here, Steve Prueitt,product manager air preparation with Parker Hannifin's Pneumatics Div

Compressed air systems can account for up to 15% of all
factory energy consumption, making them a prime target
for potential savings.Here, Steve Prueitt,product manager
air preparation with Parker Hannifin's Pneumatics Division
Europe, highlights simple methods of saving energy
Modern compressors are normally highly efficient, with variable speed controls being used to match operating speeds and thus power consumption to the demands of downstream pneumatics equipment. So, unless compressors are outdated or being operated and maintained incorrectly, there is only marginal room for improvement in this area.
By comparison, greater savings can be achieved by considering the performance and configuration of downstream systems. For example, ensuring that leaks from badly fitting tubes and fittings are prevented is an obvious but often neglected task, and one that can have a considerable impact on energy consumption.
Similarly, simple measures such as ensuring that inline filters, typically in dedicated FRL units, are cleaned or replaced at appropriate intervals, can reduce the problems both of pressure drop across each filter and the resulting increase in energy demand on the compressor.
A commonsense approach to basic maintenance is both logical and essential. It is, however, important to consider the design and construction of the pneumatic components being used throughout the compressed air system as, collectively, these can help to produce a major reduction in energy consumption.
In particular, efficiency can be enhanced by paying careful attention to the air flow paths through valves, manifolds, fittings and filters, to reduce pressure losses. As an example, Parker's Moduflex Extras coalescing and adsorption filters have been developed using computational fluid dynamic software, to calculate the ideal flow paths through inlet and outlet ports and across filter media under a diverse range of operating conditions. This has led to a number of improvements in internal flow geometries. These include a new bell mouth inlet design, which provides a full and unrestricted path for air entering the element chamber and reduces turbulence to a minimum, plus a smooth inlet elbow that efficiently directs air into the filter element.
The use of specially designed turning vanes within the flow path channel the passage of air in the most efficient manner, while flow distributors and conical flow diffusers fitted to each filter element ensure smooth air flow through the element.
It's worth recognising that the design of the filter element will affect energy efficiency. The latest elements use a deep bed pleated design, with high performance borosilicate glass nano-fibres to give a 96% voids volume and the maximum possible surface for effective filtration; typically, the available surface area can be up to 450% greater than that of traditional wrapped filter elements and around 200% more than standard pleated elements.
The overall effect is to reduce the velocity of the air as it passes through the filter element, giving excellent filtration efficiency, high dirt holding capacity and low pressure drop; the latter equates to a reduction in energy consumption that remains at a low level during the filter's normal operating life.
The potential savings from these new designs of filter can be substantial; for example, compared with a traditional filter unit of similar size and capacity, operating at a differential pressure of 200mbar, a modern deep pleated filter will produce energy savings of almost 5000kW per annum, or some 2100kg of CO2.
A similar approach can be taken to other pneumatic components. For example, the latest air preparation systems, such as Moduflex Lite, combine a lightweight and corrosionresistant injection moulded construction, with optimised air flow geometry providing greater efficiency with the opportunity to reduce operating pressure and save energy.
Interestingly, this technology has two additional benefits. Firstly, improved oil atomisation allows lubricating oil mist to travel far further along air lines without an increase in operating pressure; typically this can be more than 40m compared with the normal maximum of around 15m. Secondly, size for size, these products can be up to 45% lighter and smaller than conventional units while maintaining higher flow rates; this enables engineers to replace older devices with smaller, more affordable units that don't exceed tight budgets for capital expenditure.
For both old and new technologies, it's important not to forget the need to ensure that all pneumatic components are sized correctly for each application, as over-sized or over-specified devices will be more expensive to purchase and then cost more in terms of ongoing energy consumption.
It's a reasonable assumption that, for the foreseeable future at least, the cost of electricity to power factory systems will to continue to rise; at best it's unlikely to fall.
For some companies, counterbalancing this through an increase in prices at the factory gates may be an option; for most, however, it will be cost savings through improved energy efficiencies that will offer the best prospect of maintaining profit margins, with savings in the price of compressed air playing a vital role in this process.
Modern compressors are normally highly efficient, with variable speed controls being used to match operating speeds and thus power consumption to the demands of downstream pneumatics equipment. So, unless compressors are outdated or being operated and maintained incorrectly, there is only marginal room for improvement in this area.
By comparison, greater savings can be achieved by considering the performance and configuration of downstream systems. For example, ensuring that leaks from badly fitting tubes and fittings are prevented is an obvious but often neglected task, and one that can have a considerable impact on energy consumption.
Similarly, simple measures such as ensuring that inline filters, typically in dedicated FRL units, are cleaned or replaced at appropriate intervals, can reduce the problems both of pressure drop across each filter and the resulting increase in energy demand on the compressor.
A commonsense approach to basic maintenance is both logical and essential. It is, however, important to consider the design and construction of the pneumatic components being used throughout the compressed air system as, collectively, these can help to produce a major reduction in energy consumption.
In particular, efficiency can be enhanced by paying careful attention to the air flow paths through valves, manifolds, fittings and filters, to reduce pressure losses. As an example, Parker's Moduflex Extras coalescing and adsorption filters have been developed using computational fluid dynamic software, to calculate the ideal flow paths through inlet and outlet ports and across filter media under a diverse range of operating conditions. This has led to a number of improvements in internal flow geometries. These include a new bell mouth inlet design, which provides a full and unrestricted path for air entering the element chamber and reduces turbulence to a minimum, plus a smooth inlet elbow that efficiently directs air into the filter element.
The use of specially designed turning vanes within the flow path channel the passage of air in the most efficient manner, while flow distributors and conical flow diffusers fitted to each filter element ensure smooth air flow through the element.
It's worth recognising that the design of the filter element will affect energy efficiency. The latest elements use a deep bed pleated design, with high performance borosilicate glass nano-fibres to give a 96% voids volume and the maximum possible surface for effective filtration; typically, the available surface area can be up to 450% greater than that of traditional wrapped filter elements and around 200% more than standard pleated elements.
The overall effect is to reduce the velocity of the air as it passes through the filter element, giving excellent filtration efficiency, high dirt holding capacity and low pressure drop; the latter equates to a reduction in energy consumption that remains at a low level during the filter's normal operating life.
The potential savings from these new designs of filter can be substantial; for example, compared with a traditional filter unit of similar size and capacity, operating at a differential pressure of 200mbar, a modern deep pleated filter will produce energy savings of almost 5000kW per annum, or some 2100kg of CO2.
A similar approach can be taken to other pneumatic components. For example, the latest air preparation systems, such as Moduflex Lite, combine a lightweight and corrosionresistant injection moulded construction, with optimised air flow geometry providing greater efficiency with the opportunity to reduce operating pressure and save energy.
Interestingly, this technology has two additional benefits. Firstly, improved oil atomisation allows lubricating oil mist to travel far further along air lines without an increase in operating pressure; typically this can be more than 40m compared with the normal maximum of around 15m. Secondly, size for size, these products can be up to 45% lighter and smaller than conventional units while maintaining higher flow rates; this enables engineers to replace older devices with smaller, more affordable units that don't exceed tight budgets for capital expenditure.
For both old and new technologies, it's important not to forget the need to ensure that all pneumatic components are sized correctly for each application, as over-sized or over-specified devices will be more expensive to purchase and then cost more in terms of ongoing energy consumption.
It's a reasonable assumption that, for the foreseeable future at least, the cost of electricity to power factory systems will to continue to rise; at best it's unlikely to fall.
For some companies, counterbalancing this through an increase in prices at the factory gates may be an option; for most, however, it will be cost savings through improved energy efficiencies that will offer the best prospect of maintaining profit margins, with savings in the price of compressed air playing a vital role in this process.
MORE FROM THIS COMPANY
- Compact drive range extended
- Free drive configuration software
- Academic partnership
- Simple alternative to PLCs in pneumatic circuits
- 2000th ParkerStore opens
- Compact drive offers IP66 protection
- Maintec: Boost productivity with Parker
- Actuators introduced
- Driving forward green issues
- Parker releases high-performance automation controller based on IEC61131-3....
OTHER ARTICLES IN THIS SECTION