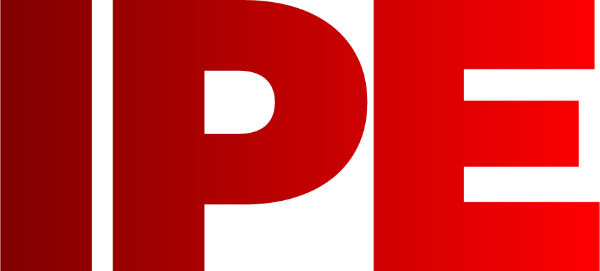
![]() |
Edward Lowton
Editor |
![]() ![]() |
Home> | Handling and Storing | >Lifting equipment | >Route to safe and legal lifting |
Route to safe and legal lifting
16 January 2017
Technology can offer an easier route to safe and legal lifting, as Geoff Holden, chief executive, LEEA (Lifting Equipment Engineers Association), explains
Among many other benefits, LEEA’s recent LiftEx exhibition in Aberdeen provided visitors with a useful insight into the wide range of IT-based solutions now available to support safe and legal lifting programmes. In particular, a number of exhibitors demonstrated how technologies such as RFID and the cloud, coupled with widespread use of tablets and similar connected mobile devices, can dramatically improve the ability to keep track of lifting equipment. What’s more, they can help ensure that all the necessary maintenance, inspection and examination procedures are undertaken – by the right people and at the right time.
Paper trails
Most readers will be aware of the need to maintain proper ‘paper trails’ for lifting equipment. In the UK, LOLER (Lifting Operations and Lifting Equipment Regulations) requires that all lifting equipment is subject to periodic thorough examination by a competent person. A written report of the examination also needs to be completed, and issued to the employer in question.
In many cases, this can involve dealing with a large number of small and hard to distinguish items. To further complicate matters, sectors such as the offshore and entertainment industries are typically characterised by numerous remote, and often short-lived, working locations. Ensuring that every single piece of equipment has been subject to thorough examination, and having the records to prove it, can prove a real challenge.
Hi-tech solutions
For many employers, traditional methods, such as the use of colour-coded tags or stamping relevant information into the body of the equipment, work perfectly well. But the new wave of ‘hi-tech’ solutions make it possible to electronically embed into each item a full history and all the relevant requirements in terms of servicing, testing and thorough examinations, for example. This information can be instantly accessed via a mobile device. Furthermore, the information can be updated as soon as any work is completed, and the records securely backed-up in a central digital archive. As and when checks are made, employers can easily retrieve all the necessary, up-to-date reports. Administration is streamlined, and the risk of human error reduced.
One of the most common observations made of the lifting industry is that much of the equipment involved seems to have changed very little over the course of time. At a glance, it may be true that the physical appearance of products such as overhead travelling cranes and hoists has remained remarkably consistent. But dig a little deeper, and it becomes evident that the development and introduction of new solutions is continuing apace. Indeed, LEEA itself is very much committed to the effective use of IT.
Training
For example, the LEEA Academy now offers students the latest online and interactive training tools. The association’s TEAM card, issued to engineers who have passed the industry-recognised Diploma examination, can be verified in seconds on the LEEA website. And we are currently putting the finishing touches to a new mobile app that will prove invaluable to workers responsible for undertaking thorough examinations.
Overall, the message for end users of lifting equipment is clear. Whilst tried and tested procedures will still suit many employers, others could find that a little research into the industry’s latest advances reaps rich rewards in terms of improvements to safety, efficiency and legal compliance.
- LEEA releases GLAD2023 Mission Statement
- LiftEx revamped for 2015
- An event-full time for LEEA
- LEEA shines a light on the essential yet often overlooked Lifting Industry
- The Lifting Equipment Engineers Association has announced a new leadership team
- LOLER: Time to voice support
- Oliver Auston named new LEEA chair
- Longer-lasting LiftEx
- Open Programme delivery for Lifting Apprenticeship in England
- Making training a safe investment