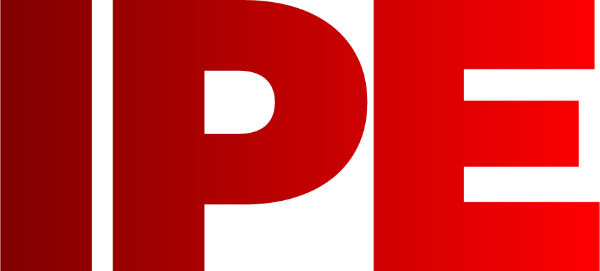
![]() |
Edward Lowton
Editor |
![]() ![]() |
Home> | Energy Management | >HVAC | >Condensing the cost of heating |
ARTICLE
Condensing the cost of heating
04 March 2013
Efficiently heating a large space such as a factory, warehouse or workshop brings a number of challenges; many such spaces make use of warm air space heaters as the preferred heating technology.
Efficiently heating a large space such
as a factory, warehouse or workshop
brings a number of challenges; many
such spaces make use of warm air space
heaters as the preferred heating technology.
As with other buildings, these heaters need to comply with the minimum net efficiency stipulated by the Building Regulations. The current requirement is for a minimum net efficiency of 91% and in most cases this can be achieved with non-condensing warm air space heaters.
Looking ahead though, the next edition of the Building Regulations has already passed through the consultation phase and is due to come into force later this year. While we don't know the exact details yet it is clear that higher efficiencies will be required for warm air space heaters within the next two to three years. It seems likely that this will match the 101% net efficiency that is already required for inclusion in the Energy Technology List to qualify for Enhanced Capital Allowances. I believe that meeting this will require the use of condensing technology.
In fact, condensing warm air space heaters are not new to the market and as a company that manufactures both types we don't have a particular axe to grind.
However, it has been estimated that around 18% of the world's CO2 emissions arise from non-condensing boilers and heaters, so a move to higher efficiencies would certainly be welcome from an environmental point of view. There are also significant cost benefits for building operators.
Condensing warm air space heaters can be operated on natural gas or liquefied propane gas (LPG) and are equipped with a secondary internal heat exchanger. This extracts residual heat from the flue gases and transfers it into the warm air stream for heating the space. The result is that the unit's heat output is increased without the use of additional fuel.
Clearly inclusion of a secondary heat exchanger results in a slightly higher cost for condensing units, compared to noncondensing units, but this is more than compensated for by the reduced energy consumption.
As this residual heat is recovered the temperature of the flue gases is reduced and this results in condensation, just as with condensing boilers, so provision needs to be made for safe disposal of the condensate via a drain point, The volumes involved are quite low, with typical condensate production rates of 0.06L/kWh for natural gas and 0.03L/kWh for LPG.
In new installations a condensate removal system can be designed-in from the start and will have a very small impact on installation costs. Where non-condensing units are being replaced with condensing heaters, provision of pipework to carry condensate away may be more complex and cost a little more.
Nevertheless there are still cost benefits that outweigh higher capital and installation costs. This can be illustrated by considering the running costs for a 140kW output gasfired warm air space heater operating for 10 hours per day, 5.5 days per week during a typical heating season (prices based on commercial gas tariffs, August 2012), as shown in table one.
It is also important to take installation costs into account and these will vary considerably from one site to another. For the purposes of this illustration, though, we can consider a modern well insulated building of, say, 2500m2 floor area and a volume of 13,500m3 requiring the above 140kW heater. Typical end user customer installed prices would be as shown in table two.
The cost difference of £1400 could therefore potentially be recovered in less than two years when compared to a noncondensing heater with minimum efficiency levels. Given that warm air space heaters should give at least a 10 year life - and many of ours have lasted much longer - the potential life cycle cost savings should be attractive to any building operator.
As with other buildings, these heaters need to comply with the minimum net efficiency stipulated by the Building Regulations. The current requirement is for a minimum net efficiency of 91% and in most cases this can be achieved with non-condensing warm air space heaters.
Looking ahead though, the next edition of the Building Regulations has already passed through the consultation phase and is due to come into force later this year. While we don't know the exact details yet it is clear that higher efficiencies will be required for warm air space heaters within the next two to three years. It seems likely that this will match the 101% net efficiency that is already required for inclusion in the Energy Technology List to qualify for Enhanced Capital Allowances. I believe that meeting this will require the use of condensing technology.
In fact, condensing warm air space heaters are not new to the market and as a company that manufactures both types we don't have a particular axe to grind.
However, it has been estimated that around 18% of the world's CO2 emissions arise from non-condensing boilers and heaters, so a move to higher efficiencies would certainly be welcome from an environmental point of view. There are also significant cost benefits for building operators.
Condensing warm air space heaters can be operated on natural gas or liquefied propane gas (LPG) and are equipped with a secondary internal heat exchanger. This extracts residual heat from the flue gases and transfers it into the warm air stream for heating the space. The result is that the unit's heat output is increased without the use of additional fuel.
Clearly inclusion of a secondary heat exchanger results in a slightly higher cost for condensing units, compared to noncondensing units, but this is more than compensated for by the reduced energy consumption.
As this residual heat is recovered the temperature of the flue gases is reduced and this results in condensation, just as with condensing boilers, so provision needs to be made for safe disposal of the condensate via a drain point, The volumes involved are quite low, with typical condensate production rates of 0.06L/kWh for natural gas and 0.03L/kWh for LPG.
In new installations a condensate removal system can be designed-in from the start and will have a very small impact on installation costs. Where non-condensing units are being replaced with condensing heaters, provision of pipework to carry condensate away may be more complex and cost a little more.
Nevertheless there are still cost benefits that outweigh higher capital and installation costs. This can be illustrated by considering the running costs for a 140kW output gasfired warm air space heater operating for 10 hours per day, 5.5 days per week during a typical heating season (prices based on commercial gas tariffs, August 2012), as shown in table one.
It is also important to take installation costs into account and these will vary considerably from one site to another. For the purposes of this illustration, though, we can consider a modern well insulated building of, say, 2500m2 floor area and a volume of 13,500m3 requiring the above 140kW heater. Typical end user customer installed prices would be as shown in table two.
The cost difference of £1400 could therefore potentially be recovered in less than two years when compared to a noncondensing heater with minimum efficiency levels. Given that warm air space heaters should give at least a 10 year life - and many of ours have lasted much longer - the potential life cycle cost savings should be attractive to any building operator.
MORE FROM THIS COMPANY
OTHER ARTICLES IN THIS SECTION