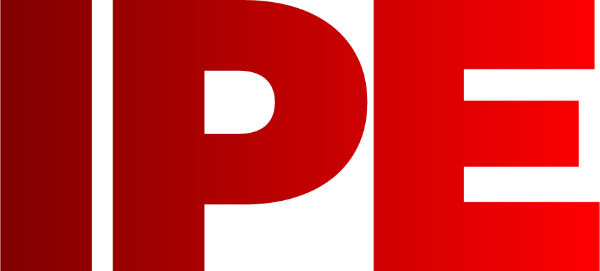
![]() |
Edward Lowton
Editor |
![]() ![]() |
Home> | Efficient Maintenance | >Maintenance products | >Component repair times cut with laser metal deposition |
Component repair times cut with laser metal deposition
09 July 2021
MANY INDUSTRIAL applications harbour challenging operating conditions such as corrosive or erosive atmospheres and high temperatures. Every component of rotating machinery used in these conditions needs to operate reliably to ensure an extended overall service life for the equipment. In many cases, specialist coatings form an important part of the design from the original equipment manufacturer (OEM) (or upgrade) and these must be reconditioned or improved during any maintenance project.

Laser metal deposition (LMD) is a repair technique that can be used for the restoration of many components used in rotating equipment similar to methods like conventional welding and high velocity oxidized fuel (HVOF). The range of repairs that can be achieved using LMD is extensive. From restoring worn bearing journals and seal areas to renewing steam turbine blade leading edges and the impeller vane tips of pumps.
The laser in the LMD repair process offers benefits beyond what both HVOF and submerged arc welding provide. The most obvious is the reduced heat input, which minimises distortion, reduces the heat-affected zone (HAZ) and almost eliminates the need for post-weld procedures. At the same time, the metallurgical bond of LMD assures excellent consistency in material density and perfect adhesion with the parent material of the component.
LMD is the latest addition to HICoat’s range of solutions, offering a variety of materials including Inconel 625 and Stellite 6 as well as others for hard-facing, improved corrosion resistance, and general dimensional restoration.
With over 25 years’ experience in delivering coating solutions for rotating equipment, Sulzer HICoat has extensive in-house expertise and cutting-edge facilities to ensure the best solution is delivered for every project. LMD can be used to re-establish original dimensions in the repair of shafts up to 23ft (7m) in length and 50,000lbs (25 tonnes) in weight, impellers measuring up to 94in (2.4m), casings and diaphragms.
Combined with precision machining facilities, Sulzer offers a fast and effective repair service for all types of rotating equipment using the most effective solutions available. LMD is just one more technique Sulzer uses to help operators minimise downtime and extend the working life of important assets.
- Improving motor spec to boost pump efficiency
- Custom white metal bearings
- Sulzer installs six HST 20 turbocompressors for Severn Trent
- Pump retrofit project paid off in weeks
- Turbocompressors boost efficiency at wastewater plant
- Sulzer launches new features for AHLSTAR
- Challenging offshore motor rewind
- Sulzer begins Baton Rouge expansion project
- AHLSTAR improves sump pumping in cardboard mill
- Effecting sustainable change