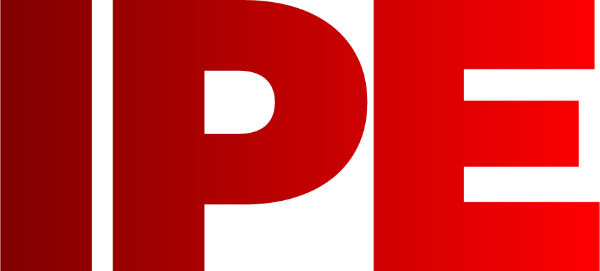
![]() |
Edward Lowton
Editor |
![]() ![]() |
Home> | Energy Management | >Compressors & ancillary equipment | >Keeping energy costs watertight |
ARTICLE
Keeping energy costs watertight
04 March 2013
Less than six months after installing a new L75RS regulated speed compressor with heat recovery from CompAir, Leeds-based Just Trays, a manufacturer of shower trays, is on target to achieve annual energy savings in the region of £23,000, with a fast payback on investment.
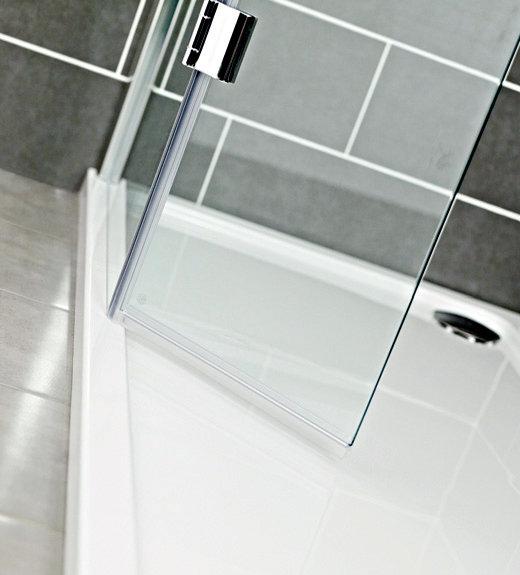
Less than six months after installing
a new L75RS regulated speed
compressor with heat recovery from
CompAir, Leeds-based Just Trays, a
manufacturer of shower trays, is on
target to achieve annual energy
savings in the region of £23,000, with
a fast payback on investment.
Ricky Dumbleton, senior production manager, says: "Based on the results of a week-long air audit, we asked a number of compressed air suppliers to put forward their recommendations. CompAir identified that, by installing a new, lubricated screw L75RS regulated speed compressor, as well as a heat recovery system, we could benefit from considerable energy savings.
"Working 10h/day, 4 days/week, the regulated speed technology in the L75RS produces the correct amount of air to match fluctuating requirements and a peak demand of about 12.5m3/min, so the compressor always runs at optimum efficiency.
This is set to provide cost savings in the region of £15,000 per annum." Just Trays' vacuum forming process needed four 9kW heat exchangers to achieve water temperature to 90°C. The heat recovery system installed by CompAir enables the water feed to be preheated, so now just one heat exchanger is required, saving a further £7000 per annum.
Ricky Dumbleton, senior production manager, says: "Based on the results of a week-long air audit, we asked a number of compressed air suppliers to put forward their recommendations. CompAir identified that, by installing a new, lubricated screw L75RS regulated speed compressor, as well as a heat recovery system, we could benefit from considerable energy savings.
"Working 10h/day, 4 days/week, the regulated speed technology in the L75RS produces the correct amount of air to match fluctuating requirements and a peak demand of about 12.5m3/min, so the compressor always runs at optimum efficiency.
This is set to provide cost savings in the region of £15,000 per annum." Just Trays' vacuum forming process needed four 9kW heat exchangers to achieve water temperature to 90°C. The heat recovery system installed by CompAir enables the water feed to be preheated, so now just one heat exchanger is required, saving a further £7000 per annum.
MORE FROM THIS COMPANY
- More sizes join compressor range
- Keeping the beer flowing
- Energy advice
- Air audit system
- Jaguar quickly claws back co
- New compressors and four stands
- Mitigating compressed air risk with oil-free technologies
- Spare parts – genuine concern
- Offering free energy advice
- Gardner Denver (CompAir) at Air-Tech 2012
OTHER ARTICLES IN THIS SECTION