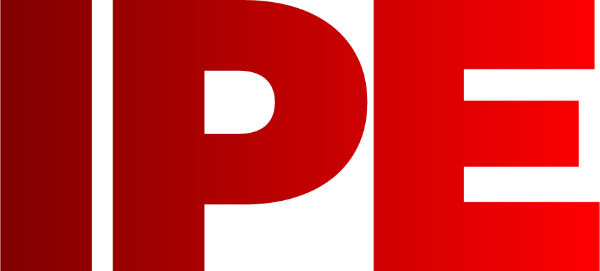
![]() |
Edward Lowton
Editor |
![]() ![]() |
Home> | Production Engineering | >Cutting systems | >Keeping trim with ultrasonics |
Keeping trim with ultrasonics
12 May 2015
There are a number of techniques and processes capable of cutting and trimming the aesthetic components used within a vehicle cabin. However machine builder and system integrator, TEC Systems, chose Telsonics’ ultrasonic technology to provide a clean, cost effective and environmentally friendly solution, within a multi-robot cell used to produce door cap components for Jaguar Cars
The cell, now in full production, comprises four ABB robots, each of which has a Telsonic ultrasonic knife mounted to the robot wrist. The robots work in combination with a rotary indexing system with precision fixturing, which is used to present the component parts to the robots for processing. This robot-based concept provides a highly flexible solution to the application, enabling cutting profiles, angles, speeds and positions to be optimised and easily modified for new or additional part variants.
The system produces the front, rear, left and right hand parts for the new Jaguar XE model. Telsonics’ ultrasonic technology was chosen for this application for a number of reasons, including the high quality edge finish achieved from the process and the cutting speed achievable. The slim profile of the ultrasonic knife also enables easy access to the areas of the component that would be difficult to reach with alternative cutting technologies.
The component parts are manufactured from a composite material – PVC with an expanded PU substrate, and respond well to the ultrasonic knives. The ultrasonic process is said to be quieter and cleaner than a water jet system and there are no issues with fume extraction, which is a requirement when using lasers to cut materials of this type. The compact nature of the ultrasonic knife complements the dexterity of the robot allowing maximum flexibility within the system parameters.
Telsonics’ involvement in the project extended far beyond just the supply of the ultrasonic modules, providing experience and knowledge for the design of component fixture and also performing cutting trials to determine factors such as reactive forces, which in turn influence the cutting speeds attainable. Each of the robots within the production system uses a 35kHz SG3510V Telsonic generator with a SE3512 converter and hardened steel knife. Chilled air-cooling aids optimum cutting speeds and allows the system to maintain the high duty cycles required within the automotive sector.
Telsonic has seen significant growth in the use of its technology coupled with robots and has invested in a 6 axis robot system which has become an important part of its laboratory equipment. This new facility allows Telsonic and its customers to perform trials using production level equipment and, in many cases, actually determine the specific application parameters early in the design and planning stage. Telsonic ultrasonic modules and systems offer high levels of choice for end users, machine builders and system integrators. The companys’ range of ultrasonic modules are also designed to be 'automation friendly', allowing easy integration within stand alone systems and sophisticated production lines.