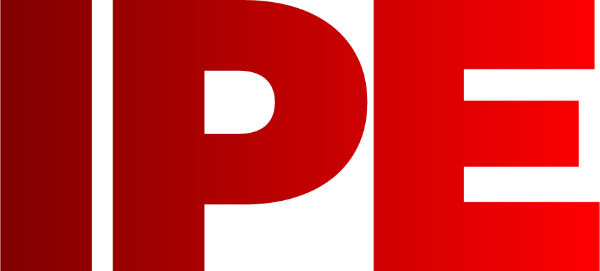
![]() |
Edward Lowton
Editor |
![]() ![]() |
Home> | Plant, Process & Control | >Motors and drives | >Latest drives boost process efficiency |
Home> | Energy Management | >Motors and drives | >Latest drives boost process efficiency |
Latest drives boost process efficiency
24 July 2013
Are you getting the best from your drives? Replacing them with more modern products that offer better efficiency and more capable software could transform your process and save even more energy, as Neil Ritchie, local business unit manager, drives & controls, ABB explains explains
Few technologies stand still and that is definitely true of variable-speed drives (VSDs). Today’s examples are a world away from their forebears in terms of efficiency and capability. The early drives of the 1980s had a typical efficiency of about 80%, while today’s drives are often in excess of 90%.
With some 40% of new drives bought as replacements for VSDs bought within the past 25 years, some companies are obviously looking at their existing drives and wondering if they could do better.
As well as improved efficiency, older drives will not have the latest energy saving features such as flux optimisation, a software algorithm which can save up to 10% more energy in pump and fan applications.
The effectiveness and efficiency of the process is another aspect and modern drives can be updated by software, often remotely over the internet, to add features that can save operational or maintenance costs.
Get the right drive
When assessing an application for drive replacement, treat the application as a new installation and take account of the present torque requirement of the load. Parameters may have changed over the years and the conditions that dictated the original sizing of the drive may no longer be valid.
Also, in the past, drives were often 10% oversized compared to what would be the norm today.
Reputable drives manufacturers will have well-established processes to help users choose the best drive for their application. This may involve engineers from the drive vendor visiting the site to conduct an energy appraisal, to ensure the best new replacement drive is selected for an application.
Matching air extraction to demand
An example of what can be achieved is at Tata Steel’s Aldwarke Bloom Caster complex in Rotherham, South Yorkshire which is saving £250,000 a year following the installation of ABB VSDs on its fume extraction system.
The extraction plant is used to remove fumes produced by the two casting machines and two ladle arc furnaces.
The original installation used four 3.3kV motors, two 650kW and two 410kW. The two large motors were used as the primary extraction motors, with the smaller motors used to provide additional extraction as required. Due to motor limitations the fans were restricted to four starts per hour, as additional starts would risk damaging the windings. These starting restrictions forced the motors to run-on for 15 minutes after receiving the stop signal, even if demand for extraction was reduced. This obviously wasted a lot of energy.
The motors were replaced with low voltage motors, controlled by four ABB low harmonic variable-speed drives, two at 400kW and two at 570kW.
As well as the large amount of energy saved by more closely matching the speed of the motors to the dust extraction demand, using VSDs also cuts maintenance by reducing wear and tear on the motors and strain on the duct work, as well as making for a less noisy environment.
Cutting the waste
Another example is TI Automotive, a manufacturer of plastic automotive fuel tanks, which is saving £24,000 a year on its energy bill following the installation of ABB variable-speed drives.
Two applications – the air compressor and the chilled water pumps – were identified as being particularly energy intensive.
With its production based on blow moulding, the plant uses a large amount of compressed air. A 75kW ABB standard drive was fitted on the air compressor, which had previously been a fixed speed unit. Running the motor at half speed, the ABB standard drive reduced consumption from 75kW to 45kW, giving a saving of around 35%.
Using 11kW ABB standard drives on the three chilled pumps produced a 30% saving, cutting power demand from 11kW to 7kW.
With increased energy saving potential and improved control features compared to older versions, modern VSDs can offer a significant improvement in the operation of pump and fan driven applications. It could be high time to take a long hard look at your own drives and see what improvements you could make.
- Team effort
- Energy projects net an award
- Steel maker set to save £68,000 on energy costs
- Award-winning
- Three in a row
- ABB integrates drive safety functionality to simplify machine automation
- Driving down costs
- Diagnostics service for drives
- ABB at IWEX exhibition
- Shielded motor helps prevent overheating