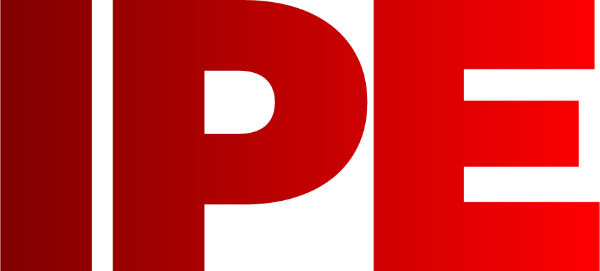
![]() |
Edward Lowton
Editor |
![]() ![]() |
Home> | Handbooks | >Manufacturing Matters Ireland | >Pump contract is in the bag |
Home> | Plant, Process & Control | >Pumps | >Pump contract is in the bag |
Pump contract is in the bag
19 December 2014
Stonehouse Paper & Bag Mills, based in Gloucestershire, UK, has installed three 500 series process pumps from Watson-Marlow Pumps Group in replacement for some diaphragm pumps that were proving hard to clean, difficult to maintain and expensive to run.
Jonathan Daniels, managing director of Stonehouse Paper & Bag Mills, says: "When we were looking for new pumps, our research revealed that electrically operated pumps would be more economic and easier to use than the air-operated diaphragm pumps with which we had become familiar. All compressed air systems have leaks, which basically means you are using energy even when the pump isn’t running. There are no such worries with an electric pump. Furthermore, changing the diaphragm and valves in an AOD pump is best done by an octopus, whereas access and tube loading on the Watson-Marlow pump couldn’t be easier.”
On the Watson-Marlow 521VI/R2C, the pumphead set-up using two-position, sprung-loaded tube clamps and clutched rotor makes tube loading effortless.
Daniels also says that the robust build of the pump helped differentiate it from others on the market. Here, heavy duty construction with impact-proof safeguarding and robust tube clamps ensure grip even in poor operating environments. Furthermore, the 520R2C pumphead features a polyphenlene sulphide (PPS) track and rotor, with stainless steel occlusion rollers to resist chemical attack and abrasive wear.
Ink circulation
The pumps at Stonehouse are used to circulate inks on the printing presses, some of which use a ‘chamber blade’ system. This, in combination with the pump, fills a pot with ink (the pot has an overflow), constantly agitating it to keep the colour consistent
"If the pump is running too fast, or the pressure is wrong, there’s a real danger that thinner inks will leak everywhere,” explains Daniels. "However, with the variable speed inverter on the Watson-Marlow 521VI/R2C, we can slow things down to negate this issue.”
In control
Daniels says that a further advantage of the Watson-Marlow pump is that it’s possible to ‘back-pump’ using reverse control to extract all of the ink from the tube and save it going all over the floor when changing over.
"In theory we could have a tube for each colour because changeover is so easy,” he says. "In reality, however, we’re running all the colours of the rainbow and every shade in between, so we have to cleandown between print runs. It’s just a case of washing through with water – using the inverter on the Watson-Marlow we can wash through at whatever speed we want.”
In contrast, Daniels says that the diaphragm pumps are hard to keep impeccably clean. They feature their own vessel into which ink is poured – this has to be poured back out at the end of the run, creating downtime.
Further orders
The three Watson-Marlow 521VI/R2C pumps have been working at Stonehouse since 2005. Such has been their performance that the company has now placed an order for two more.
Daniels concludes: "Not only have the pumps proved reliable, but Watson-Marlow are very knowledgeable and have been extremely helpful. As and when other diaphragm pumps stop being reliable we will replace them with Watson-Marlow.”