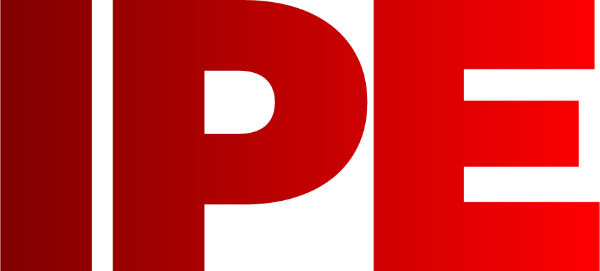
![]() |
Edward Lowton
Editor |
![]() ![]() |
Home> | Plant, Process & Control | >Boilers and burners | >Sources of steam: Selection matters |
Home> | Energy Management | >Boilers and burners | >Sources of steam: Selection matters |
Sources of steam: Selection matters
15 July 2013
With a large number of process heating applications requiring an efficient source of steam, stakeholders are often required to decide between a boiler and a generator. Rob Brown, technical manager – industrial boiler plants at Bosch Commercial and Industrial Heating, comments
The requirement for steam in industrial applications ranges greatly. From power stations through to food and drink manufacturing, the demand for steam spans both the private and public sectors. However, with energy costs at an all-time high, and industrial stakeholders having to face up to the challenge of fulfilling their need for steam without tarnishing their own environmental credentials, making the correct decision on the most suitable technology for process heating is essential.
Those requiring steam for industrial use generally have two possible options when it comes to selecting the most appropriate technology for steam generation - boilers and generators. Although steam is generated in both appliances, there are some significant differences in their construction, use and installation, so it is important not to confuse the two technologies.
Boiler v generator
In simple terms, a steam boiler consists of a pressure vessel with an integrated flame tube, reversing chambers and gas flues – all of which are surrounded by boiler water. The feed water is supplied through a water level controller which is fed by a duty/standby pump or external ring main system, independent of the heating. The steam escapes from the water level surface through a crown valve and is then transported to its relevant application.
A steam generator is a pressure system consisting of a water heating coil. The feed water is pumped through the pipe system using a piston pump, and the amount of water supplied corresponds with the steam output. Consequently, a generator is best suited to relatively small-scale applications, where the requirement for steam is for local point of use and for predetermined periods of operation. The steam volume output is adapted to the amount of water supplied. This water is completely vaporised in one full run. Only a few minutes pass between a cold start and full steam output, which is why they are also referred to as ‘rapid steam generators’.
Each of the technologies has their respective merits and strengths in terms of the types of application to which they are best suited.
Steam boilers can produce an almost unlimited amount of steam continually, which can be adjusted to meet the exact requirements levels needed for each individual application. In an environment such as a power station, the provision of steam can be distributed to multiple end-users, thanks to a boiler’s ability to supply steam on demand.
When it comes to the physical delivery of steam to its point of use, the range of boilers available means different temperature and pressure requirements can be catered for. Using a steam boiler with three pass technology, it is possible to deliver saturated steam to 235°C, at a pressure of up to 30 bar. This is suitable for the medium to high output requirements of applications such as hospitals, power stations and process facilities that require a high transfer of heat.
Bosch believes the introduction to the UK market of its range of steam boilers, which are suitable for liquid and gaseous fuels, and come equipped with flame/smoke tubes, can allow a greater recovery of heat contained in the flue gases. This can increase the energy efficiency of the boiler by up to 7% in dry running operation, and up to 15% in condensing operations. By coupling this heat recovery capability with the latest burner technology, CO2 emissions can also be kept to a minimum. For those keen to establish favourable environmental credentials meanwhile, a completely neutral CO2 level is possible through the use of bio-oils or bio-gases for steam generation.
When it comes to industrial plant applications, a heating system should always be considered in its own right, as the requirements of the building, the application, and the user will differ from case to case. That said, the steam boiler technology available to stakeholders, in the industrial sector, is capable of providing a very efficient means of meeting process heating delivery requirements.
- CHP: Responsible approach needed
- CHP: CPD programme
- CHP: The benefits of remote monitoring
- Chance to gain without pain
- Low carbon technologies
- Cutting costs through heat recovery
- CHP offering extended to 2MWe
- Energy: Don't let it go to waste
- Rebrand for gas-fired condensing boiler
- Steam: An ongoing demand