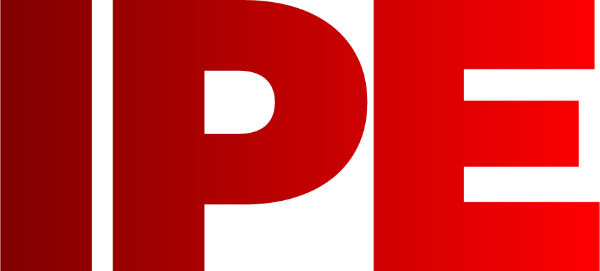
![]() |
Edward Lowton
Editor |
![]() ![]() |
Home> | Plant, Process & Control | >Pneumatic equipment | >PNEUDRI - Highest efficiency dry compressed air |
ARTICLE
PNEUDRI - Highest efficiency dry compressed air
25 January 2013
For maximum manufacturing uptime, high-efficiency PNEUDRI adsorption dryers need to be installed to not only provide the best quality air, but also prevent corrosion and inhibit microbiological growth.
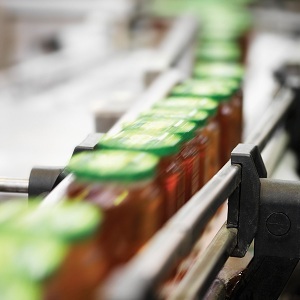
For maximum manufacturing uptime, high-efficiency PNEUDRI adsorption dryers need to be installed to not only provide the best quality air, but also prevent corrosion and inhibit microbiological growth.
Adsorption dryers can be large energy consumers, specifically during desiccant regeneration. However, the power requirement is usually optimised for maximum design conditions, i.e. 100% of rated flow, minimum pressure and maximum temperature.
Consequently, Parker domnick hunter has developed an energy management system, DDS (Dewpoint Dependent Switching) which continually measures the operating parameters of the dryer and adjusts its regeneration cycle according to the levels of moisture present in the system at any given time.
For example, in a compressed air system with a 160 KW compressor and a PNEUDRI MX heatless desiccant dryer installed, and typically averaging 70% of rated flow, DDS could save the user 153,000 KW of energy every year, simply by extending the cycle time to match decreased operational demands. This equates to an annual environmental saving of 66,000 kg of CO2.
By installing OIL-X EVOLUTION pre- and after filters in place of traditional filters, the energy savings are increased by a further 58,000 KW. In total, this equates to an energy saving of 211,000 KW and an environmental saving of 91,000 kg of CO2 per annum.

Adsorption dryers can be large energy consumers, specifically during desiccant regeneration. However, the power requirement is usually optimised for maximum design conditions, i.e. 100% of rated flow, minimum pressure and maximum temperature.
Consequently, Parker domnick hunter has developed an energy management system, DDS (Dewpoint Dependent Switching) which continually measures the operating parameters of the dryer and adjusts its regeneration cycle according to the levels of moisture present in the system at any given time.
For example, in a compressed air system with a 160 KW compressor and a PNEUDRI MX heatless desiccant dryer installed, and typically averaging 70% of rated flow, DDS could save the user 153,000 KW of energy every year, simply by extending the cycle time to match decreased operational demands. This equates to an annual environmental saving of 66,000 kg of CO2.
By installing OIL-X EVOLUTION pre- and after filters in place of traditional filters, the energy savings are increased by a further 58,000 KW. In total, this equates to an energy saving of 211,000 KW and an environmental saving of 91,000 kg of CO2 per annum.

Related articles
MORE FROM THIS COMPANY
- Escaping air:Major drain on resources
- If you compromise on filter element technology do you run the risk of threatening your facilities efficiency and productivity?
- Meeting ISO 8573-1:2010 improves energy saving, productivity and profitability
- The OIL-Xplus ADVANTAGE – taking energy saving to the next level
- Queen's Award
- Why compromise air quality for the cost of a filter element?
- Parker Chomerics introduces SOFT-SHIELD 4840 and 4860
- Energy savings promised
- Compressed air drying solutions for every application
- Are all compressed air filters the same?
OTHER ARTICLES IN THIS SECTION