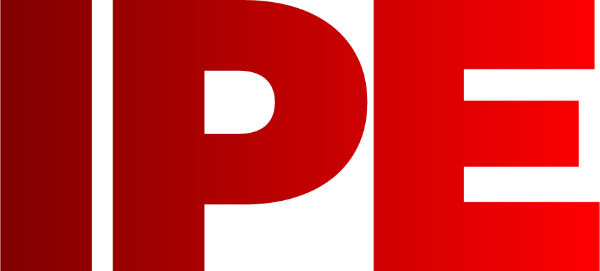
![]() |
Edward Lowton
Editor |
![]() ![]() |
Home> | Efficient Maintenance | >Maintenance products | >Getting a grip on performance |
ARTICLE
Getting a grip on performance
25 January 2013
To ensure that maintenance operations are controlled and managed effectively, those involved need access to the right information at the right time and in the right format.Mick Saltzer,managing consultant for Mainnovation

To ensure that maintenance operations are controlled and
managed effectively, those involved need access to the right
information at the right time and in the right format.Mick
Saltzer,managing consultant for Mainnovation explains how
an Enterprise Asset Management (EAM) system can help
EAM systems are commonly used by companies around the world to collect, store and manage maintenance data relating to their assets, providing facilities such as the ability to view equipment histories and to check whether spare parts are available in the stores.
Collecting and providing access to this mountain of data, however, does not in itself automatically guarantee that the right analyses and decisions will be made.
For the data to be of real value, it is essential to bridge the gap between strategy and operational execution by, for example, formulating department-relevant metrics on the basis of the company's business goals, ensuring accountability and making provision for intuitive modelling, monitoring and analysis. It is to achieve these objectives that the concept of Value Driven Maintenance (VDM) has been developed.
VDM provides a clear relationship between the working processes within an organisation's maintenance environment and the contribution that these processes deliver to value creation for that organisation. VDM will show, for example, whether the organisation needs to focus its efforts on improved equipment availability, strict compliance with legislation, smarter application of resources such as spare parts or, indeed, some combination of these.
In other words VDM, which is already being applied by companies such as Volvo Cars Manufacturing, GlaxoSmithKline, PepsiCo and Smurfit Kappa Packaging, helps the maintenance department develop a clear strategy with prioritised targets. In particular, VDM makes it possible to quantify the value potential of improvement activities using a set of formulas and, when this information is combined with benchmarking against a database of other users in related sectors, ensures that realistic targets are set.
To derive the maximum benefits from VDM or to derive the maximum benefits from your maintenance organisation/EAM system, effective monitoring is needed to provide continual confirmation that the maintenance department is moving in the right direction, and to provide reliable guidance relating to future process enhancements.
Due to the volume and complexity of the data available in a typical EAM system, significant challenges are involved in developing a monitoring system that provides the user with essential information in a form that is easily and quickly assimilated, yet also allows easy access to the underlying data that may be needed to address specific issues.
One of the best features of a monitoring system is that it provides an at-a-glance view, on a single screen of, say, the 10 most significant Key Performance Indicators.
Good practice is to choose one KPI per competence. The norm for the KPIs is based on validated benchmarking and achievable improvements. Once norms have been set correctly, a good monitoring system will enable the user to focus on deviations.
To support every KPI on the overview screen, the system should provide predefined information that allows users to positively identify the causes and trends that underlie the summary data. The necessary graphs, trend lines, pie charts, overviews and correlation diagrams should be calculated automatically, without the need for additional data entry.
In a well-designed monitoring system, every pointer in a graphic is a convenient starting point for further analysis. Every click gives a drill down to additional detailed information relating to the selection made until, at the lowest level, the works orders and/or notifications that are the root cause of deviations are identified.
To meet the need for a powerful yet easy to use monitoring system,Mainnovation, working with VCD Business Intelligence (Partner of SAP) and IBM, has developed the VDM Control Panel (VCP) application.
Meeting all criteria discussed in this article, VCP is more than a set of colourful graphics and meters; it is a step toward continuous improvement, underpinned by VDM as the chosen maintenance steering philosophy, and integrated with SAP EAM or IBM EAM (IBM Maximo) as powerful asset management systems.
VCP provides a link between strategy, processes and performance in maintenance operations, ensuring that these operations support the primary objective of every business - to maximise efficiency and profitability.
EAM systems are commonly used by companies around the world to collect, store and manage maintenance data relating to their assets, providing facilities such as the ability to view equipment histories and to check whether spare parts are available in the stores.
Collecting and providing access to this mountain of data, however, does not in itself automatically guarantee that the right analyses and decisions will be made.
For the data to be of real value, it is essential to bridge the gap between strategy and operational execution by, for example, formulating department-relevant metrics on the basis of the company's business goals, ensuring accountability and making provision for intuitive modelling, monitoring and analysis. It is to achieve these objectives that the concept of Value Driven Maintenance (VDM) has been developed.
VDM provides a clear relationship between the working processes within an organisation's maintenance environment and the contribution that these processes deliver to value creation for that organisation. VDM will show, for example, whether the organisation needs to focus its efforts on improved equipment availability, strict compliance with legislation, smarter application of resources such as spare parts or, indeed, some combination of these.
In other words VDM, which is already being applied by companies such as Volvo Cars Manufacturing, GlaxoSmithKline, PepsiCo and Smurfit Kappa Packaging, helps the maintenance department develop a clear strategy with prioritised targets. In particular, VDM makes it possible to quantify the value potential of improvement activities using a set of formulas and, when this information is combined with benchmarking against a database of other users in related sectors, ensures that realistic targets are set.
To derive the maximum benefits from VDM or to derive the maximum benefits from your maintenance organisation/EAM system, effective monitoring is needed to provide continual confirmation that the maintenance department is moving in the right direction, and to provide reliable guidance relating to future process enhancements.
Due to the volume and complexity of the data available in a typical EAM system, significant challenges are involved in developing a monitoring system that provides the user with essential information in a form that is easily and quickly assimilated, yet also allows easy access to the underlying data that may be needed to address specific issues.
One of the best features of a monitoring system is that it provides an at-a-glance view, on a single screen of, say, the 10 most significant Key Performance Indicators.
Good practice is to choose one KPI per competence. The norm for the KPIs is based on validated benchmarking and achievable improvements. Once norms have been set correctly, a good monitoring system will enable the user to focus on deviations.
To support every KPI on the overview screen, the system should provide predefined information that allows users to positively identify the causes and trends that underlie the summary data. The necessary graphs, trend lines, pie charts, overviews and correlation diagrams should be calculated automatically, without the need for additional data entry.
In a well-designed monitoring system, every pointer in a graphic is a convenient starting point for further analysis. Every click gives a drill down to additional detailed information relating to the selection made until, at the lowest level, the works orders and/or notifications that are the root cause of deviations are identified.
To meet the need for a powerful yet easy to use monitoring system,Mainnovation, working with VCD Business Intelligence (Partner of SAP) and IBM, has developed the VDM Control Panel (VCP) application.
Meeting all criteria discussed in this article, VCP is more than a set of colourful graphics and meters; it is a step toward continuous improvement, underpinned by VDM as the chosen maintenance steering philosophy, and integrated with SAP EAM or IBM EAM (IBM Maximo) as powerful asset management systems.
VCP provides a link between strategy, processes and performance in maintenance operations, ensuring that these operations support the primary objective of every business - to maximise efficiency and profitability.
MORE FROM THIS COMPANY
OTHER ARTICLES IN THIS SECTION