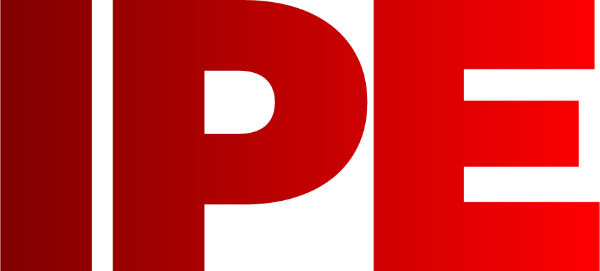
![]() |
Edward Lowton
Editor |
![]() ![]() |
Home> | Production Engineering | >Welding | >£1/4 million investment |
£1/4 million investment
02 October 2016
William Hughes has invested over £1/4 million in a twin robot welding cell to meet growing demand for automotive seat frames.
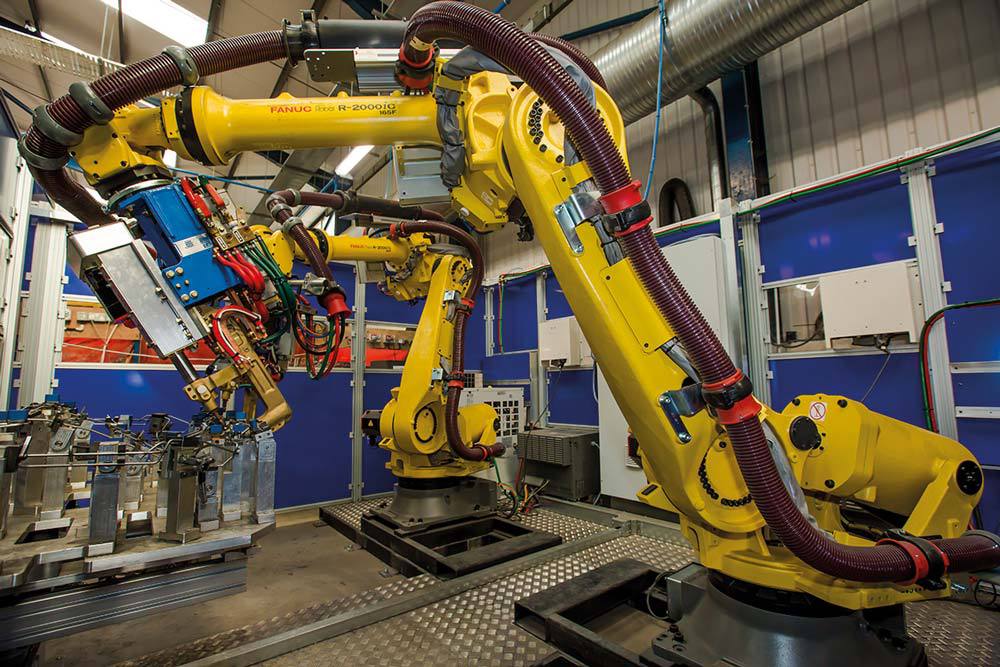
The new welding cell was supplied by Bauromat with Fanuc robots, all installed at William Hughes new headquarters in Stalbridge, Dorset.
The welding cell is in operation 24 hrs/day during the working week and is currently being used for the bulk manufacture of seat frame backs for a SUV. This particular assembly has 56 welds and uses 25 wires. As well as the improved quality and consistency of the finished product provided by the twin robot cell, the welding process is much quicker enabling parts to be produced just 1 minute 40 seconds compared with 3 minutes 45 seconds previously. Furthermore, to ensure throughput speed is maximised, the weld jigs are all designed by William Hughes engineers using latest CAD software and manufactured using CNC milling machines.
- Vacuum formed trays help protect parts
- Wire service
- New capacity springs into action at Wm. Hughes
- Bulgarian growth
- Clean bill of health
- Strong & flexible wire assembly
- William Hughes forecast to cut annual energy costs by £35,000
- Ultrasonic cleaning
- Testing capabilities extended
- Passivation explained and demonstrated