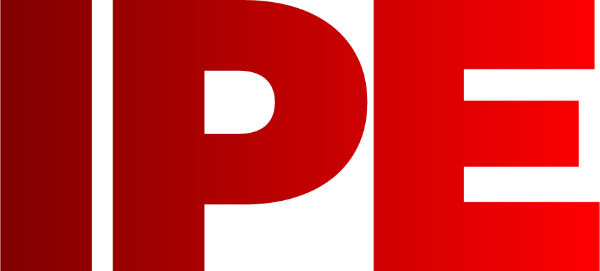
![]() |
Edward Lowton
Editor |
![]() ![]() |
Home> | Production Engineering | >Materials | >Ironing out uncertainty in stainless steel production |
Ironing out uncertainty in stainless steel production
12 May 2015
In stainless steel production, delivering the perfect specification in every batch requires advanced chemical analysis throughout the process, but taking representative samples in real time is a significant engineering challenge, as Roger Brown of Thyson Technology explains.
Stainless steel, a low-carbon, high chromium alloy of iron known for its corrosion resistance and strength, plays a crucial role in applications from micro-components to mega-structures, and more than 38 million metric tons of the material are produced worldwide every year.
A key step in its production is removing a very specific amount of carbon from the molten mixture, something that is achieved by exposing it to pure oxygen, which reacts to produce carbon dioxide and carbon monoxide gases.
The process – Vacuum Oxygen Decarburization (VOD) – must be highly controlled and takes place in a closed vessel under a vacuum. To achieve the correct proportions of elements in the final steel mixture, the timing of this process is critical. End it too soon and too much carbon will remain, resulting in a harder, more brittle material; leave it running too long and too much carbon will be removed and other important metals in the mixture, like chromium, will begin to oxidise.
Getting this wrong is costly. It will often mean the batch has to be re-blown – a wasteful, expensive and time-consuming process.
Removing trial and error
A large vessel of molten steel is transported into an air-tight chamber, where the pressure is lowered to less than 250mbar – close to a vacuum. Specially designed vents in the bottom of the vessel then allow argon – a non-reactive gas – to enter the mixture, simply to keep it circulating within the vessel. A water-cooled lance is used to blow pure oxygen over the surface of the mixture.
In the early days of stainless steel production, this was largely a process of trial and error, and it was only in the 1980s that an effective means of monitoring the composition of the mixture while the process was taking place was developed – by analysing the composition of the gases emitted by the process.
Comparing the makeup of these effluent gases, and specifically the relationship of carbon monoxide and carbon dioxide given off, against a known model allows operators to determine the exact point at which to end the decarburisation process.
This is achieved by analysing the gases with a mass spectrometer, which measures the relative abundance of different compounds in a mixture. As the process progresses, the proportions of different compounds coming off the mixture changes, with the most readily-oxidised substances being removed first. Silicone has a higher affinity to oxygen than carbon, so if there is any silicone content in the mixture, this will be first to be burned off, with silicone dioxide registering on the mass spectrometer.
This will then give way to carbon dioxide and a small amount of carbon monoxide as the carbon begins to oxidise. Finally, when carbon becomes depleted, the overall amount of carbon coming off will drop, and this will mainly be made up by carbon monoxide.
This indicates when the stage known as ‘critical carbon’ has been reached – where most of the carbon has been removed from the mixture and other elements, which the producer does not want to remove from the mixture, will soon begin to oxidise.
Timing
While this process removes much of the guesswork from the technique, it is not without challenges.
To be useful, the data produced by the gas analysis system needs to be made available rapidly and frequently and must be a precise representation of the gas leaving the mixture at any given time. For data points to be delivered to operators with a high enough frequency to identify critical points in the process, this needs to take place in just a few seconds.
This can be achieved through an integrated sampling system that works with the mass spectrometer to automatically cycle the samples in and out. A well-integrated sampling system is able to give a readout every seven seconds, giving operators a close-to-real-time view of the changing gas composition.
The most advanced mass spectrometers on the market are able to give a readout from a sample in a little over three seconds, so the sample system actually has less than four seconds to perform the complicated delivery and cleaning operation.
Different manufacturers use different VOD arrangements, so there is no one-size-fits-all solution to sampling systems, and they need to be designed and built on a bespoke basis. Even practical concerns like the physical size of the system and the accessibility of the read-out monitor can be crucial when integrating a system into an existing facility.
Ultimately, Vacuum Oxygen Decarburization is a critical process in turning low-grade and recycled steel into marketable, high-quality materials for a huge range of applications. For producers to remain competitive, it’s essential that their process runs efficiently, and ability to monitor key parameters is essential in achieving this.
- No related articles listed