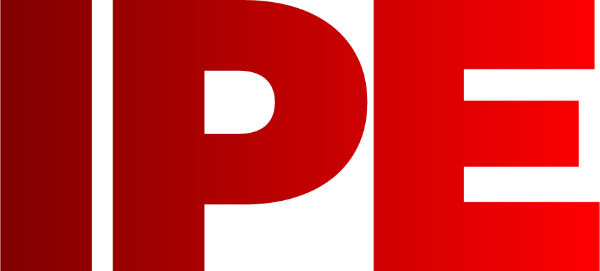
![]() |
Edward Lowton
Editor |
![]() ![]() |
Home> | Handbooks | >Manufacturing Matters Ireland | >Cutting welding time and cost |
Home> | Production Engineering | >Welding | >Cutting welding time and cost |
Cutting welding time and cost
10 March 2019
ESAB has reduced welding time and cost for one of its customers.
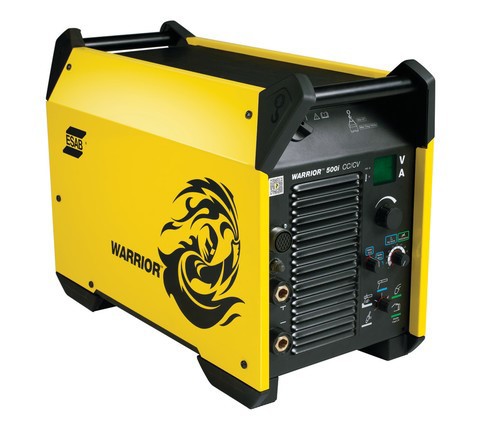
A common requirement in the construction sector is the production of H-section or I-section structural beams by joining three plates. Often the material will be rusty mill scale plate that has to be welded directly without any preparation. Cost pressures mean the welds must be made as quickly as possible and the need for rapid, trouble-free on-site assembly dictates that distortion and deformation are not acceptable.
ESAB was recently approached by a customer with exactly the requirement outlined above. In this case, a 10 x 470mm web needed flanges to be attached along both edges; the flanges were 15 x 200mm and one needed to be attached at an angle rather than being perpendicular to the web. At the time, the customer was using manual MIG welding with OK Autrod 12.51 copper-coated solid wire 1.2mm diameter. With a wire feed speed of 7.2m/min and a welding current of 240 Amps, the customer was achieving a welding speed of 30cm/minute, which equates to 3.65kg/hour and a predicted total welding time of 800h at a cost of €8.8/m.
Clearly some form of semi-automated welding would improve the situation and it might be thought that the obvious answer is to use the best technologies available, such as pulse welding that reduces heat input and, therefore minimises distortion. However, this is still a relatively time-consuming process that would require two welding operatives.
ESAB’s recommended approach was to ‘think outside the box’ and use a pair of Warrior 500i water-cooled machines, each with a Miggytrac B501 tractor unit, and Coreweld 46 LS metal-cored welding wire 1.2mm diameter. This enabled the rusty mill scale plate to be welded on both sides simultaneously to minimise distortion and deformation while still achieving the required throat thickness of a5 in a single run. Furthermore, a single operative can operate two Miggytac systems concurrently, providing the customer with substantial cost savings.
With this setup, the wire feed speed was 16m/minute and the welding current was 340A at 36V. This enabled the welding speed to be raised to 55cm/min, laying down 7.2kg of weld metal per hour. As a result, the calculated welding time is better than halved, from 800 to 300h, and the cost is similarly improved from €8.8 to €3.9/m. Most importantly, the reduced time and cost did not compromise quality, as, despite the faster welding, there was no longitudinal deformation.
Equipment and consumables
The recently introduced Warrior multi-process welding machine can perform MIG/MAG, flux-cored wire, manual metal arc (MMA) and TIG welding tasks as well as arc gouging. Featuring inverter technology for energy savings and greater functionality, the Warrior delivers up to 500A at a 60% duty cycle. It welds 0.8 to 2.0mm flux-cored, metal-cored and solid wires, carbon arc gouges with electrodes up to 10mm diameter and has a full range of MMA capabilities. The Warrior machine incorporates ESAB's TrueArcVoltage technology to ensure the arc voltage is maintained accurately under all operating conditions to achieve high-quality and more consistent welds. For the project described above, the Warrior was specified with the optional water cooling unit.
ESAB’s Miggytrac B501 and B5001 tractor unit for semi-automated straight-line arc welding is suitable for fabricating beams. Compact, yet robust and capable of producing high-quality welds, the Miggytrac B501 and B5001 incorporates a carriage travel speed from 0-130cm/min (for the B501) and a 0-170cm/min (for the B5001). They are quick and easy to set-up with almost no learning curve. Features such as programmable start and end sequences with back fill and crater fill and accurate programmable intermittent welding with high travel speeds between welds (B5001) ensure high quality and high productivity, reliability, repeatability and efficiency. Both models have a bulletproof 4 Wheel drive with high acceleration accurate stepper motor control for constant travel speed for more welding time and less downtime
Coreweld 46 LS is a new-generation metal-cored wire that has been developed for the welding of thinner plates with a minimum thickness of 1.0mm. It is said to offer a faster and higher-quality alternative to using solid wire. An absence or very low levels of silica on the weld surface and minimal spatter result in reduced post-weld cleaning. ESAB says the Coreweld 46 LS considerably reduces the welding costs for mechanised and robotic fabrication.