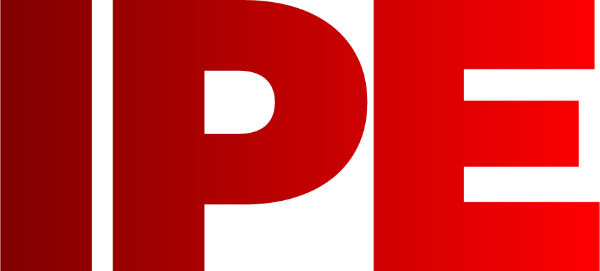
![]() |
Edward Lowton
Editor |
![]() ![]() |
ARTICLE
Lack of wear protection costing millions
25 January 2013
Insufficient wear protection in the UK bulk handling, extraction and recycling industries is costing millions claims Julian Brindley, sales and marketing director at Kingfisher Industrial.
Lack of wear protection in the UK bulk handling, extraction and recycling industries is costing millions claims Julian Brindley, sales and marketing director at Kingfisher Industrial.
Wear protection is the process of coating or lining process plant and equipment, such as cyclones, valves, bunkers, pipework, chutes (et al), with ceramics, metallics or polymers to extend their life and Brindley insists it is under-employed in the UK.
He says the heart of the problem is conflicting demands of reducing capital projects costs against the needs and expectations of maintenance managers and engineers, who inherit the plant after the usual 12- month warranty has expired.
In many instances the OEM has to achieve lowest installed cost for new equipment, in order to comply with project costs, while the maintenance manager is looking for minimised whole life costs from improved equipment reliability and longer operating life.
“Our field experience and calculations shows that it is far more profitable for companies in process industries to employ best practice from Day 1, rather than having to provide regular maintenance and repair of equipment at regular intervals due to problems associated with wear and erosion,†says Brindley.
“Reduced maintenance means reduced risk, reduced cost and more production uptime over longer periods - all of which are critically important to improve the efficiencies of companies in competitive markets.â€
Wear protection is the process of coating or lining process plant and equipment, such as cyclones, valves, bunkers, pipework, chutes (et al), with ceramics, metallics or polymers to extend their life and Brindley insists it is under-employed in the UK.
He says the heart of the problem is conflicting demands of reducing capital projects costs against the needs and expectations of maintenance managers and engineers, who inherit the plant after the usual 12- month warranty has expired.
In many instances the OEM has to achieve lowest installed cost for new equipment, in order to comply with project costs, while the maintenance manager is looking for minimised whole life costs from improved equipment reliability and longer operating life.
“Our field experience and calculations shows that it is far more profitable for companies in process industries to employ best practice from Day 1, rather than having to provide regular maintenance and repair of equipment at regular intervals due to problems associated with wear and erosion,†says Brindley.
“Reduced maintenance means reduced risk, reduced cost and more production uptime over longer periods - all of which are critically important to improve the efficiencies of companies in competitive markets.â€
MORE FROM THIS COMPANY
- The PPErfect equipment for staying out of harm’s way
- IP ratings: Protecting equipment from common environmental hazards
- Almost a third of SME manufacturers moving supplier base from EU to UK, according to new research
- Upgraded Lone Worker online management information tool
- T Levels: Make or break for Manufacturers?
- Reducing energy costs for manufacturers
- National eye health week: Employers urged to take action
- Critical infrastructure cyber attacks greater concern than enterprise data breaches
- Will wearable tech change the game for factory workers?
- Sustainability pays, says new research
RELATED ARTICLES
- No related articles listed
OTHER ARTICLES IN THIS SECTION