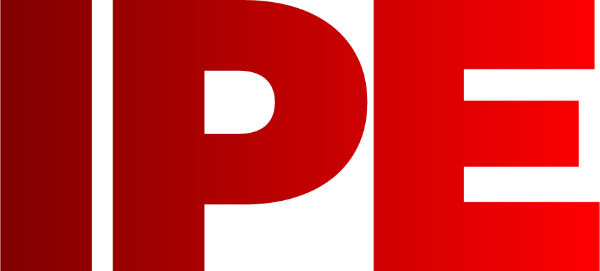
![]() |
Edward Lowton
Editor |
![]() ![]() |
Home> | Plant, Process & Control | >Pumps | >Time to pump up the planning |
ARTICLE
Time to pump up the planning
25 January 2013
Andy Cruse of ERIKS explains how an organised action plan, incorporating regular analysis, maintenance and condition monitoring, can help to maximise pump efficiency Where pumps are concerned, the best way to make sav
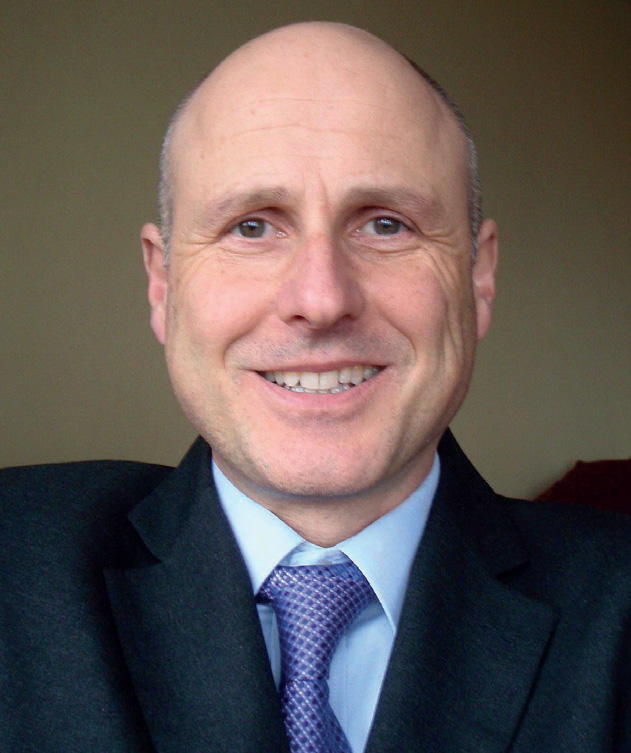
Andy Cruse of ERIKS explains how an organised action plan,
incorporating regular analysis, maintenance and condition
monitoring, can help to maximise pump efficiency
Where pumps are concerned, the best way to make savings is by finding ways to control whole life costs. The purchase price of a pump generally represents no more than 5% of its total life cost and so any plan to enhance overall pump efficiency must be based on achieving the best energy efficiency.
The good news is that there are many steps that can be taken to increase energy efficiency and by combining these methods into an organised pump action plan you can make a big difference to plant performance.
Key pump performance data, including calculations of head and flow, system resistance, power use, and efficiency, can be rendered on a graph to provide valuable information; for example, a centrifugal pump usually displays a rising rate power characteristic and so considering a graph that clearly displays this characteristic will help determine at what level you risk overloading the motor. Precise pump data can also identify problems that can then be directly addressed; for example, reduction in flow may indicate corrosion and scale buildup in the pump casing, or increased running clearances.
Pump maintenance needs to be regular and informed. We estimate that maintenance costs are less than 10% of a pump's lifetime cost but good maintenance can significantly improve efficiency and minimise energy expenditure.
Wear and tear is unavoidable but in pumps, where abrasive particles and poor water quality lead to erosion and corrosion, attention to the most vulnerable areas can maximise efficiency. For example, wear to the neck rings leads to an increase in clearance. This in turn causes leakage and recirculation from the high pressure area of the pump casing back to the suction side of the impeller. The result of this is reduced head and flow, which is a constant cause of poor energy efficiency if not managed correctly.
A clear action plan can help you manage these issues and enable the implementation of a scheduled maintenance regime that is suitable for the needs of your operations. To help identify some key steps in the process, we've put together the following summary of things you should consider.
Begin by estimating the energy cost of running your pumps and first focus on the equipment that uses the highest level of energy. It may be possible to retrofit energysaving features, the costs of which can soon be recovered by efficiency gains. Stage two of your action plan should be to introduce efficient condition monitoring practices, routine checking and data logging of pump performance. This should be followed by repairs and refurbishments, such as the application of wear resistant coatings, and the replacement of leaking seals.
Having attended to urgent requirements and put in place measures to monitor and maintain your pump equipment, you can then plan further ahead by spreading a basic knowledge of pumping principles and energy-saving initiatives among engineers.
Of course, a fully detailed action plan would be far more specific than the one described above but our summary illustrates the framework and key considerations of such a plan. You can either implement an action plan yourself or enlist the help of a specialist supplier such as ERIKS; the cost will be repaid through the resulting savings in energy costs and in most cases that cost is repaid swiftly. Considering that, in some applications, energy costs for pumps can actually rise to as much as 95% of the whole life cost, there are huge savings to be made through more efficient pump operation and more effective maintenance.
By following a strong action plan, you will be able to optimise your equipment and keep it optimised into the future to obtain maximum energy efficiency.
Where pumps are concerned, the best way to make savings is by finding ways to control whole life costs. The purchase price of a pump generally represents no more than 5% of its total life cost and so any plan to enhance overall pump efficiency must be based on achieving the best energy efficiency.
The good news is that there are many steps that can be taken to increase energy efficiency and by combining these methods into an organised pump action plan you can make a big difference to plant performance.
Key pump performance data, including calculations of head and flow, system resistance, power use, and efficiency, can be rendered on a graph to provide valuable information; for example, a centrifugal pump usually displays a rising rate power characteristic and so considering a graph that clearly displays this characteristic will help determine at what level you risk overloading the motor. Precise pump data can also identify problems that can then be directly addressed; for example, reduction in flow may indicate corrosion and scale buildup in the pump casing, or increased running clearances.
Pump maintenance needs to be regular and informed. We estimate that maintenance costs are less than 10% of a pump's lifetime cost but good maintenance can significantly improve efficiency and minimise energy expenditure.
Wear and tear is unavoidable but in pumps, where abrasive particles and poor water quality lead to erosion and corrosion, attention to the most vulnerable areas can maximise efficiency. For example, wear to the neck rings leads to an increase in clearance. This in turn causes leakage and recirculation from the high pressure area of the pump casing back to the suction side of the impeller. The result of this is reduced head and flow, which is a constant cause of poor energy efficiency if not managed correctly.
A clear action plan can help you manage these issues and enable the implementation of a scheduled maintenance regime that is suitable for the needs of your operations. To help identify some key steps in the process, we've put together the following summary of things you should consider.
Begin by estimating the energy cost of running your pumps and first focus on the equipment that uses the highest level of energy. It may be possible to retrofit energysaving features, the costs of which can soon be recovered by efficiency gains. Stage two of your action plan should be to introduce efficient condition monitoring practices, routine checking and data logging of pump performance. This should be followed by repairs and refurbishments, such as the application of wear resistant coatings, and the replacement of leaking seals.
Having attended to urgent requirements and put in place measures to monitor and maintain your pump equipment, you can then plan further ahead by spreading a basic knowledge of pumping principles and energy-saving initiatives among engineers.
Of course, a fully detailed action plan would be far more specific than the one described above but our summary illustrates the framework and key considerations of such a plan. You can either implement an action plan yourself or enlist the help of a specialist supplier such as ERIKS; the cost will be repaid through the resulting savings in energy costs and in most cases that cost is repaid swiftly. Considering that, in some applications, energy costs for pumps can actually rise to as much as 95% of the whole life cost, there are huge savings to be made through more efficient pump operation and more effective maintenance.
By following a strong action plan, you will be able to optimise your equipment and keep it optimised into the future to obtain maximum energy efficiency.
MORE FROM THIS COMPANY
- ERIKS receives 2500 applications for expanded 2024 apprenticeship programme
- Worth looking below the belt
- O-Rings: A crucial guide for the food production industry
- ERIKS launches beginners guide to MRO stores outsourcing
- Prepare for ESOS
- New drive design guide
- ERIKS launch new Automation Services Division in the UK
- New Eriks report highlights MRO supply chain challenges
- Obsolescence: Mitigating the risks
- Counting down to Maintec 2011
OTHER ARTICLES IN THIS SECTION