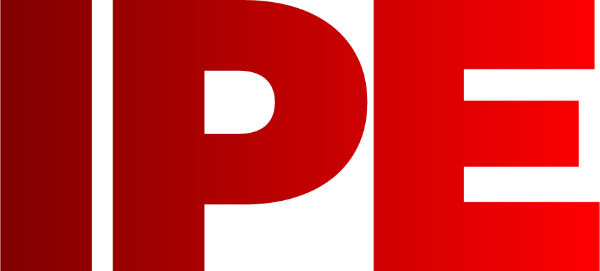
![]() |
Edward Lowton
Editor |
![]() ![]() |
Home> | Energy Management | >Boilers and burners | >Energy: Don't let it go to waste |
Home> | Energy Management | >CHP | >Energy: Don't let it go to waste |
Home> | Plant, Process & Control | >Process heating | >Energy: Don't let it go to waste |
Energy: Don't let it go to waste
01 July 2014
With energy conservation an increasingly hot topic within the process heating industry, stakeholders are now looking towards innovative methods to reduce energy consumption. Simon Tarr at Bosch Commercial and Industrial Heating, explains how a combination of technologies can be used to accompany a steam boiler to maximise energy efficiency
Increasingly, industrial energy users are looking to maximise energy efficiency and minimise production costs and overheads. Add to that the increasing requirement for businesses to meet strict energy targets and there is a real case for reviewing energy use in order to determine where improvements can be made.
On an industrial and commercial scale, there is arguably no better place to start improving efficiencies and running costs than by taking a fresh look at the technologies available in the marketplace and how these can be used to maximise energy efficiency.
Whilst much can be done by installing modern heating and hot water technologies to reduce energy use and lower costs, a case can be made for the combination of certain technologies to further enhance efficiency. For example, integrating a Combined Heat and Power module (CHP) with a steam boiler is an innovative way of using the CHP system’s waste exhaust gas to create a unique arrangement which helps to increase steam generation efficiency levels.
Steam and CHP
Steam is one of the most widely used commodities for transferring heat energy. Its use is popular throughout industry for a broad range of tasks – mechanical power production, space heating, and other process applications. One of the most common methods of steam generation is the use of a steam boiler, which operates using three pass technology.
The steam generated should be available at the client’s point of use in the correct quantity, at the correct pressure, clean, dry and free from air and other incondensable gases. In an industrial steam heating system, the purpose of the generation and distribution of steam is to provide heat at the process heat transfer surface - this could be using a heat exchanger.
To enhance boiler efficiency, additional heat can be transferred into the steam boiler via the waste exhaust gas from a CHP unit. A CHP module offers an efficient way to generate heat and electrical power simultaneously. A typical CHP module consists of a gas engine, a generator and a heat exchanger system. The gas engine drives the generator to produce three-phase electrical power, which feeds in to the main low voltage distribution system where it can be used locally.
During this process, the heat within the exhaust gases is produced as a by-product of the usable power and heat generated which, in a conventional power station, would often be wasted. However, this exhaust heat generated by a typical CHP module can be re-directed and may be used in process heating or hot water applications. Through the use of a waste gas inlet valve, this surplus heat can be transferred to a specific point of use.
By implementing an innovative fourth smoke tube pass between the CHP unit and the steam boiler, the surplus heat generated can be driven back into the steam boiler, thus maximising the energy efficiency of steam production.
System design
The production of steam was once used for space heating, yet is now generally more popular for process use. Not only is steam an excellent carrier of heat, it is also sterile, and thus commonly used in the food, pharmaceutical and health industries. It is also widely used in hospitals for sterilisation purposes.
This has meant that companies operating in this sector have generally had to address the source of electrical power and heat generation in isolation. As users of the technology will know, the installation of a steam boiler is very complex, with each steam boiler installation requiring a bespoke design. Incorporating an innovative fourth pass technology into any system design between a CHP unit and a steam boiler, can lead to considerable increases in energy efficiency in comparison to the conventional, separate electrical power and heat generation. This will also ensure reduction in CO2 and NOx emissions, providing further environmental benefits and compliance with the CRC Energy Efficiency scheme.
Simon Tarr is sales manager for industrial boilers at Bosch Commercial and Industrial Heating.
- Rebrand for gas-fired condensing boiler
- Chance to gain without pain
- Cutting costs through heat recovery
- Sources of steam: Selection matters
- CHP offering extended to 2MWe
- Low carbon technologies
- Commissioning: Key to peak performance
- CHP: Responsible approach needed
- CHP: CPD programme
- CIBSE launches new society