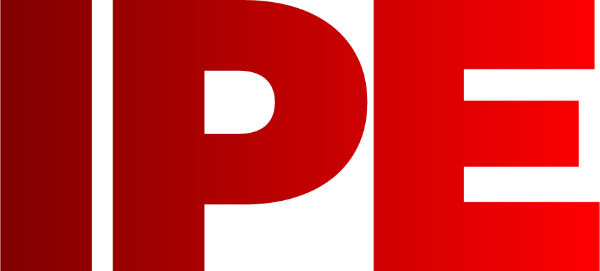
![]() |
Edward Lowton
Editor |
![]() ![]() |
All things electric
09 October 2019
With government ambition for all new cars and vans to be effectively zero emission by 2040, Charlotte Stonestreet considers some of the challenges and opportunities around the manufacture of low emission vehicles.
There’s no doubt that low emission vehicles are big news, and they seem to be on the cusp of big business too. Earlier this year the UK Government awarded £25m to projects across the country to develop ground-breaking zero emission technologies for new vehicles. A key part of the government’s Industrial Strategy, the funding is also part of wider efforts towards developing a net zero carbon economy.
One project aims to develop innovative, new electric motorcycle technology lowering vehicle emissions and noise, with faster battery charge times and making electric motorbikes attractive to the market. Led by Triumph Motorcycles, it adds award-winning motorsport and electrification experience from Williams Advanced Engineering, propulsion innovation from Integral Powertrain and Warwick Manufacturing Group’s success integrating academic research with public and private sector projects.
Other winning projects include a project that will add an electric drive axle to a conventional diesel-powered truck, creating a hybrid engine which will store and reuse the electrical energy on the trailer; a research and development project to replace metals with new materials using recycled carbon fibres from aviation waste; and a feasibility study into the potential of hydrogen fuel cell technology as a zero-emission solution for utility and off-road vehicles.
Support for these projects is key to the delivery of the government’s modern Industrial Strategy’s Future of Mobility Grand Challenge and the Road to Zero Strategy, both of which aim to put the UK at the forefront of the design and manufacturing of zero emission vehicles. This transition is also a crucial part of the UK’s move to a net zero emissions economy to end the country’s contribution to global warming entirely.
The government’s ambition is for all new cars and vans to be effectively zero emission by 2040. The numbers of ultra-low emission vehicles on UK roads is currently at record levels, with around 200,000 ultra-low emission vehicles registered in the UK.
However, despite all good intentions, there is a danger that the UK will fall behind when it comes to electric vehicle production. The the need to heavily invest in new production facilities and supply chains, combined with Brexit uncertainties, is creating a perfect storm with many of the major automotive manufacturers choosing to invest in mainland Europe over the UK.
According to research carried out by Reuters using public data, global automotive companies are planning to invest at least $300b in electric vehicles over the next five to ten years. Of this, just $2.34b is coming to the UK in the form of Jaguar Land Rover’s plan to offer electric versions of all it’s vehicles by 2020.
There is also the issue of slow take up of the technology with consumers. Despite the Tesla Model 3 being the UK’s third best selling car in the UK this August, with 2082 new registrations, electric vehicles still present only 1.1% of new cars sold in the UK. There are very few electric cars available on the second hand markets, and with UK drivers taking up to 15 years to change their cars, this doesn’t look like a situation that is due to change soon.
And even if the UK public did suddenly buy into the electric vehicle concept, there are questions over the infrastructure needed to keep motoring. Addressing this, The Treasury has launched a £400 million fund to bolster Britain’s electric vehicle charging infrastructure, with the first £70 million allocated for 3000 charge points – more than doubling the number across the UK to 5000.
Rapid charge points can recharge a family car in as little as 20 minutes, compared to existing technology which can take 40 minutes- making the reality of driving electric vehicles easier and more accessible for people across the country.
A review is currently underway to explore the provision of charge points across major road networks, meaning drivers could charge their car whilst stopping for a coffee at a service station. The investment complements £1.5b support to boost the uptake of electric vehicles and make cleaner vehicles more accessible to everyone – part of the Government’s ambition to end the sale of petrol and diesel vehicles by 2040.
Always at the forefront of electric vehicle technology, Schaeffler is entering the electric motor manufacturing sector with a modular, highly integrated technology platform. This family of electric motors is designed for efficiency and a good price/performance ratio, and potential applications range from hybrid modules and dedicated hybrid transmissions (DHTs) through to electric motors for electric axle drives.
Voltage ranges from 48V to 800V and performance classes from 15kW to over 300kW are possible. Volume production for a range of customer projects worldwide is set to begin in 2021. Schaeffler’s worldwide network of manufacturing plants and special machinery and tool manufacturing facilities will be used to set up and operate the production lines.
Electric motors for P2 hybrid modules are subject to special requirements, as their design means that they run at the same speed as the internal combustion engine. Minimal axial length and ample free space inside the rotor for the integration of clutch and release system ensure the necessary high packing density for this application. Single-tooth winding allows extremely small axial installation spaces. Both 48V and high-voltage motors with ratings of 15 to 120kW are available.
As the hybrid module is designed as a dry system, the stator is actively cooled using a cooling jacket. In systems with a wet clutch, the oil that is available can also be used to lower the temperature of the electric motor, which leads to significantly better heat dissipation and thus higher continuous output levels. However, the best type of power loss is the one that never occurs in the first place, which is why the motors are optimised for high efficiency across a wide range of data map areas.
Depending on the design envelope, the same can apply for electric motors in dedicated hybrid drives. These transmissions are usually designed in such a way that more axial installation space is provided for the electric motors, which rotate faster. Output levels of 80 to 140kW are common. Depending on the transmission and powertrain operating mode, these motors work together with the internal combustion engine as motors or generators, and their efficiency characteristics are optimised in accordance with the utilisation profile.
As a result of the all-electric driving modes of plug-in hybrids, their acoustic behaviour becomes a prominent factor. In many cases, the use of distributed windings is the right solution. To this end, Schaeffler has defined a second standard winding solution, for which the production machinery is also developed in-house. The method in question is bar wave winding, which Elmotec Statomat is constantly refining at its location in Karben. To provide a specific application, a traction machine was developed that has an overall axial length of 137mm and delivers 125kW of power and 310Nm of torque.
The portfolio is completed by a range of electric motors for driving electric axles. These cover both high-voltage 2 (400V) and high-voltage 3 (800V) ranges, and outputs of 100kW to 300kW are possible. If the system design permits, these motors are configured for high maximum speeds of up to 20,000rpm, which allows the advantages of bar wave winding to be fully utilised. The high number of stator grooves means that the temperature is lowered effectively and leads to a rotating field with a low number of harmonics. This results in two advantages: a high power density and an excellent level of efficiency.
Centres of excellence
Schneider Electric has collaborated with Edmundson Electrical to open four Electric Vehicle (EV) Centres of Excellence. The centres, in Manchester, West Bromwich, Glasgow and Twickenham, are partnered with Schneider to develop expertise around smart, interoperable EV charging systems. This will support contractors in meeting growing EV infrastructure and energy demands.
Since 2015, the number of ultra-low emission vehicles has quadrupled. As the market continues its rapid growth, the demand for EV energy management system knowledge will increase. As EV charging systems scale in size and complexity, the opening of the centres will enable Edmundson Electrical and Schneider to deliver expertise, training and support to the UK EV charging installation market.
Charge point solutions
The RAY: Smart Charge Point Communications Controller from embedded systems consultancy ByteSnap Design is a smart charge point communications controller supporting both AC charge points and DC chargers using the latest communication standards.
RAY has been developed to meet specific new regulations. “The UK government says that any charge point eligible for an OLEV [Office for Low Emission Vehicles] grant must be “smart”. This regulatory requirement has only just come into force and means that charge points must be controllable to help load balance the electricity supply network and prevent overload and permanent damage,” says ByteSnap director, Dunstan Power.
“In addition to meeting the government’s latest regulations, our robust, new products will help charge point manufacturers and installers effectively develop competitive charge points whilst meeting customer demand. They’ll also work well within the existing power infrastructure.”
Cable management
Of course, it isn’t just the chargers that are seeing an upsurge in demand. The continued growth in the production of electric vehicle charging stations is driving an increase in demand for the range of cable management products offered by Buttkereit from UK manufacturers of these systems.
Although electric vehicles and their charging technology are at the forefront of today’s automotive industry, the process of building the charging stations has much in common with manufacturing other electrical or control panels. Panels of all types have multiple cables, and proper management of the different types and sizes of cable being installed is essential if the highest levels of safety and reliability are to be achieved.
Earlier this year Buttkereit enhanced its cable management portfolio through a new partnership agreement with Italian manufacturer Detas SpA, and has a broad range of solutions available for manufacturers of EV charging stations. Certain cables are pre-terminated, and to avoid potential reliability and warranty issues, it is essential that these cables can be installed without removing the original connectors. This is achieved using the DES system that comprises of a selection of frames and inserts. The frames have been designed to be capable of accepting multiple insert types, to provide the highest level of flexibility in cable sizes and configuration.
For standard, non-terminated cable types, the range includes a wide selection of gland plates. This part of the DES range offers an innovative alternative to the standard cable glands often found on electrical and electronic cabinets and equipment. The cable is pushed through a front membrane, whilst an integrated second membrane increases the strain relief and liquid resistance. The comprehensive range offers protections levels up to IP66, strain relief to EN 62444 and a sturdy construction rating up to IK10.
User friendly infrastructure
The HARTING Technology group has formed a successful partnership with Swiss automotive company Rinspeed to develop a number of e-mobility solutions including an expanded e-mobility infrastructure for the automated fast charging of electric vehicles. At the Geneva International Motor Show earlier this year, Rinspeed presented the microSNAP, the latest vehicle study by Swiss car visionary Frank M. Rinderknecht, alongside HARTING’s solutions for automated charging.
“The breakthrough for e-mobility crucially depends on the duration of the charging process and user-friendly charging infrastructure,” says Rinderknecht: “Long charge times and unwieldy, heavy-duty connectors deter car owners from switching to electric vehicles, making rapid charging via compact DC connectors an essential prerequisite to speed their widespread adoption.”
With fast charging via a DC charging plug such as HARTING’s DC Combo 2, future vehicles will be supplied with sufficient power in just a few minutes rather than in hours. In addition, automatic charging solutions will increase in popularity, since handling today’s larger charging infrastructure systems limits their usage in space-constrained environments such as car parks or garages.
Compact connector system
Developed to meet the demanding requirements of electric and hybrid vehicle drivetrains, the new PerforMore connector system from Stäubli Electrical Connectors can carry a continuous current of 400A or more with minimal power loss.
The rugged devices are suitable for connecting the whole drivetrain, including batteries, inverters, motors and high voltage distribution units. Their low contact resistance is due to the company's proprietary MULTILAM multi-contact system, which also guarantees strong resistance to vibration and elevated temperatures.
The PerforMore is exceptionally compact, with a pitch only usually found with significantly lower current ratings, while maintaining the clearances and creepage distances necessary for high operating voltages. In the mated condition in particular, its low profile gives a clear advantage in the efficient use of available vehicle space.
Installation is quick and easy, while disassembly is user friendly and safe, with protection against accidental disconnection and arc flash. This is due to a two stage unlocking system which ensures the high voltage interlock loop is interrupted in the first stage before disconnection of the live contacts in the second stage.
The two pole connector has 10mm diameter contacts and is rated at 1000V, as defined in LV215 standards. Robust and reliable, it features ingress protection to IP67 and IP69 according to IEC 60529 when mated, and IP2X unmated.
Mechanical keys and colour coding offer additional flexibility and safety if using more than one connector in a vehicle, by eliminating the risk misconnections.
A high number of evenly distributed contact points in the power contact shielding ensures high quality 360 degree EMC shielding even at high frequencies.
Autonomous Vehicles
The latest release of ANSYS Autonomy, part of ANSYS 2019 R3, enables engineers to develop safer autonomous vehicles (AVs) through advanced closed-loop scenario simulation, automated driving and control software development, functional safety analysis, and sensor, camera, lidar, and radar simulation.
AVs require rigorous testing in complex environments and under variable conditions. Physical testing would require billions of miles of driving – a time-consuming, cost-prohibitive, approach. Using simulation to virtually test AVs is the only viable option for validating systems safety and accelerating AV development.
From sensors to virtual environments to artificial intelligence (AI), ANSYS 2019 R3 includes robust offerings that speed the safe development and deployment of AVs.
- Cyber attacks climb
- HSE announces collaboration with SHW Live
- TREND Networks receives gold
- Combining sustainability with lifting power: Sarens introduces new SGC-170
- IP&E Awards extends deadline for entries
- Lorien appoints duo of directors
- New CEO for intralogistics maker Agilox
- UK's first open access 'pay-as-you-go' factory
- WEG to produce artificial ventilators for COVID-19 patients
- Cyber attack on steel mill causes physical damage
- No related articles listed