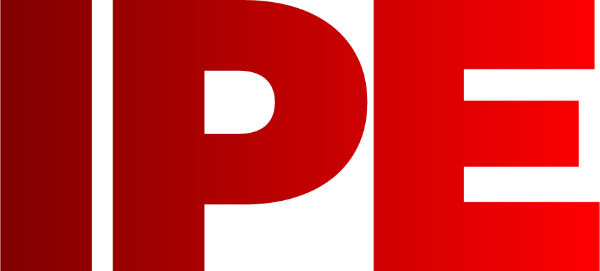
![]() |
Edward Lowton
Editor |
![]() ![]() |
Home> | Plant, Process & Control | >Process equipment | >Firmware option reduces programming |
Firmware option reduces programming
14 October 2013
When bespoke machinery design and build company, Jim O'Neill Engineering, developed a coating line for a transfer printing operation the company called upon the control systems expertise of Mitsubishi Electric.
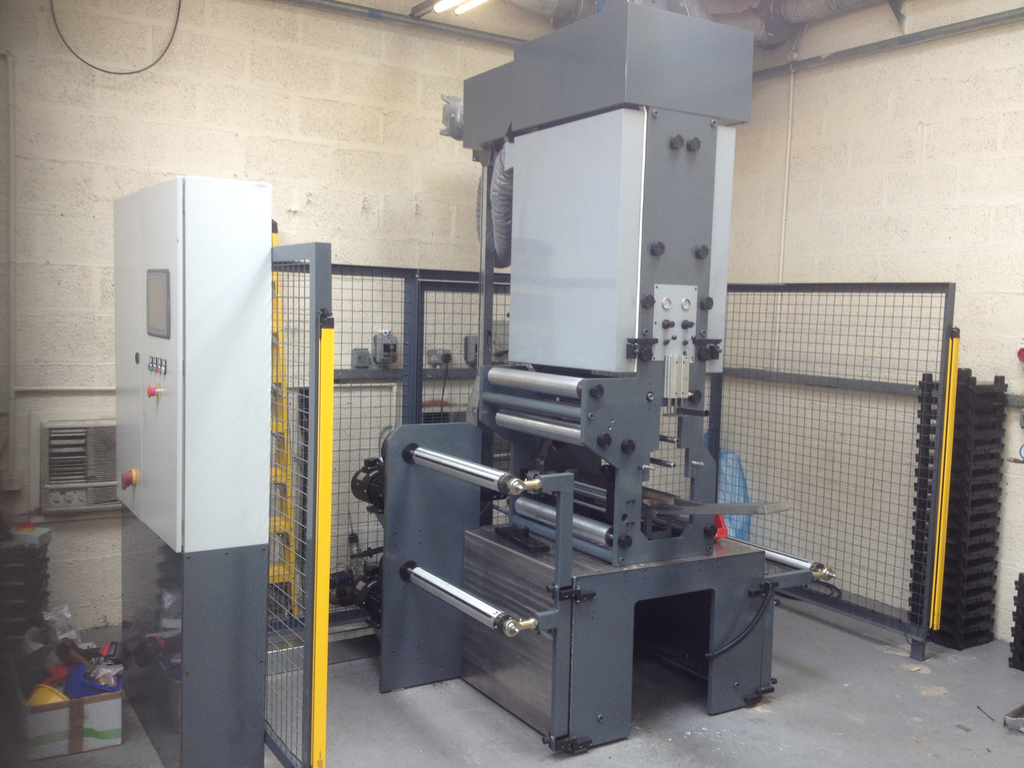
In this case Mitsubishi made use of a firmware option to customise its standard FR-A700 drives for the job in hand. Previously programming this functionality into a PLC or selecting a high cost systems drive would have been necessary, resulting in extra programming time and expense. The winder functionality in the FR-A700-A1 requires simple parameter settings only.
The solution devised uses four motors: a rewind motor, an unwind motor, auxiliary station and a master motor running in speed control. The rewind and auxillary station Inverters are connected to the three-phase 400V power supply, while the other two Inverters are connected to the DC Bus of each of these Inverters. This allows the continuous regenerative energy from the unwind sections to be used in the motoring inverters. It also means the regenerated energy can be recovered, reducing energy costs.
- Waterworks modernisation
- First steps on the road to digitalisation
- The right solution for almost any application
- More than speed & torque control...
- What will the SME manufacturing landscape look like post COVID-19?
- Energy from waste
- Comes in handy for energy savings
- Condition monitoring keeps paper plant running
- Integrated display
- Second day added to 'Future Manufacturing Event'