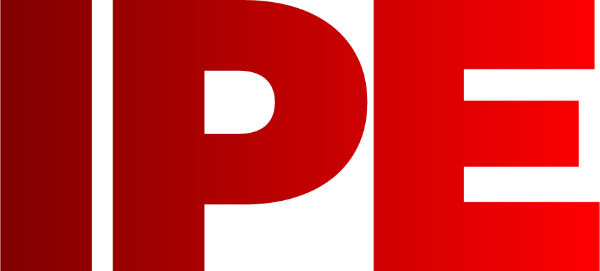
![]() |
Edward Lowton
Editor |
![]() ![]() |
Home> | Energy Management | >Compressors & ancillary equipment | >Saving compressed air system costs by reducing leaks |
Saving compressed air system costs by reducing leaks
01 December 2023
IMPROVING THE energy performance of compressed air systems continues to be a high priority amid soaring electricity prices. In this context, a planned approach to reduce pipework leaks can reduce ownership costs.

In April last year, the British Compressed Air Society (BCAS) launched the 10% Taskforce - a call for UK businesses to take simple steps to cut their compressed air energy usage figure by 10%. The campaign has an ambitious target to save over 411 thousand tonnes of CO2, the equivalent of taking 317 thousand cars off the road.
When BCAS launched the campaign, no one could have predicted the scale of the rise in the wholesale gas and electricity prices. The campaign’s original calculations of £485.43m being spent in wasted electricity have now risen two or even three-fold.
Generating compressed air can be very energy intensive, representing as much as 30% of a site’s total electricity bill. According to a report entitled 'Compressed Air Systems in the European Union', when looking at the most important energy savings techniques available to compressed air users, "the energy savings amount to 32.9%, achievable over a 15-year period".
Therefore, since the launch, BCAS members have been speaking with customers to encourage them to act and to dispel some of the commonly held beliefs that saving energy will require significant investment in new capital equipment.
In particular, the Society is advocating small, incremental steps and demonstrating the significant impact these can have on reducing energy consumption.
One of the key areas that can help avoid wasteful practices is to fix air pipework leaks and implement a regular monitoring procedure.
Why fix leaks?
All compressed air systems experience leaks and in the past this may have been ignored, as they either pose no immediate health and safety concerns, or the cost of repair outweighs the energy savings achievable. However, the current climate means that users are much more aware of the energy which is being wasted and the costly effects of leaking air.
BCAS members are reporting that where they have performed energy audits in the past, and the survey did not recommend any action was required, these are now worth revisiting. The rising energy costs have brought these surveys back into focus as providing viable maintenance actions.
One 2mm hole in the pipework could cost over £1,249 per year in wasted energy, and so it’s more important than ever to take measures to reduce air leaks.
Source of the leak
There a four common leak sources to be aware of, these include:
- Air-using equipment left running when not required
- Manual condensate drain valves left open
- Leaking hoses and couplings
- Leaking pipes and pipe joints
It is important to check these areas regularly, as leaks need to be monitored constantly. It is recommended that operators conduct a leak survey at least twice a year, to keep abreast of any changes or modifications required to the system.
Under pressure
When pressure drops in the system it means the generating pressure is set much higher than necessary. To resolve this issue, engineers should start by identifying where the pressure drop originates and take action to fix the cause and regulate the pressure.
The issue of a drop in pressure could be due to:
- Leaks
- System component constrictions (e.g. valves, bends)
- Undersized piping
- Pipework installation (e.g. no ring main)
- Aged pipework with increased friction
Identify the leak
As air leaks aren’t hazardous to health and safety, it is easy to become complacent if there is a small leak. However, as mentioned a small leak can have significant effects on energy usage, so it is important to take action.
A simple place to begin is to conduct an out-of-hours survey and to walk the site listening for any leaks - it should be easy to hear any leaks when the site is quiet.
Following the survey, a leak management programme can be implemented, marking the leaks, recording them on a site plan and grading the priorities, such as fixing the largest leak first.
Finally, users should be encouraged to report leaks so they can be identified and repaired as soon as possible.
Pressure reduction
Once any leaks have been repaired, then it’s advised to discuss with the supplier about reducing the generation pressure at the compressor. Understanding the system pressure is critical when it comes to leakage reduction and reducing energy usage.
Fixing a leak will increase the pressure of air. This can not only have an impact on the system’s energy consumption, but also put any projected savings at risk.
The pressure drop should be less than 10% of the compressor’s discharge pressure, as measured from the compressor outlet to the point of use.
If one section of the plant requires much lower pressure, it is recommended to run a dedicated low-pressure compressor or to regulate the pressure down that line.
When it comes to the energy used, on average it is found that for every 1 bar g additional generation pressure there is a loss of 7% in specific energy. And so, keeping pressure low can help to reduce operating costs.
Zone out
The design and installation of the pipework can help with saving energy and so when considering leak reduction measures, it’s important to consider the pipework currently in place.
The following are examples of how sites can alter the pipework to be more efficient:
- Spilt the system into zones and pressurise each as required
- Remove or isolate redundant piping
- Use vales to isolate parts of the distribution network
- Select large radius bends instead of elbows
- Support piping to minimise movement and sagging to reduce leaks and build-up of fluid
- Replace older pipework with modern materials to reduce friction
Not all parts of the network operate to the same hours or pressure and so it is possible to save energy by zoning the compressed air system.
For more information, please speak to a BCAS member who can assist in this area by emailing [email protected]. And you can download a free copy of the leak-fixing guide here: tinyurl.com/327ywa4z
Tel: 0207 935 2464
- Simple steps to compressed air energy savings
- Getting to grips with legal matters
- BCAS offers new working safely during Covid-19 training course
- Original way to boost efficiency
- Air receivers: Focus on facts
- BCAS expands team with the appointment of second technical officer
- Gaining skills for life with BCAS
- BCAS reiterates air treatment advice for COVID-19 concerns
- CSCS card update: The current state of play
- Taking an energy-first approach to compressed air system design