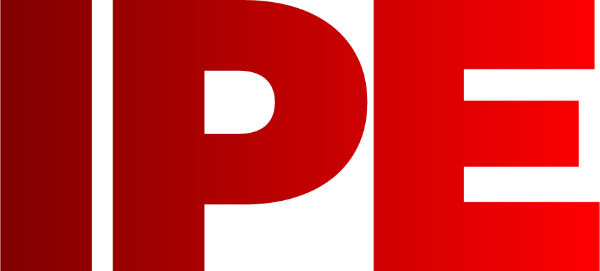
![]() |
Edward Lowton
Editor |
![]() ![]() |
Home> | Efficient Maintenance | >Reliability-centred maintenance | >Understanding preventive maintenance |
Understanding preventive maintenance
27 November 2023
While a significant number of businesses are familiar with the concept of preventative maintenance, its benefits can still be overlooked, suggests Charlie Green

ACCORDING TO a recent study by Oneserve, UK manufacturers face a staggering £180bn in costs annually due to unplanned downtime of critical assets. This alarming figure is a stark reminder of the financial repercussions of not having a robust maintenance strategy in place. In this context, preventative maintenance emerges not only as an option but a necessity to any business's maintenance strategy.
Understanding preventive maintenance
Preventive maintenance is a strategic approach that focuses on averting equipment failures by conducting regular inspections, routine maintenance, and preemptive repairs. According to IBM, through techniques like machine learning and operational data analytics, preventive maintenance can optimise maintenance routines, ensuring stable operations and resolving issues even before they arise.
The benefits of implementing preventive maintenance
1. Averting Downtime and Elevating Efficiency
Asset downtime translates to lost revenue, increased operational costs due to rush repairs, and potential penalties from unmet contractual obligations. Moreover, it can erode customer trust, as delays and inconsistencies can impact a company's reputation. Recent data from Infraspeak highlights that a staggering 93% of companies view their maintenance processes as inefficient. This signals that many businesses are precariously positioned on the edge of these disruptions.
Preventative maintenance is not just about averting equipment failures; it endeavours to ensure machinery and assets operate at peak efficiency, reducing the risk of unexpected breakdowns. A survey by PricewaterhouseCoopers found that a staggering 95% of respondents reported improvements in at least one key maintenance value driver due to predictive maintenance, with 60% witnessing a marked enhancement in equipment uptime.
2. Less Expenditure on Unexpected Repairs
In the intricate financial ecosystem of modern businesses, every decision has a ripple effect on the bottom line. One of these decisions is the choice between investing in preventive measures or relying on reactive maintenance strategies. While the former requires an upfront investment, the dividends it pays in the long run are undeniable. A study by Jones Lang LaSalle illustrates this, revealing that businesses can achieve savings of 12-18% by adopting preventive maintenance over its reactive counterpart. In addition to this, research by the National Institute of Standards and Technology highlights that reactive approaches can incur costs that are two to five times higher than preventive strategies.
3. Compliance with regulations
Preventative maintenance plays a pivotal role in ensuring businesses adhere to compliance regulations, safeguarding them from potential legal repercussions and financial penalties. One recent study found that regular maintenance can reduce the risk of non-compliance by up to 66%. This is because many industry-specific regulations, such as those in the pharmaceutical, food processing, and energy sectors, mandate regular equipment checks and maintenance to ensure safety and quality standards.
Non-compliance with regulations can lead to hefty fines, legal actions, and even business shutdowns. A report by the Aberdeen Group highlighted that businesses that prioritise preventative maintenance have a 90% compliance audit pass rate, compared to 68% for those that don't. This underscores the significance of preventative maintenance in not only ensuring operational efficiency but also in meeting regulatory standards.
4. Improved asset availability
Preventative maintenance is crucial for businesses aiming to optimise asset availability. According to The Association for Manufacturing Technology (AMT), asset availability is defined as "the percentage of potential production time during which equipment is operable, that is, operation is not prevented by equipment malfunction".
Maintenance teams play a significant role this process. They are tasked with minimising unplanned downtime and expediting equipment repairs when failures arise. By equipping maintenance technicians with essential tools and information, such as work order history, failure tracking data, and owner’s manuals, they can swiftly diagnose failures and devise solutions. Organised stockrooms, appropriate inventory levels, and efficient labour utilisation indirectly contribute to more streamlined maintenance. Advanced organisations also employ root cause analysis (RCA) and utilise failure codes to monitor equipment failures. RCA assists in pinpointing the likely causes of breakdowns and offers data to refine or establish preventive maintenance strategies.
Charlie Green is senior research analyst at Comparesoft
For more information:
Tel: 020 3963 5379
- Aerospace reaches new heights
- Irish manufacturer appoints new commercial director
- China predicted to overtake the US as the world’s leading pump producer by 2018
- UK manufacturers report near-survey record increases in stock holdings
- IP&E Awards 2024 Shortlist Announced
- Efficient material handling is key.
- Energy efficiency: Still top of the agenda
- ETG introduces 'cost conscious' Vulcan
- EarthSafe introduces new industrial cleaning solutions
- Annealed free-cutting steel
- Distribution
- Reliability strategy: New thinking required
- RCM : The quest for easier implementation
- Strong cast for Maintec theatres
- Top tips to keep your belts in business
- Boosting the scope of shrink fits with engineering adhesives
- Advanced pump analysis proves invaluable
- Hydraulic equipment maintenance & improvement
- Keeping your diesel engine healthy
- Optimising machine reliability