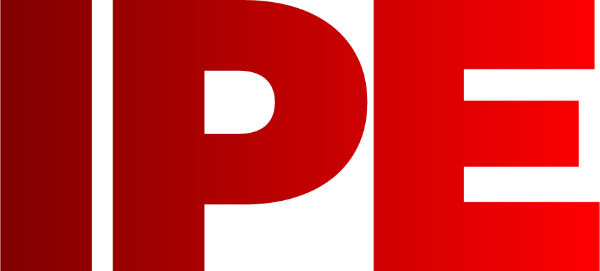
![]() |
Edward Lowton
Editor |
![]() ![]() |
Home> | Plant, Process & Control | >Events | >Learning about lean |
ARTICLE
Learning about lean
25 January 2013
'Eliminate waste and maximise efficiency' - this was the overriding message given to a group of delegates at the latest Lean Factory Group workshop, hosted in Andover. The Lean Factory Group, a consortium of seven sup
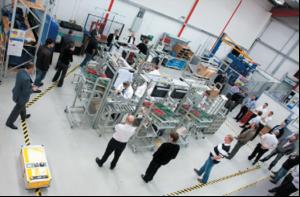
'Eliminate waste and maximise
efficiency' - this was the overriding
message given to a group of delegates
at the latest Lean Factory Group
workshop, hosted in Andover.
The Lean Factory Group, a consortium of seven suppliers to the manufacturing sector (iCart, Bosch Power Tools, Bosch Rexroth, K.Hartwell, Sick UK, SSI Schaefer and Spitfire Consultancy) provides manufacturers with hands-on advice and guidance on innovative, yet practical lean manufacturing solutions to boost productivity.
A demonstration manufacturing cell, set-up within SSI Schaefer's HQ, provided a practical and visual way of educating manufacturers to the benefits of lean implementation.
There were presentations on the theory and benefits of the lean approach, including value stream mapping, KANBAN boards and workplace design. However, it was the practical session within the cell that gave visitors the chance to compare their own production plant and really examine the operation behind a lean manufacturing cell.
For further information about the Lean Factory Group and the next series of workshops please visit www.lean-factory.co.uk
The Lean Factory Group, a consortium of seven suppliers to the manufacturing sector (iCart, Bosch Power Tools, Bosch Rexroth, K.Hartwell, Sick UK, SSI Schaefer and Spitfire Consultancy) provides manufacturers with hands-on advice and guidance on innovative, yet practical lean manufacturing solutions to boost productivity.
A demonstration manufacturing cell, set-up within SSI Schaefer's HQ, provided a practical and visual way of educating manufacturers to the benefits of lean implementation.
There were presentations on the theory and benefits of the lean approach, including value stream mapping, KANBAN boards and workplace design. However, it was the practical session within the cell that gave visitors the chance to compare their own production plant and really examine the operation behind a lean manufacturing cell.
For further information about the Lean Factory Group and the next series of workshops please visit www.lean-factory.co.uk
MORE FROM THIS COMPANY
- Boosting Operational Efficiency
- Creative conveyor solutions
- Tall order from Wine Society
- SSI Schaefer on Stand Number E122
- Partnering approach to logistics & material flow
- Pick and pack
- SSI Schaefer's Salver Service for Spares
- Helping boost cold store efficiency
- Porsche gets a lift with SSI Schaefer's Vertical Storage System
- Two-tier storage
OTHER ARTICLES IN THIS SECTION