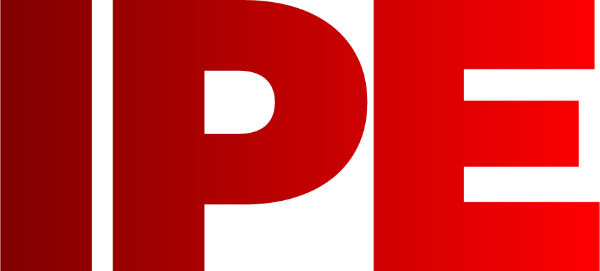
![]() |
Edward Lowton
Editor |
![]() ![]() |
Home> | Efficient Maintenance | >Industry 4.0 | >Charting the industrial data solutions landscape |
Charting the industrial data solutions landscape
14 July 2023
With an increasing number of ways to monitor, measure and analyse data, it can be a challenge for organisations to identify the right industrial data solutions for them. Richard Jeffers discusses some of key considerations to keep in mind.

THE ROLE of industrial data solutions as a facilitator for increased operational efficiencies, production scalability and downtime reduction - all essential elements in a fast-paced, competitive arena - is well-recognised, and not just by those organisations who benefit from using these solutions. Many new start-up businesses have flooded the market in recent years, in accordance with the size of the opportunity, offering an array of data services.
With so many ways to monitor, measure and analyse data, and so many players emerging in the market, it’s not surprising that organisations looking to make the foray into industrial data solutions may be put off by the sheer scale of the options available. Add this to the other potential barriers and challenges industrial firms face: legacy equipment, disparate systems, skills gaps and cyber security concerns, and a no-brainer can quickly become a non-starter.
Starting simple and growing smart is a mantra to work to, but deciding where to start and with which solution or partner is a decision that should be carefully researched and considered.
Conquer the fear of the cloud
Without doubt, any industrial firm looking to embark on or expand data solutions should be focusing on cloud over on-premise options. The industrial Internet of Things (IoT) often requires significant amounts of data processing and storage which, if facilitated on-premise, would be very costly to implement and expand. The cloud offers the ability to scale up or down in accordance with business needs, without having to worry about hardware limitations, expensive maintenance or upgrades. For businesses that may not have the resources to invest in and manage their own IT infrastructure, this is a particular advantage.
The accessibility afforded by cloud solutions is also unrivalled: as long as there’s an internet connection, industrial IoT data can be easily shared across departments or even multiple locations. This is essential for businesses that need to make real-time decisions based on data collected from multiple sources. Cloud solutions are also often easier to integrate with other software and systems than on-premise solutions, which can be crucial for businesses that need to connect their industrial IoT data with other enterprise systems like ERP, CRM or MES.
Security often presents a barrier to adoption, but cloud solutions typically have robust measures in place to protect data, crucial for industrial IoT solutions that involve sensitive data related to manufacturing processes or supply chain operations. And in an arena where the biggest business inhibitor is standing still, innovation is constant in cloud solutions, which evolve and improve so businesses can benefit from the latest features and technologies without having to invest in new hardware or software upgrades.
Gleaning data wisely
There is a huge assumption that a plethora of sensors and monitoring equipment need to be installed, and with the cost of monitoring technology drastically reducing over the last couple of decades - making it much more accessible - many firms have gone down this route without really knowing what to do with the data. The truth is that industrial plants are often ram-packed with data, far too much of it from a variety of sources, and less than 20% of it is used in any decision-making.
This data is often disparate, sitting in silos making it difficult to gain insights from and therefore at best, restrictive, and at worst, useless. And this is where many will fall for the glitz, glamour and claims of start-up solutions providers which often do a great job of telling a story, but unless they have the real foundation, experience and expertise to guide and advise the customer on how best to glean the insights they need, aligned with their objectives, the solutions may fall short. Another consideration should be the capability of the software to integrate with a variety of equipment brands and types. Solutions that are brand agnostic are a must in the industrial environment, where equipment and technology investments span decades and therefore won’t be all one brand, type or generation.
As the data solutions offering has exploded in the industrial space, there should also be considerations around longevity of the provider. With many start-ups having received funding from venture capital investors, a downturn in funding for these providers could hinder or halt the solution. This would be spell disaster if a significant investment has been made in the solution by an industrial operator. The best case could be disruption in the service and the worst could be a total loss of data and solution capability. This is likely to become a growing issue over the next decade.
Use specialists to help unlock low-hanging fruit
Many organisations know data extraction and analysis is key to business growth but don’t know where to start on what to measure from the magnitude of available data, and why. Using a firm that is underpinned by industrial engineering expertise and, therefore, which understands the sector, combined with expertise in the process control environment and IT integration, and knowledge of digitally connecting a range of new and legacy assets, is key.
They will help identify the useful data that is freely available in the factory, locked away in equipment, and then ascertain where the gaps are so the right equipment can be implemented to address this. Extracting and analysing data so that predictive maintenance can be optimised, production downtime minimised and energy saved to help meet sustainability goals is a process that, with the right approach and knowledge, can be achieved in weeks, not months.
A consultative approach will help an organisation develop key performance indicators (KPIs) and objectives, using experience and specialist knowledge of not just the technology but the sector as a whole, helping unlock value. A modular solution approach means the most critical assets can be prioritised as a starting point, with the plan to expand as value is realised.
Accelerating digitisation
Adoption of digitisation is moving slower than anticipated in the industrial space and there’s no doubt some are burying their head in the sand because of perceived barriers. While others are too busy putting out fires and being reactive to crises to dedicate the time to developing a predictive maintenance strategy based on digitisation. Some are digitising without knowing what problem they’re trying to solve. But with the cost of production downtime costing up to £10,000 per hour, the cost of doing nothing is high.
Continuous operational insight of plant and processes is key to survival in the industrial world, and firms must get on board and commit to digitally connecting new and legacy industrial assets to achieve this. With the array of solutions and services available to help, from the first top-dip phase through to expansion of digital solutions integration, it's time for heads to emerge from the sand.
Richard Jeffers is managing director of RS Industria
For more information:
Tel: 0333 247 0235
- RS releases Performance in Focus 2024 Maintenance Engineering Report in partnership with IMechE
- New contactor series delivers reduced energy consumption in industrial machines
- Non-sparking maintenance tools
- Guess-free decision-making
- RS Components launches 7-in-1 oscilloscope
- Enhancing Operational Efficiency and Sustainability with Vendor-Managed Inventory Solutions
- Certainty doesn't happen by chance
- RS releases Environment, Health and Safety industry report 'Improving the Standard' 2025
- RS Components wins ninth consecutive RoSPA award
- Driving F&B exports with a proactive maintenance approach
- Technology and Open Standard data enabling smart maintenance
- Broadband sensors: Pinpointing leaks in compressed air systems
- Mechanised welding, cutting and Industry 4.0
- Tomorrow’s tech is here today
- Investment in infrastructure, innovation and people
- Getting to 4.0 – one hard-won gain at a time
- Digital transformation in the chemical industry: White paper
- Digital industry around the world
- Guidance via AR
- How machine learning is transforming predictive maintenance