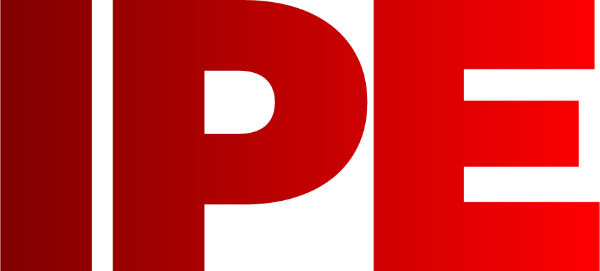
![]() |
Edward Lowton
Editor |
![]() ![]() |
Home> | Plant, Process & Control | >Sensors and instrumentation | >Less injection moulding rejects |
ARTICLE
Less injection moulding rejects
25 January 2013
The CoMo Injection system from Kistler Instruments is widely used to ensure minimum reject rates by monitoring and controlling in-cavity pressure in large scale injection moulding production. The launch of the new CoMo
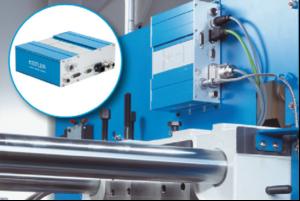
The CoMo Injection system from
Kistler Instruments is widely used
to ensure minimum reject rates by
monitoring and controlling in-cavity
pressure in large scale injection
moulding production. The launch of
the new CoMo Injection Basic brings
the same zero reject capability within
the reach of lower volume
production. The new version will be
especially useful to moulders
producing large, high value items,
such as car bumpers, where even a
small proportion of rejects can hit
profitability, says the company.
CoMo Injection Basic provides an interface to four in-cavity, piezoelectric pressure sensors to monitor the maximum pressure reached in each cavity. It also controls, via a digital output, a device such as a reject diverter or a robot, which separates any parts evaluated as being defective.
CoMo Injection Basic provides an interface to four in-cavity, piezoelectric pressure sensors to monitor the maximum pressure reached in each cavity. It also controls, via a digital output, a device such as a reject diverter or a robot, which separates any parts evaluated as being defective.
MORE FROM THIS COMPANY
OTHER ARTICLES IN THIS SECTION