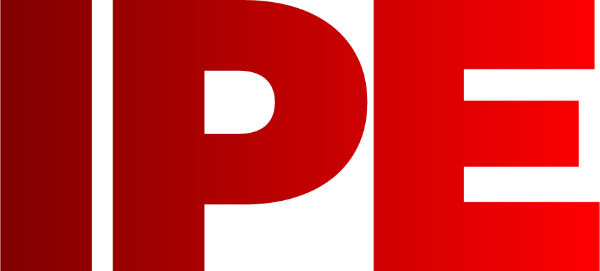
![]() |
Edward Lowton
Editor |
![]() ![]() |
Home> | Handbooks | >AirUser | >Efficient compressed air generation – and heat for free |
Home> | Energy Management | >Compressors & ancillary equipment | >Efficient compressed air generation – and heat for free |
Home> | Plant, Process & Control | >Compressors and ancillary equipment | >Efficient compressed air generation – and heat for free |
Efficient compressed air generation – and heat for free
19 July 2013
When compressed air is generated, heat is inevitably produced as a by-product. Anyone looking to enhance efficiency can use this heat and increase the efficiency of compressors to about 95% as a result. To achieve this, there are easy-fit heat exchangers which can even be fitted to existing stations. This investment often pays for itself within less than a year. Mark Whitmore, general manager at BOGE Compressors, explains
The issue of heat recovery in compressed air circles is not always tackled head on. This may be explained by the fact that manufacturers of compressed air compressors and suppliers of complete compressed air stations first of all need to look a rather unpleasant truth in the face before they can instil in users an awareness of this extremely efficient type of combined energy use: Whatever way you look at it, generating compressed air as a utility is not actually very efficient.
This property of compressed air is shared with many other energy conversion processes. A coal-fired power station achieves an efficiency of about 45%. A wind generator, working at 50%, is not much more efficient, although this is not really an issue being a renewable source of energy.
Compressed air plus thermal energy - a highly efficient combination
Similarly to coal-fired power stations, around 94% of the energy during compressed air generation is converted to heat (fig. 1). This often dissipates before it can be used - a considerable failure where energy efficiency is concerned. If the heat is used for the production process, or to heat the premises, it is possible to achieve impressive efficiencies of well over 90%.
In fact, of the 100% of the electrical energy consumed, some 94% is converted to heat, that can be put to good use after it has been recovered.
This does not actually make compressed air cheaper per cubic metre, but the operator can make considerable savings in other respects, such as the cost of heating premises or water.
Choosing the right process
It is a useful exercise at the outset to take a good look at the process parameters, and to select the process which is likely to benefit most from using the heat produced by the compressor. Many chemical and foodstuff producers are at an advantage in this respect, since they use temperature controlled processes and therefore have a year-round demand for heat. Paint shops and electroplating operations also need a constant supply of heat for their processes. In plants that do not require process heat, the user has the choice between either heating premises or hot water heating.
Compressors as energy savers
Modern water-cooled compressors are already well-prepared for easily integrating a heat recovery system into the cooling circuit. There are a lot of much older compressor stations, though, that work without heat recovery. For stations such as these, Boge has a new Duotherm system, which can be used with existing BOGE systems as well as with other-brand systems. This makes the compressor into an 'energy saver' with a surge in overall efficiency, no matter what the original model or output was.
This system is available in five power levels from 7.5 to 110 kW, for easy integration into oil-injection cooled screw compressors. The generously dimensioned heat exchanger in the Duotherm system is connected to the oil system of both the compressor and the hot water or process water utility mains. It efficiently transfers the heat from compressed air production to the desired process - without any additional energy input. Thanks to the compact design, the system requires very little space to achieve a lasting improvement in the energy efficiency of the compressor.
Quickly pays for itself
The investment costs for heat recovery systems depend largely on the structural conditions at the site of use. These conditions need to be taken into account, since they have a considerable influence on the amortisation time. In Boge's experience so far, investments in a heat recovery system pay for themselves within six months to 12 years; frequently, this occurs within less than 12 months.
At its own premises, Boge relies on a combined model of thermal use: In winter, and in the transition periods between the seasons, the compressor heat is used for heating purposes, while in summer, it is used to heat hot water. This saves the company around 100,000kWh of heating power per year.
Simple equation
Users considering buying a heat recovery system may like to consider the following: The Boge S 100-2 type compressor in the 75kW class produces a usable heat of 60.6kW. In single shift operation over 2000 compressor operating hours, and with a heating oil price of €0.80, this equates to a savings potential of €14,046 by using Boge Duotherm. Constantly increasing energy prices make the procurement of a system such as this even more worthwhile.
Air-cooled systems
Air-cooled systems can use the exhaust air to heat rooms or production facilities. This can also be easily achieved using the outdoor thermostat control. In this case, from a defined temperature upwards, the exhaust air stream from the sound insulation hood is switched over to heat the production facility when temperatures drop - and all this at no extra cost.
In view of the low investment, compressed air users should seriously consider the option of utilising waste heat. This is particularly true for the smaller type of compressor station: Even waste heat from an 18.5kW compressor provides enough to heat a domestic dwelling.
It is also a good idea to look into the fine tuning of other factors involved in the efficiency of compressed air supply. These include recommendations such as checking the pressure level, optimising the regulation with as low a pressure range as possible, the use of variable speed compressors for peak loads, and reducing inefficient idle times. It is also advisable to set up regular leak testing, which can be achieved electronically by modern control systems, through measuring the drop in pressure when the compressors are switched off. Boge supplies a tool for this purpose - the Leakage Monitor.
- Oil-free piston range
- Five simple steps to maximising energy efficiency
- White paper for F&B manufacturers
- Turning heat into energy
- Savvy solutions to energy issues
- Kitchen maker finds recipe for savings
- Remote control of compressors
- Air compression: Looking to the future
- Sound advice on controlling noise
- Oil-free compressors