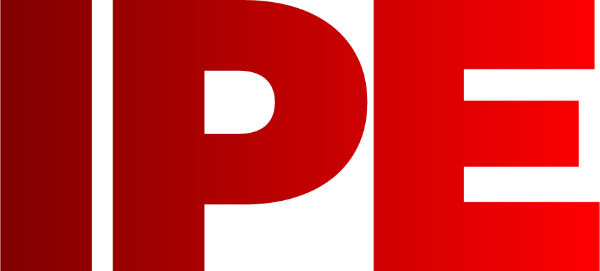
![]() |
Edward Lowton
Editor |
![]() ![]() |
Home> | Plant, Process & Control | >Process equipment | >Crosslapper control |
ARTICLE
Crosslapper control
25 January 2013
In response to industry demand, ABB and specialist textile machinery company, Tatham, have developed technology to provide higher production speeds with improved product weight distribution for crosslapper control.
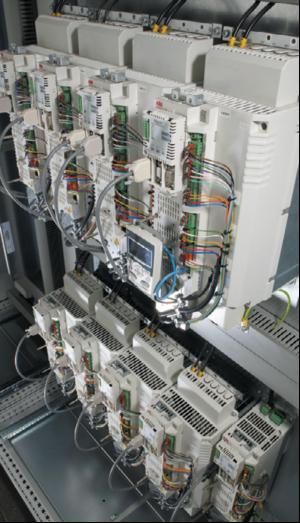
In response to industry
demand, ABB and specialist
textile machinery company,
Tatham, have developed
technology to provide higher
production speeds with
improved product weight
distribution for crosslapper
control.
A crosslapper accepts a lightweight fibre web from a carding machine and uses it to build up a heavier web in layers (known as a batt). The crosslapper overlaps the layers by means of a complex arrangement of conveyors and reversing mobile carriages that turn the material through 90°. Typical end-products include automotive textiles, bedding, industry felts and filtration media.
Tatham's latest TSX control system utilises ABB machinery drives and servomotors. Several panel combinations are available depending on the existing crosslapper configuration.
The system is linked to the master process control using Profibus, an ABB AC500 PLC provides positioning data to the drives which convert it into control signals to maintain the speed of the servomotors.
A crosslapper accepts a lightweight fibre web from a carding machine and uses it to build up a heavier web in layers (known as a batt). The crosslapper overlaps the layers by means of a complex arrangement of conveyors and reversing mobile carriages that turn the material through 90°. Typical end-products include automotive textiles, bedding, industry felts and filtration media.
Tatham's latest TSX control system utilises ABB machinery drives and servomotors. Several panel combinations are available depending on the existing crosslapper configuration.
The system is linked to the master process control using Profibus, an ABB AC500 PLC provides positioning data to the drives which convert it into control signals to maintain the speed of the servomotors.
MORE FROM THIS COMPANY
OTHER ARTICLES IN THIS SECTION