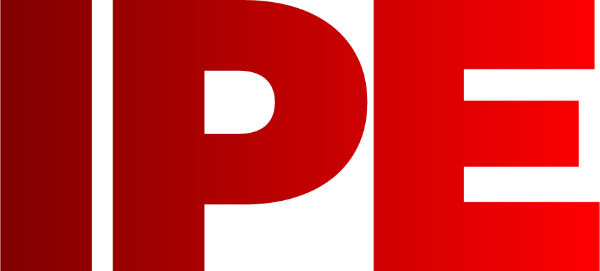
![]() |
Edward Lowton
Editor |
![]() ![]() |
Home> | Energy Management | >CHP | >CHP: Responsible approach needed |
CHP: Responsible approach needed
10 March 2014
As the use of Combined Heat and Power (CHP) technology has grown in the UK, lessons have been learnt around the ways in which a system should be designed to maximise performance. Here, Pete Mills, commercial technical operations manager at Bosch Commercial and Industrial Heating, argues that there remains a need for system designers to take a more responsible approach
Small scale CHP projects represent the bulk of the sector where facilities such as production, hospitals, nursing homes, hotels and leisure facilities can take advantage of the significant CO2 and energy savings. Wherever there is high energy use with significant base loads for heat and power, CHP should always be a consideration in the design appraisal.
System designers face many decisions at the start of a project and CHP modules have the capability to be heat-led or electrically-led in operation. Most modern systems are heat-led, since this maximises the efficient use of a CHP module where the waste heat from generating electricity can be put to good use. In certain applications however, there are good reasons for having an electrically-led or electrically biased operation; for example when standby operation is required for important but non-emergency loads during power outages.
Compromised efficiency
In spite of design best practice, there is now evidence of many schemes where it was decided upon to make the system purely electrically led, based on financial reasons alone, rather than from the point of view of maximising efficiency. On such schemes, heat is routinely rejected or dumped through dry air coolers to the atmosphere. I believe it is high time that the rejection of heat is seen as a last resort.
The sheer nature of a CHP system means that even schemes which set out to reject a minimal amount of heat can find themselves rejecting more heat than required. Many opt for a system where the amount of heat rejected is controlled by a three way valve and control system, which in principle should be fine, however in practice, the reaction speed of the valve and overall control can lead to useful heat being lost to the atmosphere; thus reducing efficiency, CO2 savings and financial savings. Furthermore, frost protection is required to protect the dry air cooler, and if there is no hydraulic separation using glycol, immersion heaters often have to be relied upon. Immersion heaters are not always able to provide adequate protection and as seen in the recent extreme low ambient temperatures experienced in UK winters, have resulted in damage to the coils, and system water loss, which leads to costly repairs.
Whilst rejecting heat may be seen as the most financially viable option in some cases, many within the industry believe this type of standard heat rejection is no longer acceptable.
Reap the rewards
The Quality Assurance scheme for Combined Heat and Power (CHPQA) recognises the environmental and security benefits of well-designed and operated CHP schemes. Although a voluntary scheme, it offers many benefits and provides a route for further savings from Climate Change Levy (CCL) exemption, access to Enhanced Capital Allowances (ECA), and exemption of plant and machinery from business rates. For small scale schemes where no heat rejection is used, the CHPQA allows a simpler approach to monitoring the quality of the scheme by metering of the gas used and electricity produced.
CHP schemes have the potential to offer some of the most cost-effective savings of CO2 as well as helping with the security of electricity supplies, but as with all renewable and low carbon technologies, well designed, installed, and operated systems are the key to realising these savings.
- CHP: The benefits of remote monitoring
- CHP: CPD programme
- Sources of steam: Selection matters
- Commissioning: Key to peak performance
- CHP offering extended to 2MWe
- Cutting costs through heat recovery
- Energy: Don't let it go to waste
- Low carbon technologies
- Rebrand for gas-fired condensing boiler
- Chance to gain without pain
- CHP: CPD programme
- Energy: Don't let it go to waste
- Plugging potential gaps
- Carbon management
- Trial to create smarter electricity grid
- CHP: Helping cold store cut costs
- Operating new biomass CHP plant
- CHP: Efficiency right at the source
- CHP: The benefits of remote monitoring
- CHP guide for manufacturing industry