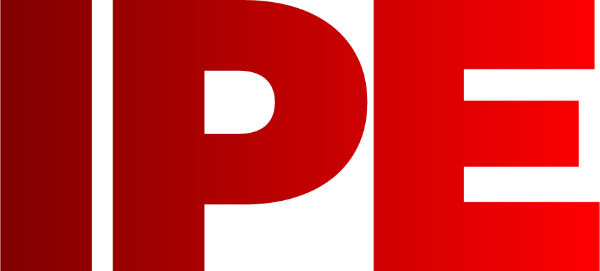
![]() |
Edward Lowton
Editor |
![]() ![]() |
Home> | Energy Management | >HVAC | >Chiller challenge |
ARTICLE
Chiller challenge
25 January 2013
Replacing an old chiller with a new one is a simple way to cut energy use and carbon.However, as Steve Warnock MD of Coolmation explains, there are many factors to consider With recent technology developments and impr
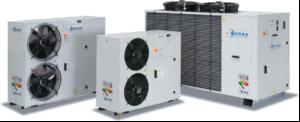
Replacing an old chiller with a new one is a simple way to
cut energy use and carbon.However, as Steve Warnock MD of
Coolmation explains, there are many factors to consider
With recent technology developments and improvements in chiller design and performance, replacing old chillers with new, high efficiency ones brings real cost benefits to the industrial sector.
Selecting the most energy efficient chiller is not simple, and there is no one solution that suits all. It is necessary to consider each chiller's EER (Energy Efficiency Ratio), the ratio of cooling output compared to power input. Eurovent, the European Committee of Air Handling and Refrigeration Equipment Manufacturers, has set its own formulae to calculate EERs, making it easier to compare the performance of chillers made by Euroventaccredited companies. Its classification for full load EER follows a similar path to the A to G approach to the Energy Labelling Directive, with the energy efficiency of chillers designated by Eurovent A or Eurovent B in catalogues and the Eurovent Directory of Certified products.
Yet, a chiller's EER should not be considered in isolation. Reference to the chiller's ESEER (European Seasonal Energy Efficiency Ratio), as set out by Eurovent, will allow clients to compare the efficiency of one chiller against another under part load conditions, giving a more realistic view of the chiller's life-cycle performance.
Since the compressor is the largest energy consumer within any chiller, the choice of scroll, screw or Turbocor centrifugal unit is a key factor in defining the EER and ESEER. Chillers with the latest oil-free Turbocor centrifugal compressors, with inverter-driven, permanent magnet motor and magnetic bearings, have grabbed the headlines. Typically, traditional induction motors of this size are in the 92% efficiency range; the Turbocor compressor's permanent magnet DC motor provides an efficiency of between 96 to 97%. Yet, they are not necessarily the best option for all applications. For tasks requiring cooling capacities to 350-400kW, chillers with four or six independently operating scroll compressors are still likely to be the most efficient selection.Matching a reducing load simply means turning compressors off, more efficient than allowing compressors to continue to run in an unloaded state.
The efficiency of the Coolmation range of multi scroll chillers has been enhanced by a predictive control system, which can reduce energy consumption by as much as 18% where temperature stability is not so critical.
Traditionally, control logics on water chillers and heat pumps ignore cooling load dynamics; instead they regulate according to return water temperature to maintain steady operation. However, a new predictive control system, Adaptive Function Plus, (developed by Rhoss Spa and available from Coolmation in the UK) is different since it objectively optimises the chiller's operation through information gathered from the load profile, then regulates delivery water temperature according to load demands. A special adaptive algorithm and mathematical formulae is used to vary these values by managing the operation of each individual compressor.
Rarely do chillers operate at full load throughout the year in industrial plants, and part-load operation has a noticeable effect on seasonal energy performance and power consumption. These are precisely the conditions where efficiency savings can be made through predictive control logic. A predictive control ensures the highest possible water leaving temperature is delivered while still maintaining user conditions. This can result in an 18% energy reduction and proportionate reductions in carbon footprint.
By using a predictive control it is possible to achieve equal to or better performance results than Class A chiller performance, as defined by Eurovent, making it possible to obtain an affordable, highly efficient chiller.
For applications where temperature stability is essential to product quality, the AFP can run on an alternative 'precision setting, making it possible to guarantee an average fluctuation from the water supply temperature of about ± 1.5°C from the set point value, compared to an average fluctuation over time of ± 3°C with a standard control.
Another feature of predictive control systems is the 'Virtual Tank' function which allows multi scroll chillers to operate with less water volume per kW of cooling/heating capacity. The control compensates by muffling the control signal when source temperature is reached, preventing the compressor from switching on and off abruptly, saving energy and reducing the average fluctuation of the set-point value. Lower water content means that, if required, a smaller buffer tank can be installed, saving installation time, glycol and water treatment costs.
Returning to chiller types, where demand exceeds 500kW, the choice is probably between a Turbocor or screw compressor chiller.Where load conditions are going to be constantly above 70%, it is probable that a screw compressor chiller will be as efficient as a Turbocor one, and less expensive.Where loads are likely to reduce for considerable periods to around 50%, Turbocor chillers will be more efficient than screw.
Another way to cut a chiller's operating cost and its carbon footprint is to install a free cooling chiller. This takes advantage of low ambient temperatures to pre-cool the water returning to the chiller, reducing the load on the compressors and the energy consumed.When ambient temperature falls 1°C below the temperature of the water returning to the chiller, free cooling can be activated. Free cooling is effective in the UK where ambient temperature is below 15°C for almost 75% of the year. Typically, with an ambient temperature between 3 and 5°C below set point temperature, compressors will switch off and the only energy consumed will be by the small fans on the free cooler.
To maximise either chiller efficiency or temperature stability Rhoss' AFP control can now be combined with free cooling chillers.
Plant engineers must be given the chance to select the most efficient chillers to meet their requirements, while demonstrating their financial benefits to finance directors.
With recent technology developments and improvements in chiller design and performance, replacing old chillers with new, high efficiency ones brings real cost benefits to the industrial sector.
Selecting the most energy efficient chiller is not simple, and there is no one solution that suits all. It is necessary to consider each chiller's EER (Energy Efficiency Ratio), the ratio of cooling output compared to power input. Eurovent, the European Committee of Air Handling and Refrigeration Equipment Manufacturers, has set its own formulae to calculate EERs, making it easier to compare the performance of chillers made by Euroventaccredited companies. Its classification for full load EER follows a similar path to the A to G approach to the Energy Labelling Directive, with the energy efficiency of chillers designated by Eurovent A or Eurovent B in catalogues and the Eurovent Directory of Certified products.
Yet, a chiller's EER should not be considered in isolation. Reference to the chiller's ESEER (European Seasonal Energy Efficiency Ratio), as set out by Eurovent, will allow clients to compare the efficiency of one chiller against another under part load conditions, giving a more realistic view of the chiller's life-cycle performance.
Since the compressor is the largest energy consumer within any chiller, the choice of scroll, screw or Turbocor centrifugal unit is a key factor in defining the EER and ESEER. Chillers with the latest oil-free Turbocor centrifugal compressors, with inverter-driven, permanent magnet motor and magnetic bearings, have grabbed the headlines. Typically, traditional induction motors of this size are in the 92% efficiency range; the Turbocor compressor's permanent magnet DC motor provides an efficiency of between 96 to 97%. Yet, they are not necessarily the best option for all applications. For tasks requiring cooling capacities to 350-400kW, chillers with four or six independently operating scroll compressors are still likely to be the most efficient selection.Matching a reducing load simply means turning compressors off, more efficient than allowing compressors to continue to run in an unloaded state.
The efficiency of the Coolmation range of multi scroll chillers has been enhanced by a predictive control system, which can reduce energy consumption by as much as 18% where temperature stability is not so critical.
Traditionally, control logics on water chillers and heat pumps ignore cooling load dynamics; instead they regulate according to return water temperature to maintain steady operation. However, a new predictive control system, Adaptive Function Plus, (developed by Rhoss Spa and available from Coolmation in the UK) is different since it objectively optimises the chiller's operation through information gathered from the load profile, then regulates delivery water temperature according to load demands. A special adaptive algorithm and mathematical formulae is used to vary these values by managing the operation of each individual compressor.
Rarely do chillers operate at full load throughout the year in industrial plants, and part-load operation has a noticeable effect on seasonal energy performance and power consumption. These are precisely the conditions where efficiency savings can be made through predictive control logic. A predictive control ensures the highest possible water leaving temperature is delivered while still maintaining user conditions. This can result in an 18% energy reduction and proportionate reductions in carbon footprint.
By using a predictive control it is possible to achieve equal to or better performance results than Class A chiller performance, as defined by Eurovent, making it possible to obtain an affordable, highly efficient chiller.
For applications where temperature stability is essential to product quality, the AFP can run on an alternative 'precision setting, making it possible to guarantee an average fluctuation from the water supply temperature of about ± 1.5°C from the set point value, compared to an average fluctuation over time of ± 3°C with a standard control.
Another feature of predictive control systems is the 'Virtual Tank' function which allows multi scroll chillers to operate with less water volume per kW of cooling/heating capacity. The control compensates by muffling the control signal when source temperature is reached, preventing the compressor from switching on and off abruptly, saving energy and reducing the average fluctuation of the set-point value. Lower water content means that, if required, a smaller buffer tank can be installed, saving installation time, glycol and water treatment costs.
Returning to chiller types, where demand exceeds 500kW, the choice is probably between a Turbocor or screw compressor chiller.Where load conditions are going to be constantly above 70%, it is probable that a screw compressor chiller will be as efficient as a Turbocor one, and less expensive.Where loads are likely to reduce for considerable periods to around 50%, Turbocor chillers will be more efficient than screw.
Another way to cut a chiller's operating cost and its carbon footprint is to install a free cooling chiller. This takes advantage of low ambient temperatures to pre-cool the water returning to the chiller, reducing the load on the compressors and the energy consumed.When ambient temperature falls 1°C below the temperature of the water returning to the chiller, free cooling can be activated. Free cooling is effective in the UK where ambient temperature is below 15°C for almost 75% of the year. Typically, with an ambient temperature between 3 and 5°C below set point temperature, compressors will switch off and the only energy consumed will be by the small fans on the free cooler.
To maximise either chiller efficiency or temperature stability Rhoss' AFP control can now be combined with free cooling chillers.
Plant engineers must be given the chance to select the most efficient chillers to meet their requirements, while demonstrating their financial benefits to finance directors.
MORE FROM THIS COMPANY
OTHER ARTICLES IN THIS SECTION