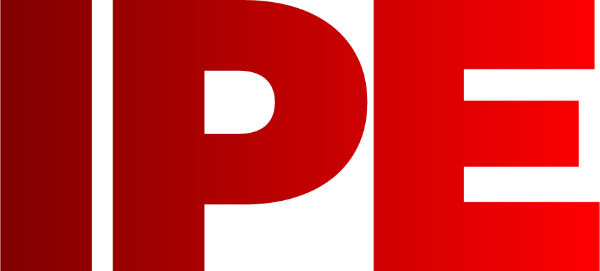
![]() |
Edward Lowton
Editor |
![]() ![]() |
Home> | Plant, Process & Control | >Seals and sealants | >Seals provide savings for sugar refinery |
Seals provide savings for sugar refinery
18 July 2016
Suiker Unie used to rely on packing to seal juice circulation pumps at its Dinteloord sugar refinery in the Netherlands. Typically, after three campaigns the packing on these pumps had to be replaced and, as a result of wear caused by the packing, the shaft sleeves also needed replacing. AESSEAL provided a cost-saving solution
Water used to maximise the life of the packing leaked into the product, and needed to be removed by evaporation. For Suiker Unie saving energy is a key element of its sustainability program, which is why it has a goal to cut energy consumption by 50% by 2030 relative to 2005. Removing the need to evaporate off seal water from the product has the potential to save energy.
In order to address the leakage and shaft wear issues AESSEAL recommended replacing the packing with a CDSA dual seal along with a SW2 seal support system on 12 pumps, coupled with a single FDU installation. Changing from packing to a dual mechanical seal eliminated shaft wear and after six years of operation (approximately seven campaigns) the system is operating without failure.
Savings
The change from packing to double seals with support system has resulted in Suiker Unie receiving tax benefits from the government for saving both water and energy. In order to qualify for this tax benefit; the company must achieve an energy saving of between 0.6 and 1.5Nm³ Natural gas equivalent per invested Euro.
With packing water usage was measured to be 48L/h per pump, giving water usage per campaign to be:
12 pumps x 48L x 24h x 120 days campaign = 1658m³.
1658m³ is 1658 tonne return flow. To evaporate 1t of water requires approximately 100m³ of gas. Total gas usage to evaporate the injected seal water is therefore 165,888m³.
Changing to dual seals with support systems has resulted in no significant leakage of water and therefore saved energy as there is now no requirement to evaporate off seal water. The plant has subsequently installed additional seals and support systems, replacing packing on 43 pumps.
With the upgrade applied to 43 pumps more than 5944m3/year of water will be saved, reducing gas usage by 594,432m3/year. This is equivalent to approximately £181,000/year saving.
The sugar factories at Dinteloord and Vierverlaten operate cogeneration plants to produce steam and electricity they use in the production process during the campaign. Suiker Unie produces more electricity than it actually needs. The company is also working with the Brabant Environmental Federation to reduce its CO2 emissions.
Ab Barendregt, project leader maintenance senior operator, Suiker Unie Dinteloord, comments: “The biggest cost reduction was based on the flush water that went into the process. This water needed to be evaporated. Now Suiker Unie has almost no water entering the process due to the support systems. A smaller cost reduction is based on the energy for the motors. The company needed a lot of energy because of the breaking or chucking impact of the packing onto the shaft. A seal hasn’t got any friction.”